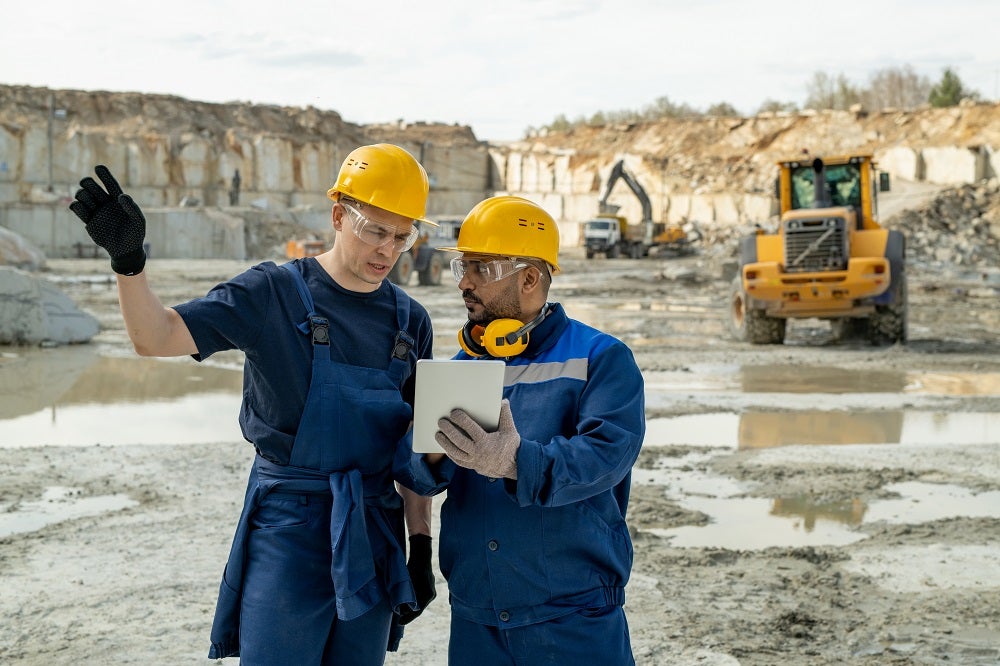
At the forefront of Industry 4.0 and digitalisation is a focus on optimisation, and this reaches beyond improving productivity and profitability. For industries such as mining and tunnelling, there have always been challenges when it comes to safety, from controlling air quality to preventing rock explosion or falls and implementing vehicle collision avoidance.
In the mining industry, deeper excavation is becoming increasingly more common, so what health and safety solutions does Industry 4.0 offer? Mining-technology spoke with Riku Helander, senior vice president and head of services business line at Normet Group, and Sushil Kohli, global head of health, safety, environment and quality (HSEQ) services, to find out more.
What are the health and safety benefits or challenges of using battery electric vehicles?
Riku Helander: The obvious health and safety benefit from battery electric vehicles comes from having no local exhaust emissions underground. In addition to improving the air quality, the ventilation in the mine environment is also simpler to design and needs less capacity when electric vehicles are used.
Battery electric vehicles emit heat significantly less than internal combustion engines machines. This means the machines have less heat around, lower surface temperatures, improving safety when operating with the machine.
As battery electric vehicles utilise regenerative braking when descending downhill, the energy can be utilised to charge the batteries rather than heat the brakes. Regenerative braking reduces the load on brakes and axels and the risk of overheating of brakes.
Sushil Kohli: Battery electric vehicles are quiet. They produce less noise in use, meaning the operator can hear the environment better when operating a battery electric vehicle. We estimate that noise level is reduced up to 7 dB during driving and we experience up to 15 dB reduction during idling. Also, in urban environments, the lack of engine voice and local emission is a significant benefit.
Our battery electrical vehicles come with an optional fast-charging capability based on the universal combined charging system (CCS) standard. Normet offers fast charging systems of different power levels for different needs. There is no need for tedious and dangerous fuel delivery and storing anymore.
The safety challenge to address with battery electric vehicles is fire safety. Normet uses battery chemistry, which is safe by design, and the whole design of the machine is based on the highest safety standards.
The environmental challenge is the safe disposal of used batteries in line with countries’ e-waste disposal policies. Most developed countries are creating smooth operations to deal with this challenge, and developing countries are also learning and implementing safe disposal processes that are pragmatic and operationally friendly.
How can underground mining and tunnelling use IoT technology for monitoring safety?
RH: Having a real-time view of the process helps to identify any deviations in the process, including safety. For example, scanning results of the thickness of sprayed concrete can be transferred to ensure the tunnel is structurally sound.
SK: Also equipment reliability and mean time between failure (MTBF). As the operating status and maintenance parameters can be monitored, maintenance needs and risks can be addressed using predictive maintenance skills to predict and prevent safety risks and loss of productivity, which gives better equipment availability for customer use. Cost-benefit is also realised for customers’ benefit as MTBF is improved by observing safety abuses while driving (such as harsh braking, vehicle in operations with the high temperature of oil, etc) using IoT and giving feedback to drivers to continually improve.
How have remotely operated vehicles/machinery affected safety culture? Can we expect to see more remotely operated vehicles in the future?
RH: We can expect remotely operated machines in the future for sure. Getting people away from danger is a key to improve safety. We intend to move in stages i.e., firstly operate from next to machine, then with the line of sight, and finally true remote operations. For many applications, such as charging and scaling, working remotely increases safety greatly.
In the future, we can also expect machines to be autonomous at least for a part of the process.
Another driver for remote operations is the ore, which is harder to get, and mines need to get deeper and deeper. The temperature deep underground can be too high for a full shift of work, hence remote operations is a question of safety and proper working environment.
Overall, are miners safer in Industry 4.0? Both from accidents and long-term health effects.
RH: The simple answer is yes for both. People can be taken away from the place of danger. Preventive maintenance reduces the risks of breakdowns and accidents. Optimising the process increases productivity and reduces both local and wider impacts to occupational health and the working environment. Of course, associated risks has to be mapped and managed to an acceptable level.
What services does Normet offer to improve safety at mining/tunnelling sites?
RH: We as employees of Normet are committed to serving customers safely. Zero harm is a mindset, and without a mindset of zero, we may never achieve excellence. To strive towards our ambition to move towards zero (recordable injuries and/or environmental incidents and/or occupational health illness), we are driving a culture of HSE positively that is leadership-driven but employee-owned. We learned that addressing behaviour, not exclusively deficiencies in equipment or conditions, can prevent most casualties. Leadership has empowered employees to identify and report (HSE) observations so that we can progress inclusively on this journey.
The Normet service plans, service agreements, and spare parts ensure high-quality operations of a machine and minimise the risk of accidents and breakdowns. We work with customers on all key processes to ensure the processes are optimised both from a safety and productivity angle. We actively share new safety upgrades and improvements with our customers, and we can also audit customer operations to ensure safety is appropriately addressed.