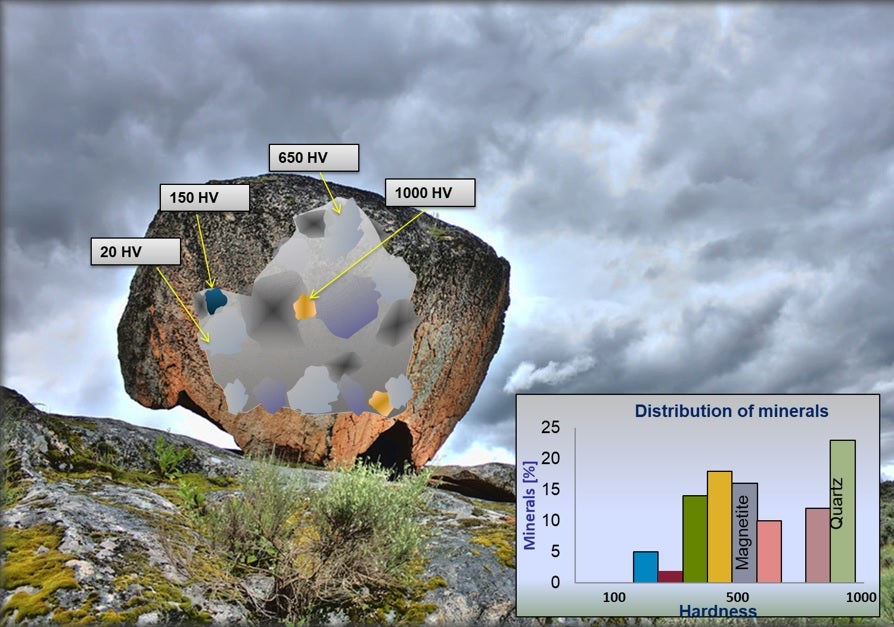
As an industry – including miners, OEMs and attachment producers, we need to move things forward. Mining companies are typically risk-averse and do not like to be first movers. Steel and casting companies more often than not measure their performance on tonnes sold. Boilermakers like to weld. And OEMs often appear to focus on machine and technology development, over ‘the bit that moves the dirt’ (an essential function of their machines!). This presents a question: can we do better?
If we really focus on what the goal / purpose of the equipment is, can we offer better solutions as an industry? In other mobile equipment attachments – most notably dump bodies – we have seen significant advances in weight reduction and increases in payload, but why has this not been effectively translated in bucket design?
On many mine sites, we are still building and repairing using chocky blocks, heel blocks, a mixture of wear bars and wear liners on top of other wear blocks and wear liners. Wear parts to stop the wear parts wearing out. There are thousands of instances of this – use of bi-metals, chocky blocks, wear buttons, manual hard facing, etc. All costly, all time consuming to install, all adding weight to a product that is to be suspended off the front of an excavator, and for which every kilo of mass we add to the bucket, we should be removing a kilo of usable payload! And that is before we get into what we are doing to the base structural materials of the bucket with all that heat input.
Can we think a different way?
In the 1970s, gas-guzzling, full-size cars from the big American automakers ruled the world – with examples such as the Ford LTD clocking in at just 8.5 miles per gallon! But in recent years Tesla has outstripped the value of all these companies using new technology, with the development of lightweight, electric vehicles that are desirable enough to be sold at a premium.
In the lifting industry, technological advances in materials and design over the last 90 years have seen us go from steam cranes with 12t payloads and a 3.5m hoist to telescopic mobile cranes with 100x this payload – 1,200t at a reach of up to 188m!
Closer to home in mining, as mentioned, significant advances have been made by many in dump body design, with higher strength, higher hardness materials enabling structural and wear components to be combined, and enabling new shapes to be used, reducing welds and high-stress areas. Here lightweight aftermarket options can yield up to a 10% improvement in the available payload.
But the potential gains can be even bigger in buckets than bodies. And as there are fewer excavators in the system than dump trucks, when we can get the productivity of an excavator up it can make a bigger difference to the overall operational efficiency of the mine then upgrading a single body. The full lifecycle should also be considered – the cost of maintenance, refurbishment and repair versus productivity/tonnes moved.
What are we trying to achieve?
In mining, there are four major considerations:
• Safety
• Efficiency
• Environment
• Cost
However, ultimately in a truck and shovel operation, the goal is to move the most tonnes in the safest, fastest means, and for the lowest cost per tonne.
Bucket design constraints
As a non-OEM producer, we need to design and operate within the Machine Design Constraints. That being the suspended load limits (the maximum allowable weight the machine can lift – a combination of the bucket and payload weight), the Tip to Pin radius (which is specified to both ensure sufficient breakout force, but also prevent contact between the bucket and the stick), the Bucket to Machine Connections (pin arrangement), and a maximum bucket width.
The design may also be constrained by the Ground Engaging Tool (GET) design and selection – particularly with the use of Cast Lips which pre-fix the width of the bucket to the width of the casting. Plate lips offer some additional flexibility with lip width and the spacing of GET – but also come with additional manufacturing costs.
We also need to think about the rock. When designing for a specific application we need to understand the hardness profile of the rock, which comes from the mineral composition. We need to understand the shape of the rock and the sharpness of particles. The density of the rock is critical to right-size the bucket, and the material fragmentation size is also important in this aspect to understand fill factors.
What is available to us now?
As indicated, times are changing, and we need to change with it. We have a suite of new tools and materials at our fingertips and we need to utilize these / take steps away from the old way of building a structure from structural materials in the same shape as we have always made it, and then covering it with wear-resistant materials.
Materials
• New stronger, harder, tougher advanced steels, offering the capability to combine wear and structural elements.
• New composites.
• Castings in new shapes and in new materials.
Joining Technologies
• Welding
• Bolting
• Adhesives
Design and Analysis Tools
• Advanced CAD/CAM
• Finite Element and Discrete Element Modelling
There are several who have innovative designs and thinking, but there is not widespread take-up of these from the industry, and there are still many who are happy to sell tonnes of steel rather than to sell the opportunity for increased tonnes moved.
To be followed by Part 2, detailing what G&G has done to meet these needs with our XMOR high productivity bucket offering.