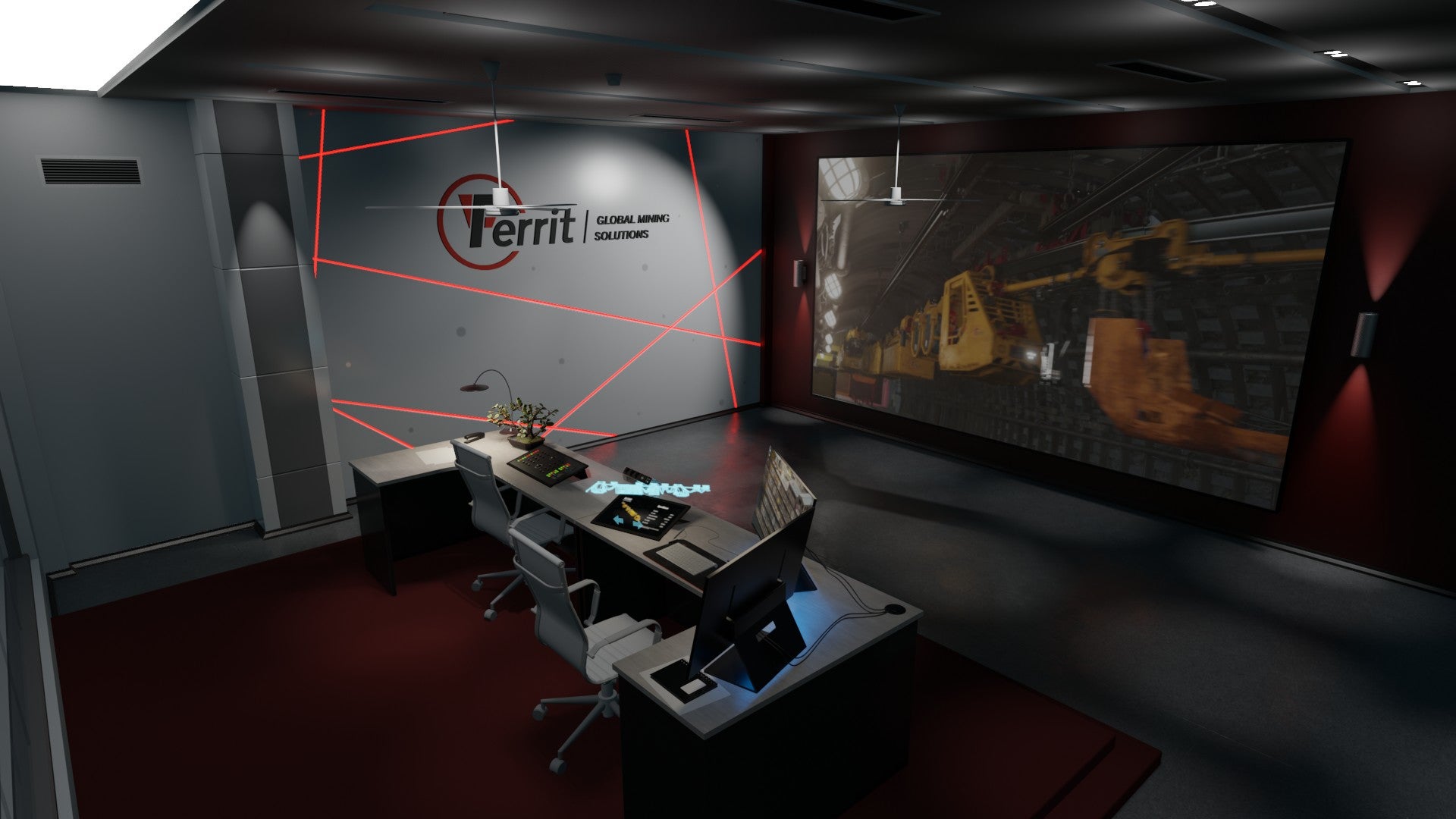
The world’s mining industry is facing rising pressure from regulators, investors, and customers to lower carbon emissions from operations, and most of the big players have already set ambitious targets to achieve CO2 emissions reductions in the shortest time possible.
