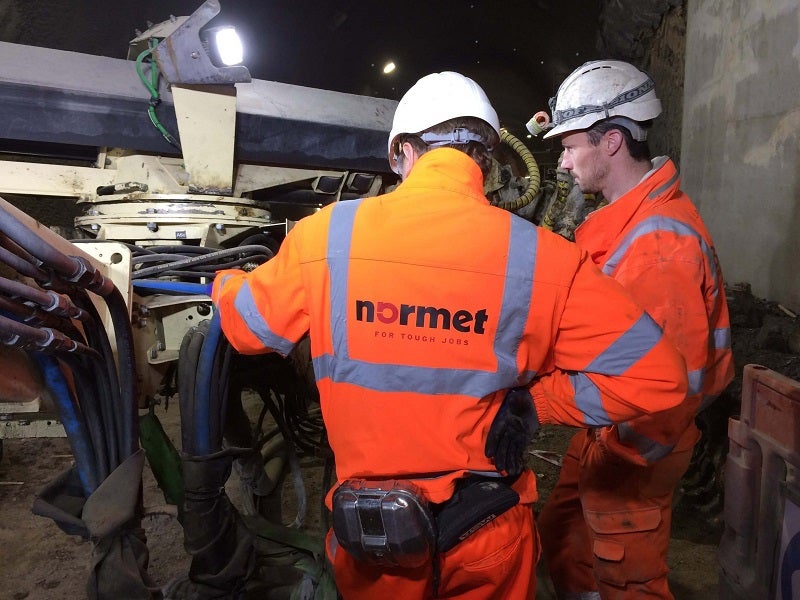
Robotics, remote technology and digitalisation are all something that we are growing accustomed to seeing in industry 4.0, and increased utilisation of AI, machine learning and automation is something that we should expect to see more of in the future.
Fortunately, technology stealing our jobs remains in the remit of science fiction, and changing the way we work is only making the industry more sustainable, safe and efficient.
But there is one challenge that the industry is facing in light of these new ways of working: re-skilling. Mining Technology spoke with Mark Ryan, Normet’s vice president of equipment offering and R&D, about how technology trends are shaping the way we work, and how the skill gap is being addressed.
“People often think that if we have this increased level of technology, that potentially their job becomes redundant. What we’ve seen in reality is that those jobs still exist, it’s just that the skills are different,” Ryan explains.
“Nowadays there’s typically a huge amount of effort going into zero-emission machines, such as battery-electric. If we think about it from a skills perspective, batteries and electrical components don’t really need a heavy amount of service, but they still do need to be maintained. We need a workforce with the ability to work on electrical components, particularly high-voltage electrical components.”
Replacing diesel engines doesn’t mean replacing the personnel who work with them as companies increasingly offer up-skilling courses for current workers and new training for emerging generations entering the industry. These new maintenance skills extend to the automated machinery that is making repetitive tasks more efficient and taking workers out of the danger zone, something that becomes increasingly important as mining excavation goes deeper.
“We understand already what drives customers to move towards zero-emission machines, but another trend that is very evident nowadays is that customers want to take every step possible to move personnel away from dangerous operations,” Ryan adds.
“What that does is it adds an extra level of automation, which is able to take the operator or worker away from a dangerous area, and an automated system will be put in place where the operator is able to do that function remotely or the machine does it automatically. Obviously, that also comes with different levels of skills to be able to maintain that type of technology. Automated types of machines actually require a much higher level of maintenance, so you really need to up your game with regards to looking after these systems.”
Beyond safety, automation’s selling point is increased efficiency, something that we cannot rely on without skilled maintenance workers.
According to Ryan: “You can have the most advanced automation system out there, but if you’re not able to make sure that it’s being maintained in the appropriate way, you tend to lose any advantage that this system would give you. If you have more breakdowns, then of course you have less productivity.
“Knowledge of control systems, how to handle that control system, software and electrical components such as sensors, would definitely become more of an advantage in the future.”
A challenge that the mining industry is currently facing is not only up-skilling workers who have experience in the industry, but also finding new skilled workers to take the leap into mining and tunnelling.
“That is always a challenge with mining companies,” Ryan explains. “It’s not just about implementing the technology, but it’s also about finding those people who are experts in using and advancing it.
“When people do get into the mining business they realise how much fun it is, at least in my case. I think I got the bug very early on and realised that there was nothing else quite like it.”
To find out more, download the whitepaper below.