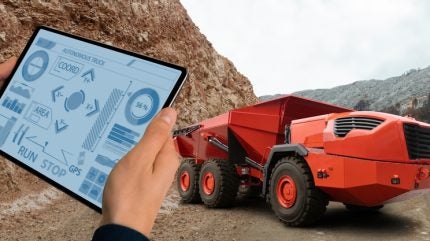
Autonomous vehicles (AVs), for example, represent significant promise for the mining sector. As of July 2024, GlobalData’s Mining Intelligence Center (MIC) was tracking 2,080 autonomous haul trucks operating on surface mines across the globe. By 2026, it expects this number to increase to c.2,800, as operators increasingly recognise how the use of tele-remote/autonomous machines in mining environments can deliver enhanced safety, reduced costs, improved productivity, lower maintenance costs, reduced machine damage, increased equipment lifetime, and reduced manpower.
But mining has been traditionally slow to adopt new technologies. While there is a clear need for a cultural shift toward embracing innovation and collaboration to accelerate digital transformation, a significant challenge remains in overcoming the entrenched old-fashioned mindset within the industry.
The connectivity conundrum
Widespread adoption of such technologies, particularly of Level 4 and Level 5 autonomous vehicles, will require 5G and subsequently, wireless networks. 5G is capable of handling larger amounts of data at much higher speeds than existing mobile networks, all with lower latency than previous standards. AVs are expected to generate and request enormous amounts of data thanks to the complexity of the self-driving task, and they will need to be in constant communication with other vehicles and smart driving environments as well as intelligent cloud-based support. In essence, a fully functional, scaled-up 5G network will be critical.
The need for this infrastructure has proven a key barrier to the uptake of transformative tech such as AVs with many sites experiencing limited network coverage, inadequate bandwidth, inconsistent device standards, low collection rates, and heavy reliance on manual inspections.
Connectivity issues in the mining industry are multifaceted and significantly impact operational efficiency, safety, and communication. For example, many mining operations are situated in remote areas where the infrastructure for reliable internet connectivity is either lacking or non-existent. This remoteness complicates the installation and maintenance of communication systems, leading to higher costs and operational inefficiencies.
Many operations still rely on outdated networks that until now do not provide the necessary latency and reliability for modern applications.
“Connectivity is a major issue,” says Jack Chen, CMO of Huawei Oil, Gas and Mining BU. “For underground operations, this is particularly problematic, where personnel are often working in dangerous or uncomfortable environments.
“At Huawei, we are leveraging our strengths to help the industry to digitalise. In particular, we are working to make operations safer; to make personnel more comfortable and working away from a hazardous environment.”
Crucial to this is the creation of a digital ecosystem and IT infrastructure built on AI capabilities to help support these leaps in productivity.
New heights for automation
In the mining industry, Huawei has worked with numerous partners to implement more than 100 scenarios-based mining applications that are based on Pangu mining models, which offer a set of automated tools to eradicate manual processes and ultimately help customers, partners, and developers operationalise AI.
By utilising End-2-End wireless communication networks, connections are created to ensure safe mining operations, allowing remote control in remote and high-altitude mines and tailings. Huawei’s core network 4G/5G co-platform’s unified control plane simplifies O&M, while a dual-device backup in the core network, remote disaster recovery, and high reliability addresses the intrinsic safety and efficiency issues faced by onsite production staff.
“We have helped customers achieve remote control and autonomous driving in open-pit mines in extreme climates such as plateaus and deserts,” says Theodore Shao, VP of Mining, Oil & Gas Industry, Latin America Enterprise Business Dept, Huawei. “The online operation rate of mining trucks reached over 99%. We have established innovative partnerships with customers in the Middle East, Brazil, Algeria, and Angola, focusing on intelligent mining and intelligent oilfield construction.”
Huawei has assisted a range of global mining companies in achieving regular unmanned driving operations in open-pit mines. At the Yimin open pit mine, for example, Huawei played a crucial role in the planning of deployment of 100 vehicles by 2025, which allowing the operation to run 24/7. At one high-altitude mine in Lanping County, Nujiang, located in Yunnan Province, China, the introduction of autonomous driving engines means vehicles can easily handle road sections that are often challenging for human drivers. Autonomous driving trucks currently have tour trajectory planning modules that can adjust the vehicle speed based on the terrain.
As well as dealing with the difficult terrain, engineers have added a hybrid grouping capability that manages not only their autonomous driving vehicles but also manned vehicles and remotely controlled excavators. This coordination capability helps to ensure stable operations across the entire road section the pilot sits on. The solution, jointly proposed by Huawei and partner, uses a cloud platform to run a unified brain for the mining area that can plan paths for multiple vehicles to avoid conflicts. The planned paths include key coordinates and driving speeds and expected arrival times at each key node, as well as the control modes required by different vehicles. This ensures that the vehicles are evenly distributed around the work area to avoid congestion.
Driving transformation
As well as improving efficiencies and allowing continued operations in challenging environments, automated measures are going a long way to solving the skills shortage plaguing the industry. Mining executives are finding it harder than ever to attract and retain the necessary talent, there is a pressing need for mining companies to create safer and more inclusive work environments to attract young talent.
“Many mining environments are not safe or comfortable to work in,” says Mr Chen. “We can deploy systems such as remote-control drilling and shovelling, or autonomous trucks in challenging locations, which means fewer people are working in these environments. Instead, they have a comfortable, air-conditioned room which they can work from.”
As focus within the industry shifts towards technology roles, particularly due to advances in automation and digitalisation, the need for a workforce that is not only skilled in traditional mining practices but also adept in new technologies grows.
“Existing workers need to upskill and we can give them this training,” says Mr Shao. “When we introduce the new technology, we are not necessarily reducing the labour. It’s about enabling someone to do the work remotely and safely.”
Intelligent transformation
Today’s mining companies are facing three key challenges: safety, recruitment, and efficiency. They are increasingly struggling with low overall production volumes and inefficient transportation, with vehicle dispatch frequently inefficient and fuel costs extremely high. Truck and shovel operation is often not coordinated, resulting in delayed production data updates and suboptimal mineral blending plans, ultimately leading to decreased product quality.
Automating operations is a critical step forward for the industry, helping to address all of these issues, but it is only possible through intelligent transformation, robust networks and reliable connectivity. For more information on how Huawei’s network expertise can help your operations evolve, visit www.huawei.com/en/industries/mining