Capital markets, often a key source of funding for miners, often charge as much as 20% to 25% higher rates for those miners with the lowest Environmental, Social, and Governance (ESG) scores. This gives those with better sustainability and greenhouse gas (GHG) emissions records.
One key pathway is electrification, which is fast becoming a major technology shift in mining, together with the expanded use of digitalisation and automation. Keen cost improvements and a greener profile is driving more companies to consider electrification – indeed most new mines plan to include battery-powered equipment in their operations.
Battery and electric power
Battery electric vehicles (BEVs) are the main options for long-life operational transport infrastructure, and together with digital innovations in monitoring, maintenance, worker safety, digital twinning, etc, all help mines to demonstrate their zero carbon credentials.
Electrification will have the largest impact on underground mining, as without noxious diesel exhaust fumes and the heat such powered equipment generates, mines would not require hugely expensive-to-run ventilation and cooling infrastructure. An important side benefit is increased protection for workers from excessive heat and bad air.
The current crop of lithium-ion batteries utilises an electrolyte that is made mainly from ethylene carbonate. Although the electrolyte is designed to lend stability to both the anode and cathode, it is flammable and raises concerns of battery fires and subsequent toxic gassing.
Companies, however, are researching to make safer solid-state batteries, that use a non-combustible glass electrolyte, which will have a longer cycle life (battery life) with a high volumetric energy density and fast rates of charge and discharge – ideal for enclosed underground work environments.
Higher performance batteries
Such developments of high-performance batteries will help ease the route toward increased automation and electrification of mines, making extraction easier and cheaper while maintaining ore grades, and supporting the electrical equipment market’s growth and, consequently, the battery-powered mining equipment market.
Mining machines are now being designed that can use onboard and remote data analytics and statistical techniques to predict equipment health and create just-in-time maintenance schedules.
They can also have devices installed that can measure the volume of ore available in the ground using drilled core samples and analysing composition against stored data, reducing time spent in face inspection and core logging.
Analysis of mine operations
There is virtually no aspect of underground and opencast mining operations that is not being analysed to gauge whether fossil fuels can be replaced by electricity to power all activities. It is now generally accepted that battery and electric power reduce greenhouse gases, but there are also other great benefits.
Ventilation costs plummet as around 40% – 50% less ventilation is required with battery or electric-powered machines, compared to those running on diesel. There are also lower overall cooling requirements, less noise pollution, and lower maintenance costs, with battery vehicles having significantly fewer parts compared with diesel systems.
Some additional technologies being researched to make mining more efficient are:
- Collision avoidance systems on all vehicles – a cheaper investment option than paying future damages
- Autonomous and remote-control vehicles – increase safety as the software makes fewer mistakes than humans
- Drones – can access all parts of mines easily. Good for mine site plans, surveys, heat mapping, visually checking machinery and equipment
- Battery- and hydrogen fuel cell-powered mining vehicles – reduce carbon footprint and help achieve net zero targets
- Fatigue detection – using wearables like intelligent clothing and smart headgear, the physical condition of individual workers can be remotely monitored
- AI-powered mine planning software – makes new mines more efficient
- Digital-twinning – monitor mine operations remotely to anticipate and react quickly to issues
- Digital communication systems – to increase connectivity safety and reduce accidents etc.
- Predictive maintenance using intelligent sensors for all plant and equipment
There are some 10,000 operating mines around the world, and all of them are considering modernisation programmes of one sort or another in light of rising fossil fuel costs and climate change targets. The opportunities these changes create a huge market for companies with products and technologies that can create efficiencies to achieve better results.
Ferrit’s R&D is working on a new battery concept, which will be applicable not only to its own-brand equipment and machinery but could be marketed as a product on its own merit to other mine equipment manufacturers and also those companies that already have battery-powered machinery and equipment in its inventory.
Electric and battery power designs for transportation are expanding, with hundreds of thousands of cars, trucks, buses, off-road vehicles, and even some ships and intercity and commuter railways are running on green power. Ferrit plans to stay at the leading edge of this phenomenon by investing in sustainable R&D for all its future products and services.