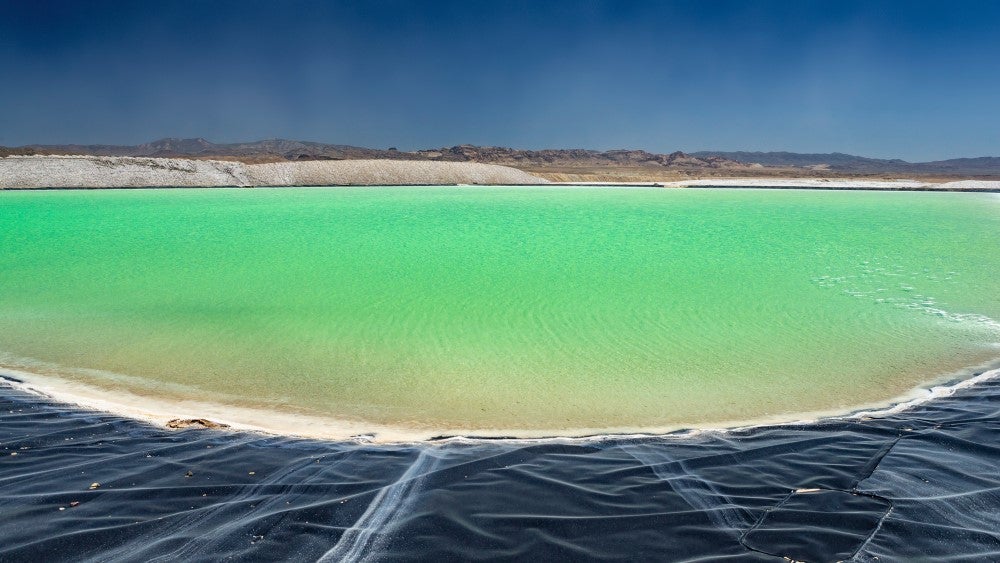
Industries across the globe are aiming to reduce, or eliminate, carbon emissions from their operations, and the implementation of sustainable practices in the mining industry is even more crucial as green mineral extraction increases.
Spodumene vs brine – lithium extraction processes
Two main raw material sources of lithium are brines and spodumene. A build-up of salty groundwater enriched with dissolved lithium is known as a lithium brine deposit. The “hard rock” minerals found in pegmatites, which form thick seams in other rocks, contain the lithium-containing mineral called spodumene.
Lithium brine is only found in a few places around the world. This brine is pumped to the surface to be evaporated in a sequence of ponds. Each transfer to a new pond results in a higher concentration of lithium, until the ultimate processing in a chemical plant, where the end product is lithium carbonate. The majority of the lithium generated from brines comes from Chile and Argentina, with a smaller amount coming from Nevada, USA.
What is spodumene and how is it mined?
Spodumene is a lithium aluminosilicate mineral originating in granitic pegmatites located across the world. It is mined using traditional techniques of digging and drilling the Earth for rock. Heavy machinery is needed when doing the rock blasting and ore extraction, which is then graded and crushed to ensure a constant feed concentration for the subsequent steps of the operation.
Lithium is extracted from the spodumene in a process that includes it being “roasted” at very high temperatures and then put through acid leaching using concentrated sulfuric acid, after which sodium carbonate is introduced to the mix, resulting in the formation of lithium carbonate. The resultant is then “slurried” with calcium hydroxide to produce lithium hydroxide, which is what battery manufacturers use for their cells. Petalite, lepidolite, and amblygonite are a few other minerals from which lithium can be derived.
Both processes produce lithium, but a higher quantity of the metal can be extracted from spodumene as it has a greater lithium content in comparison to brines, so can be processed into either lithium hydroxide or lithium carbonate much more quickly.
The drive to net zero
The global drive towards a net-zero carbon emissions future has explosively increased demand for green minerals such as lithium, manganese, cobalt, nickel, and graphite, to name the main ones. According to a March 2022 report by the International Energy Agency titled “The Role of Critical Minerals in Clean Energy Transitions”, over the next two decades, the proportion of clean energy technologies’ demands for these minerals will increase dramatically, reaching more than 40% for copper and rare earth elements, 60–70% for nickel and cobalt, and approximately 90% for lithium.
