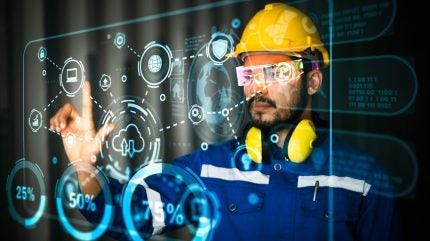
The mining and tunnelling industry is undergoing significant changes. What is emerging is a new era of battery-electric vehicles (BEVs) and tech-integrated machinery in mine sites and large-scale civil engineering projects.
From exploration to development and extraction to reclamation, advancing technologies are rapidly reshaping how mines can profitably and sustainably recover metals and minerals from ores and process them efficiently. Disruptive technologies are also being rapidly adopted in equipment used in mining and tunnelling projects for more cost-effective decision-making.
A growing number of electric, tele-remote and autonomous machines and vehicles are arriving on site but as the technology speeds up, is worker education keeping pace?
Knowledge gaps are a growing risk
Most countries have mining regulations that require manufacturers to provide basic training for new machinery, including commissioning, familiarisation, basic safety and handover, but Normet says this isn’t sufficient to enable effective operational change management – and the gaps aren’t necessarily being filled by a third-party supplier or in-house.
“As the cycle of innovation gets shorter and the technology integrated into equipment gets more sophisticated, with electric and internet-of-things schematics, so companies involved in mining and tunnelling should be seeking extended and advanced training from their OEM partner,” says Harri Sonninen, global product manager for training solutions, Normet.
“IoT, robotics and machine learning are enabling mining operations to collect more data than ever before and use it to improve efficiencies in operations, boost profits, save energy and lower costs – but that all relies on the engineers understanding how to take advantage of all the functionality of the machinery.
“They should also have a deep understanding of the technology foundations that are the bedrock of new mining equipment so that maintenance can always be undertaken safely and effectively.”
Normet is a Finnish mining and tunnelling OEM at the bleeding edge of technology innovation and application development supporting mining operations get ahead of the curve with regard to worker safety, reducing waste and emissions and boosting performance. For 60 years, Normet has been defining the future underground, offering the latest in scaling, explosives charging, concrete spraying, logistics and other solutions to the industry.
Normet is a leader in mining technology, with a long track record of bringing groundbreaking applications to the market, such as its sprayed concrete support technologies, integrating robotics into explosives charging systems and its SmartDrive modular battery electric vehicle (BEV) architecture. The OEM has always offered its customers training but the pace of change has prompted it to officially launch a training academy in a bid to formalise its approach and broaden awareness of the importance of worker upskilling, which is critical today with the shift to BEV architecture and IoT-integrated infrastructure.
Sonninen explains: “Battery electric vehicles require less maintenance overall, but the tasks are more advanced, involving high-tech cooling units, battery technology, and inverter technologies. Incorrect maintenance can cause significant failures and downtime. For BEVs, understanding the different architecture is crucial to prevent failures and downtime.”
Normet’s offers a basic BEV training programme for all service personnel and operators. This includes training in hazard evaluation, education in the basics of recognising component locations and operating principles, safety training that goes above the mandatory levels included in commissioning and basic maintenance and service work that does not involve high-voltage devices.
Its advanced BEV programmes are aimed at electricians and charger maintenance workers and are more technical due to the nature of their work – responsible for AC/DC maintenance and critical component replacement.
Maintenance training for its other equipment outside of BEV is also split into different levels – the basics concerning familiarisation that is included in the service level agreement, extended and advanced. Depending on the number of personnel and requirements, training can be online or classroom based.
The company also offers separate training for process applications like spraying concrete, and scaling, which Normet can provide through its leading simulator digital twin technology and hands-on training with subject matter experts
VR and the future of training in mining
“Virtual learning and augmented reality learning programmes are the future of training in the mining sector,” says Sonninen. “Simulations provide trainee operators with the opportunity to experience equipment in a realistic virtual setting without putting themselves at risk, damaging equipment or using expensive production equipment.
“Additionally, VR training has the benefit of offering continuous performance feedback and the ability to record the session for later evaluation and providing clearly reported data from training.”
Normet analysis shows that simulator training can improve operator efficiency by 23% on average and deliver up to 30% savings in process operations costs.
Normet has been building its training simulators since 2010 and recently introduced full-blown 3D digital-twin technology to train concrete sprayers and scaling operators. Its spraying simulator was developed in conjunction with EFNARC, the international association of Experts for Specialised Construction and Concrete Systems and now the Normet spraying simulator includes the globally recognised expert training course for beginner and advanced sprayers. This includes hands-on spraying practices.
Its success led to Normet bringing to market a VR simulator for scaling in 2023. This allows customers to understand how to manoeuvre when loose rocks are falling and learn systematic scaling control, potentially hazardous, in a completely safe environment. Normet, which has been investing in digital twin technology development for years, has suggested that more simulator launches could follow in 2025 and will be aligned to customer training demand.
“Process audits and basic equipment commissioning are no longer sufficient in the digital age, for many reasons but also for employee engagement. In a tight labour market, you want to be the mine that is offering the best development opportunities for your workers and then you create loyal talent to support your operation thrive for many years to come,” Sonninen reflects.
Read the free guide below to find out more about the Normet Training Academy