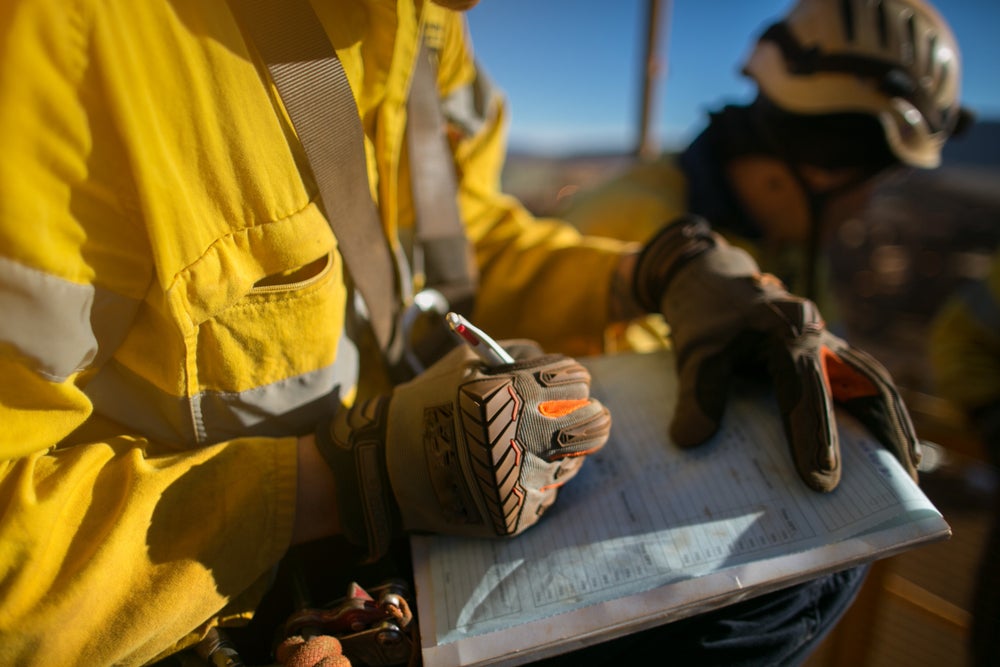
Mining’s safety record, globally, is self-evidently improving for the better, year on year. A renewed focus on safety and adhering to strict protocols across the sector has, thankfully, delivered encouraging results.
“Safety is without doubt the highest priority of all mining companies and all have policies and processes in place, and continuously strive to improve the safety of their workers and contractors on the mine site. Metrics such as the lost-time injury frequency rate (LTIFR) and total recordable injury frequency rate (TRIFR) have fallen steadily overall over the last few years,” says David Kurtz, Director – Mining & Construction, GlobalData.
According to GlobalData’s figures, LTIFR was on average 1.52 per million hours worked in 2021, down from 1.87 in 2017 and TRIFR was 3.08 in 2021 down from 4.17 in 2017, falls of 19% and 26%, respectively, says Kurtz.
Meanwhile, The Safety Performance Report in 2022 by the International Council on Mining and Metals (ICMM) benchmarked the progress of its members during 2021 and the findings indicated steady, incremental improvements in mine safety, with a total recordable injury (TRI) frequency rate at 2.90 – down from 5.07 from records a decade ago.
At the time, the ICMM noted that the mining sector has unilaterally implemented “operational, cultural and leadership transformation” to help reduce and minimise fatalities over recent years.
Those same measures, allied with an uncompromised compliance towards safety protocols and a continued investment in cutting-edge innovation to ensure for a safer environment, has seen BME, a leading provider of explosives and blasting technology and services and part of the Omnia Holdings Group of companies, go even further in its pursuit of safety across its blast sites, globally. Following five years of implementing its Safety for Life brand, the Omnia Group company has successfully reached a primary tenet of the organisation’s safety targets, a zero recordable case rate (RCR), for the year ending March 2023.
The RCR is calculated on the amount of safety incidents that resulted in treatment beyond first aid for an individual. To achieve zero is remarkable considering the inherent safety issues associated with the blast process and a vindication of how successfully ingrained Safety for Life has become in the working culture within the mining division of the Omnia Group company, BME.
“We consider our zero RCR over the preceding 12 months as a proud landmark to have reached, based on the positive safety culture that our Safety for Life initiative has fostered within the business,” said Ramesh Dhoorgapersadh, General Manager for Safety, Health, Environment, Risk and Quality (SHERQ) at BME.
Dhoorgapersadh believes that the fundamental reason behind the zero RCR is not only BME’s safety strategy and systems, but in “the committed and practical application” of these principles each day from its entire workforce.
“Companies’ systems and processes often look very good at face value, but these need to be effectively translated into action,” he says. “A RCR of zero does not happen overnight and requires constant reinforcement from the highest level before it forms part of the prevailing culture in the workplace.”
Positive impact
BME’s safety protocols, says Dhoorgapersadh, have been directed by a range of safety interventions, including the implementation of driver awareness programmes and fatigue management, process safety, near-miss reporting and “visual felt leadership”, which requires a consistent commitment from senior BME executives to convey exactly how safety protocols are being applied on site. This all works in lockstep with Omnia Group’s overall vision of “zero harm and positive impact through responsible business practices”. These frameworks also marry up with the stringent standards of BME’s mining customers, many of which are established international companies.
For Dhoorgapersadh, achieving the zero RCR is in no way a case of “mission accomplished”. Safety standards must be rigorously, but also continuously, adhered to – to keep finding ways to improve and thereby reducing any risk of safety incidents in the future. And that applies to constantly monitoring the wellbeing of its employees too.
“In recent years, for instance, BME has placed growing focus on the medical wellness of our employees,” he says. “They often work under very stressful conditions – frequently out in the open or on the road. Our medical surveillance programme has become more intense, to ensure that their physical condition is optimal at all times.” That programme also covers subcontractors – particularly those in the transport sector.
Similarly, BME’s Safety for Life focus is extended beyond the workforce to the natural environment in addition. The adherence to strict safety protocols has also ensured there have been zero occurrences of chemical spillages that could harm the environment. “We are very aware that, to sustain our enviable safety record, we need to be revisiting all aspects of our progress to look for ways to refresh our approach,” he says.
Small details meet high-level innovation
According to Dhoorgapersadh, both a high-level focus on safety and a constant attention to the small details is the key to maintaining this kind of continued record.
“An important aspect of safety management is about doing the simple things better. In every task, you need to be identifying where the risks are – and find ways of preventing those risks from becoming reality,” he says.
Innovation also plays a crucial part. “The blasting philosophy of BME is expressed through our innovative products and leading initiation technologies,” says Dhoorgapersadh. Electronic detonation systems play an important role in achieving safe blasting, for example, because they allow detonators to be accurately initiated within milliseconds of each other, staggering the energy release of a blast as opposed to numerous blast holes detonating all together – a much safer approach.
While innovation and successfully applying a range of safety protocols to adhere to – and indeed exceed – regulations, Dhoorgapersadh believes that fostering a culture of safety that aligns behaviour with systems is still the most critical aspect at play.
“Our Safety for Life brand priorities the safety of employees, communities and the environment,” he says. “By ingraining a safety culture, we can apply and embed our safety learnings wherever we operate.”
Further details:
For more information, please visit www.bmeexplosives.com and download one of BME’s award winning whitepapers below.