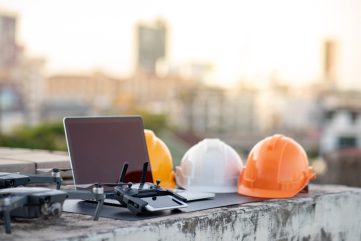
The Internet of Things (IoT) is revolutionising the mining industry by impacting every stage of the mining value chain, from prospecting to reclamation – with many advantages for pumping operations.
Connected sensors and actuators can monitor and help control the environment, assets, machinery, and people within mining operations. The technology enables mining companies to automate workflows, improve efficiency, and reduce costs, while also enhancing safety and ESG credentials.
The spread of IoT into mining has been encouraged by reduced latency, increased computing power, and the falling price of sensors, which have led to a faster ROI. Additionally, a growing number of IoT products and services now incorporate AI technology into their capabilities, especially for predictive maintenance.
For pump installations specifically, IoT has much to offer. With the correct applications, IoT can remotely monitor wear and tear on equipment, nose clearance, vibrations, temperature and load conditions, movement of materials and water in tailings. IoT tech can also manage water curves – all vital for reducing inefficiencies and saving costs.
Potential problems with slurry pumps
Low pump efficiency and flow rates are potentially major problems for slurry pumps. Water curves indicate a slurry pump’s performance at various speeds, with curves changing depending on what slurry is going through the pump. As such, water curves are an effective way to calculate performance.
However, being unable to read and adjust a pump’s water curves for the presence of solids can adversely affect production – by increasing the likelihood of subsequent line blockages, and even possibly resulting in shutdowns.
By providing operational visibility, IoT sensors and cameras installed in mining pump installations can monitor and gather data about the movement of materials and water in tailings. With IoT sensors in place, remote monitoring of water curves can take place, allowing rapid and accurate adjustments.
“GIW’s IoT offerings allow customers to monitor and accurately control their nose gaps, which can lead to upwards of 6% gains in hydraulic efficiency, according to tests performed on an 84in impeller in the GIW Hydraulic Lab,” explains Aaron Cutright, manager of engineering IT systems at GIW Industries.
Digital processes to transform pump operations at mines
KSB Group is a leader in digital transformation and is using technological solutions to enhance customer ownership through monitoring, analytics, and IoT – all to ensure optimal pump performance.
KSB offers four mining IoT intelligent applications that allow for effective monitoring of both slurry and non-slurry pumps, making a significant contribution to operations efficiency.
These solutions can be installed as single units, or as a combination depending on the application.
KSB Guard is a non-slurry pump monitoring system that allows remote monitoring of pump performance data, optimising maintenance and reducing downtime, increasing efficiency. Consisting of four components, the smart pump monitoring system contains a sensor unit, a transmission and battery unit, a gateway, and a web portal and app.
Current dynamic data can be viewed at any time as a complete overview and in detail. For example, vibrations and temperature, load conditions or even warnings and alarms.
GIW® SLYSEL is KSB’s proprietary software program for slurry pump performance calculations and pump selection, helping mining operators identify the best slurry pump for their needs by analysing key data points. As well as calculating the minimum pipeline velocity to avoid sanding, it also predicts a range of recommended flow rates and supports the pump selection process for the specified pipeline system. It can also simulate large pipelines with dozens of pumps and can be used to plan startup sequencing.
GIW® SLYsight is a pump wear analytics tool, which measures the actual wear rate of pump parts, including the nose gap, by collecting real-time data from custom sensors. The motivation behind SLYsight is to continuously monitor the thickness in different locations and to visualise that wear over time. This can extend maintenance cycles and because operators can see how long their parts are lasting, it also means fewer unnecessary downtime events, which can lead to significant improvements in operational efficiency.
GIW® RAMSL improves maintenance procedures by remotely adjusting the nose gap of a pump, enhancing operational safety and efficiency, and increasing adjustment accuracy.
In slurry pump operations, units are expected to run continuously 24/7, and there is critical maintenance activity involved with maintaining a tight, continually adjusted nose clearance between the impeller and the suction liner. Historically completed during manual maintenance, with most or all of the equipment shut down, this can lead to a loss of productivity.
Remotely adjusted mechanical suction liner (RAMSL) offers the ability to do nose clearance adjustments down to around a quarter of a millimetre. In addition, the technology can be adapted to existing equipment with minimal impact.
Remote monitoring with IoT
Through the targeted use of IoT, water and slurry pumps can be monitored more accurately, making the pumps more efficient, and reducing costs and potential downtime.
Although KSB and GIW have had software controls for their pumps for some time, the new consolidated offering of products can help miners monitor their equipment remotely. Additionally, these solutions are available with real-time technical support, 365 days a year and 24/7 from anywhere in the world.
According to Cutright: “Customers that have installed SLYsight on their equipment in the field have been impressed by the insights it has provided into wear development, which is novel data that has allowed them to extend maintenance cycles further than ever before.”
For more information on how digital processes can revolutionise the operation of pumps, download the free paper below.