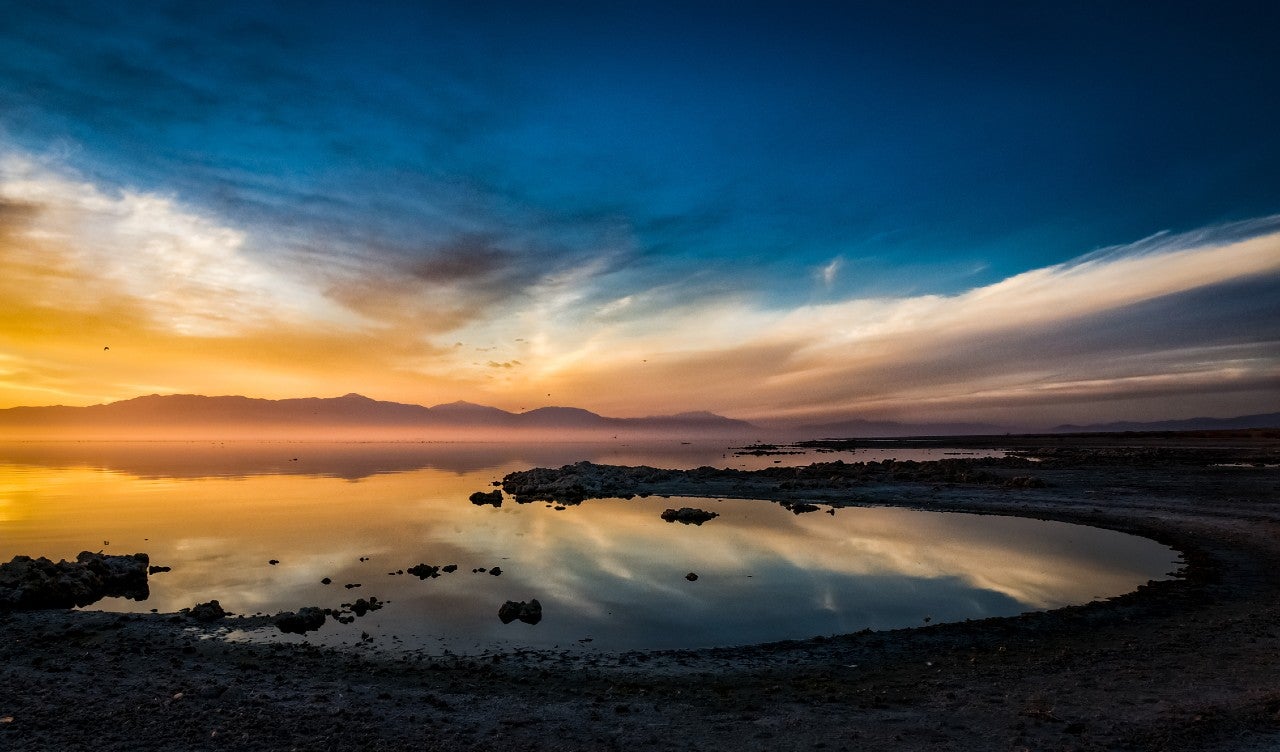
According to Global Data’s Mining Intelligence Centre, lithium consumption is forecast to rise to 138.8kt by 2025, up from 75.9kt in 2022.
This may not sound like a lot. But it took 16 years for production to rise by the same amount from 15kt in 2000 to a peak of 96kt in 2018. With a looming supply gap, lithium producers need to find new developments and technologies to help deliver metal to market in the time available.
Global lithium consumption vs electric vehicle battery demand, 2014-2025
Source: GlobalData Mining Intelligence Center
Self-sufficiency and regulation are driving local activity
The world’s main source of lithium currently comes from a traditional evaporation pond method, like those in South America, or from hard rock mines in Australia.
But what options are available to lithium producers and governments to increase supply as they look to secure one of the most important natural resources in the next decade?
Already, some are looking at their local resources and supply chains to produce lithium themselves, rather than rely on foreign manufacturing sources.
For example, in February 2021, the President of the United States, Joe Biden, signed an executive order to put battery materials at the heart of US climate technology. This could bring significant change to areas like California’s Salton Sea – a region rich in lithium brines, with SRI International suggesting the region could produce 600,000 tons of lithium annually.
“The challenge for America’s lithium deposits is that they’re low-grade, which is the biggest barrier to achieving self-sufficiency,” says Craig Cuttriss, lithium process consultant at Worley. “In California’s Salton Sea lithium is found in brines, including geothermal brines, and producers will need to explore lesser-known techniques and technologies, such as direct lithium extraction (DLE), to help recover lithium from these deposits.”