By 2040, EVs and battery storage are expected to overtake consumer electronics as the main users of nickel and have already surpassed consumer electronics as the main consumers of lithium.
Global lithium stocks
Extraction of lithium is carried out mainly in The Lithium Triangle: a region in South America that spans three countries: Chile, Argentina, and Bolivia. Home to roughly 58% of the world’s lithium resources, this land is a very dry zone where water is a precious resource. Several direct extraction methods are being used to recover the lithium from the brine, and then reuse the water.
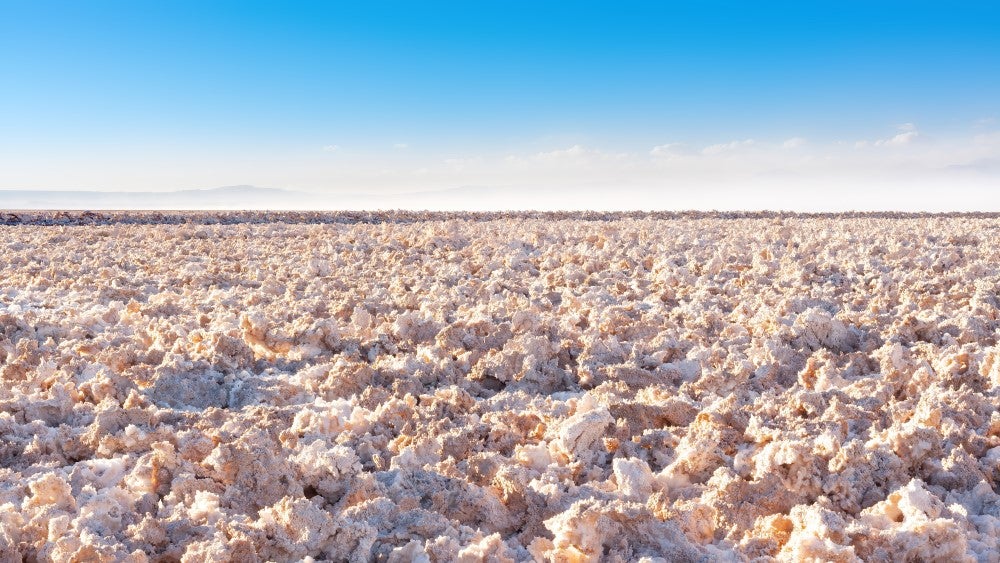
These applications now face additional challenges as attention turns to how mining companies might reduce their environmental impact while maintaining productivity gains and abiding by new rules. This shift in focus internationally highlights the need for more sustainable slurry processing and management.
The road forward involves not just putting in place more dependable energy-efficient machinery and equipment, but also collaborating directly with businesses that can build solutions specifically for optimum and sustainable outcomes.
KSB’s global network supports green mineral mining
KSB Mining is working with companies to make the process of mining battery metals more efficient. KSB offers a number of slurry and non-slurry pumps that are currently in use and can be used in the brine or spodumene process applications.
Those particularly suited for spodumene include the GIW® LCC-M for low and nonabrasive slurries, the GIW® LSA for severe slurries, and the GIW® MDX for extremely abrasive and aggressive slurries. When processing brine, the GIW® LCC, GIW® LCV, GIW® LSA, GIW® ZW, and KSB’s MCPK product ranges are appropriate. The LCC range of pumps is the most energy-efficient slurry centrifugal pump on the market with efficiencies reaching the 90% range.
KSB serves customers all over the world, with 37 production sites in 18 countries and nine foundries on three continents, and more than 3,500 experienced service staff ready and equipped to offer complete packages of custom-design and off-the-shelf products and services.
Currently, the company has MCPK pumps installed at a carbonate plant of one of the world’s largest lithium production sites in Chile. This pump is also being used to process brine, at a carbonate plant, in Argentina.
In Australia, MCPK, CPKN, and Movitec pumps are being used at a refinery to convert spodumene to lithium hydroxide (LiOH).
KSB has decades of specialized experience in water, solution, and slurry pumps, valves, and technical/training services. Its team of experts can help choose appropriate pumps for specific applications, create safer work environments, and avoid unnecessary and costly maintenance, repairs, and related downtime.
Dedicated and highly technical service staff at KSB regional sites can also devise forecast and inventory management so customers always have the OEM spare parts required.
To find out more, download the whitepaper below.