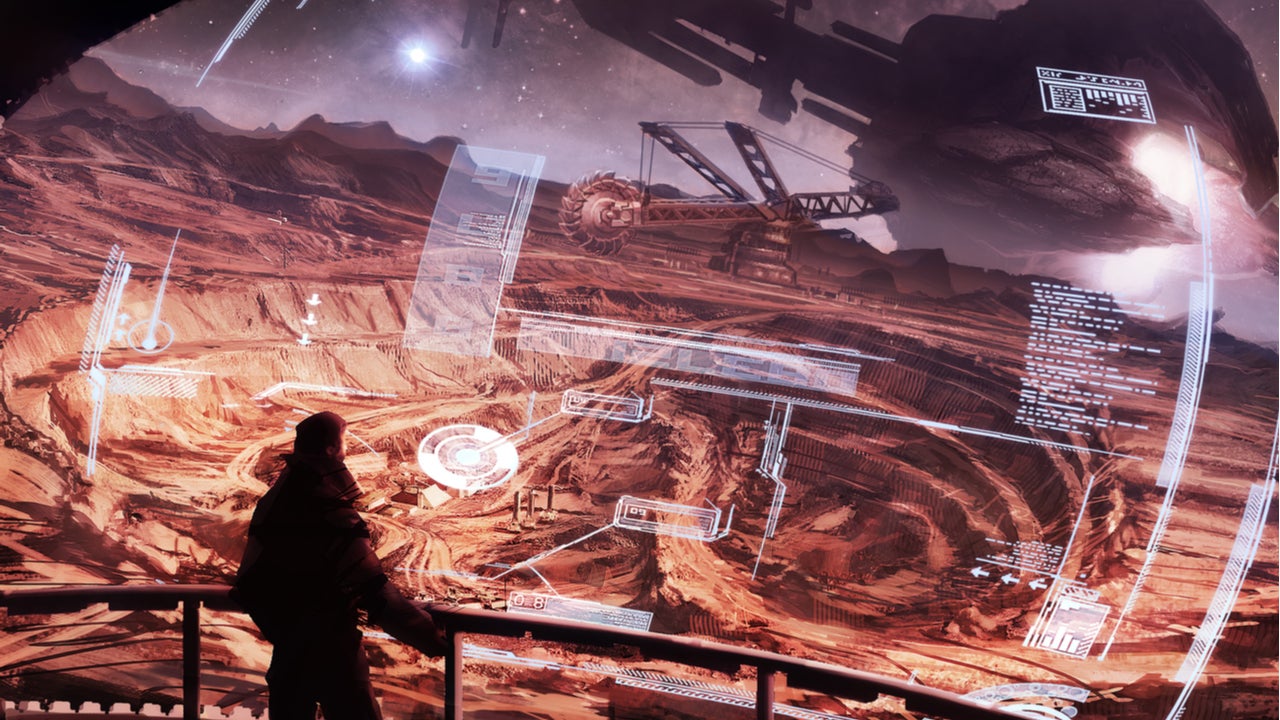
When declaring robots are the future of any industry, you will often be met with strong reservations and fears of redundancy, with suggestions of a fully automated future striking fear into any employee. But automation does not necessarily mean a decline in employment, rather a change in expertise for operators who can benefit from learning new skills and improved safety measures.
This is especially true in mining. Improving safety, sustainability, and productivity are key factors robotic developers are striving for in the industry, and automation proves particularly useful when it comes to cumbersome, operations-heavy processes.
Mining Technology spoke to Mark Ryan, vice president of equipment offering and R&D for Normet, to eradicate common automation misconceptions and discuss how robotics are helping to create a more sustainable future for the mining industry.
Myth busting
“With regards to technology implementation, people often think that if we have an increased level of technology, then potentially their job becomes redundant or not needed anymore. But what we have seen in reality is that those jobs still exist, it’s just the skills are different,” Ryan explains.
For Normet electric vehicles and machinery is an area that is growing globally. Mining industry leaders are putting a huge amount of effort into zero-emission machines, such as battery-electric. When a diesel engine is removed and replaced with a battery driven system, the service becomes a much longer process. Despite batteries and electrical components not requiring a heavy amount of service, they still need to be maintained, therefore requiring people that are able to work on electrical components.
In short, removing diesel engines and replacing them with automated battery systems does not mean replacing personnel in favour of mechanised tools, rather adapting the skill requirements and role responsibilities of their existing operators.
Improved safety
Automated machines can often improve safety and productivity of underground activities. Normet is committed to helping its customers in building safe mining environments through robotic machine components.
Replacing workers with a remotely functioning automated system reduces the risk of workplace safety implications. “Customers want to take every step possible to move personnel away from dangerous operations in mining environments,” Ryan says. Through distancing workers from impact zones, customers are not only improving the safety of their workforce but also increasing productivity and profitability, thus maintaining the best possible customer outcome.
Latest innovations
The first step towards optimising operations for Normet is automating the concrete spraying process. SmartSpray technology ensures speed, quality, and economical use of materials. Today, the use of sprayed concrete in civil engineering structures such as mines, is a crucial part of successful, highly productive, and safe rock support systems.
Through automated technology such as SmartScan, concrete application and repairs are completed effectively through AI calculating and monitoring the thickness of sprayed concrete. This equipment ensures spraying is completed efficiently and with minimal waste.
Robotic mechanisms and their operators work in tandem to achieve the best mining results. “Automated machines require a much higher level of maintenance as they tend to tolerate less heavy abuse. You need them to work efficiently so the customer can receive all the benefits they need from their investment,” Ryan says.
But talented operators are becoming increasingly difficult to find, and the quality of the sprayed concrete can vary critically between operators. Equipment manufacturers are developing products that ensure the operator effect on the result is minimised while spraying productivity is increased. Ryan explains: “You really need to up your game with regards to maintaining these systems.”
However, this growing need for highly skilled operators does not hinder current personnel, rather it provides new opportunities for workers to up-skill and develop their career. According to Ryan: “Technology might replace certain people but the skills required to maintain the equipment will change.”
The mining industry is undergoing seismic changes with technology trends shaping the way they operate. By addressing the skills gap created through integrating robotics into everyday working environments, Normet is improving the safety and efficiency of its’ mining projects whilst keeping employees central to its continued industry leading success.
To find out more, download the whitepaper below.