Direct lithium extraction explained
DLE uses a similar method to ion exchange.
One of the advantages of DLE is increased efficiency of lithium recovery from low-grade brines. “With DLE you’re not adding lime to remove magnesium and concentrating it in evaporation ponds, you’re extracting the lithium directly from the raw brine,” explains Cuttriss. “This means it can be economic to treat lower grade brine sources down to approximately 200 parts per million, allowing low grade resources to be tapped, and expanding the number of resources available to miners.”
What’s more, cut-off grades can also be lowered which increases the size of the resource.
“Current data suggests that DLE could recover up to 90% of the lithium in the brine stream, whereas the overall recovery through evaporation is around 60% to 70%. If these assumptions are correct, there may be significant capital cost gains which is a great step forward to increasing the supply and diversity of lithium sources,” adds Cuttriss.
Cracking the direct lithium extraction challenge
DLE is currently being used on a few projects around the world. A project in northern Argentina uses an alumina-based adsorbent at a commercial scale to produce lithium carbonate – and has done so for 20 years.
“It’s likely the only project in the world that currently uses DLE at such scale,” says Cuttriss. “More recent developments include the salt lakes of Tibet with a company claiming DLE technology and marketing its success to the world.”
So why hasn’t the rest of the industry followed the same path?
“The fundamental challenges fall under intellectual property and technology scale-up,” explains Cuttriss. “Current research is sponsored by small venture companies, mostly in Canada and the USA, that are protective of their intellectual property and commercial arrangements when engaging with prospective lithium producers.”
As a result, DLE technology must be ‘reinvented’ time and time again, creating uncertainty about the performance of DLE technology.
“Some research and technology companies claim to have their own absorbent materials, but broadly speaking, this is yet to move past the pilot stage,” says Cuttriss. “Scaling up DLE techniques from lab to full production remains a challenge. And developing a stable material that bonds with lithium, and no other impurities or minerals found in brines, is a key research objective.”
Confidence is also needed around the length of the media’s lifecycle, reliability of mass production and cost.
“Through early collaboration, and by applying engineering processes tailored to bring new technologies to commercial scale, project developers can lower these risks to an acceptable level,” says Cuttriss. “Worley is investigating how DLE can work at commercial scale, focusing on the process flow sheet and circuit mass balance, as well as the performance of the media in terms of its selectivity for lithium, adsorption kinetics and lifecycle.”
Sustainability is also a critical concern when implementing DLE technology. But separate technology and techniques to reduce site emissions and minimise water waste are more accessible today.
Site sustainability
Large consumers of lithium, such as battery producers, are now, more than ever, conscious of their sustainability credentials and want to make sure their products are as green as possible. This means all materials, starting from the mine site, must come with a low-carbon footprint.
“To address site sustainability lithium producers need to focus on how they generate heat and power and implement strategies to minimise water consumption,” says Cuttriss.
Evaporation ponds are low carbon emitters. But it’s the peripheral equipment such as pumps for the large volume of brine that needs to be moved, which require alternatives to fossil fuels.
“Decarbonised lithium production requires heat to be generated by solar, possibly low temperature solar thermal, rather than gas or coal-fired power plants,” explains Cuttriss. “Water is also scarce in a lot of the locations where lithium is extracted. And in some cases, fiercely contested by the community where brines are concerned. Identifying opportunities for water recycling, as well as recovery through efficient tailings dewatering technologies in the case of hardrock lithium resources, needs greater focus and expertise if lithium producers are to meet environment and social expectations.
“There are also opportunities to use reverse osmosis on process water, keeping fresh water in streams or underground aquifers, to play a stronger water stewardship role.”
While we have limited information on DLE’s water saving credentials, a recent announcement from Schlumberger New Energy suggests greater sustainability can be achieved with its planned DLE pilot plant in Nevada, USA, potentially reducing water consumption by over 85% compared to current extraction methods.
On the verge of transformation
For those chasing lithium self-sufficiency, DLE is a viable technology for producers and governments to achieve lithium self-sufficiency.
However, research centres and lithium producers will need the right partner to help them ‘bridge the gap’ by assessing technology readiness, then guiding these solutions through front-end loading processes.
“Those who work out how to make DLE technology work for them and find sustainable options may leapfrog ahead and become a large player in a growing industry,” says Cuttriss.
“Managing the risks of new technology isn’t about good luck. Focused front-end-loading on the engineering of technology lowers the risk of implementation. Adding more definition and planning at the engineering stage helps miners to make better decisions as a technology is scaled up from concept to a solution that can be industrially applied.
But regardless of the extraction technique or location, favourable market conditions will arise for lithium producers who can demonstrate low carbon, sustainable operations.”