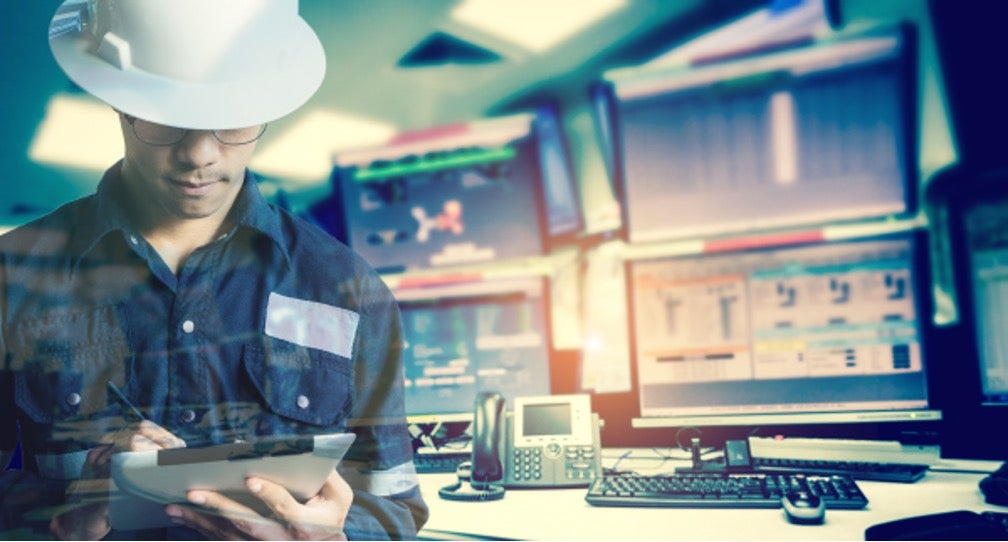
Now, more than ever, companies are looking for ways to empower their employees to work from a distance. To do more with less. Companies are having to streamline, tighten the budgets and find ways to keep expenses down, as well as minimise the exposure of their valuable staff to risky environments. And of course, not forgetting to find ways to make sure machines are operating at peak performance, have high reliability and minimise down time.
Remote Monitoring and the Industrial IoT (IIoT) are not new technologies. You have probably heard of them before. Remote Monitoring from Monico Monitoring, Inc. allows the user to leverage these technologies to create new ways of doing business. To find ways to be more efficient, minimise disruptions to business, and keep everything running as smoothly as possible.
With innovations in technology, it is possible to connect your industrial machines – including mobile and stationery – and equipment (i.e., assets) to the internet or private networks, to systems, for storing, visualsing, analysing data and monitoring for conditions that may be problematic. The same data that can be captured from these connected devices can be used to review and monitor productivity of machines and operations, and assist in finding ways to improve the utilisation, reliability, maintenance, and service of these assets.
Remote Monitoring can provide increased awareness, improved access to information, visualisation of asset data, powerful notifications and diagnostics capability. Coupled with the knowledge of subject matter experts (SMEs) and analytics, remote monitoring can provide a powerful tool for use in condition monitoring of assets.
Remote Monitoring can help maintenance/service in many ways, such as reducing site visits to equipment; reduced travel; better preparation when trips to equipment are necessary; improved visibility of how assets are operating; reduced downtime and improved productivity.
Implementing a Remote Monitoring solution can be challenging and there are many factors that should be considered when doing so.
So where does one start?
Monico believes one place to begin is by asking what data you need and how you can get that data to begin working to solve the business challenges you have. Monico refer to this as ‘Industrial Data Acquisition’. However, Industrial Data Acquisition’ is complex, there are many factors involved in capturing data to consider, such as industrial protocols (e.g., J1939, CDL, ModBus), industrial networks (e.g., CanBus), protocol translation and conversion, data sampling rates, data transmission methods, data storage, and more.
Once you have a solution in place to acquire data a whole other set of questions needs to be addressed. What are you going to do with it? How are you going to use it, who’s going to use it, and where are they going to use it? You’ll want to consider how data is to be consumed and visualised so that it provides immediate value to end-users. You’ll want to answer questions, such as: are the end-users going to review data on screens and do analysis of the data or is there a need for automated analytics to incorporate the knowledge of SMEs?
Remote Monitoring becomes powerful when you implement automated analytics that analyse data in real-time, as it streams in from the connected assets, and triggers alerts and email or text notifications based on conditions presenting with assets that may require human attention and interaction. This helps minimise the need for someone to be reviewing screens of data all day, which nobody wants to do.
How can Monico Monitoring help?
Monico works with its customers to help them develop their solutions for both Remote Monitoring and Remote Condition Monitoring. Monico likes to differentiate the two like this: Remote Monitoring is collecting and viewing data coming from assets whereas Remote Condition Monitoring incorporates advanced real-time analytics to help detect conditions that are developing that may result in shut down events or catastrophic failures of assets.
This provides a preemptive approach to equipment and machine maintenance and can help to avoid costly downtime. Monico sees Remote Condition Monitoring as a tool for maintenance and service professionals to use in improving reliability and service/maintenance of assets through condition-based maintenance.
Further details:
For a more in-depth look at these concepts please download Monico’s technical whitepaper on Empowering companies to do more with Remote Monitoring.
To have a conversation or schedule a consultation please contact Monico at: sales@monicoinc.com or visit monicoinc.com