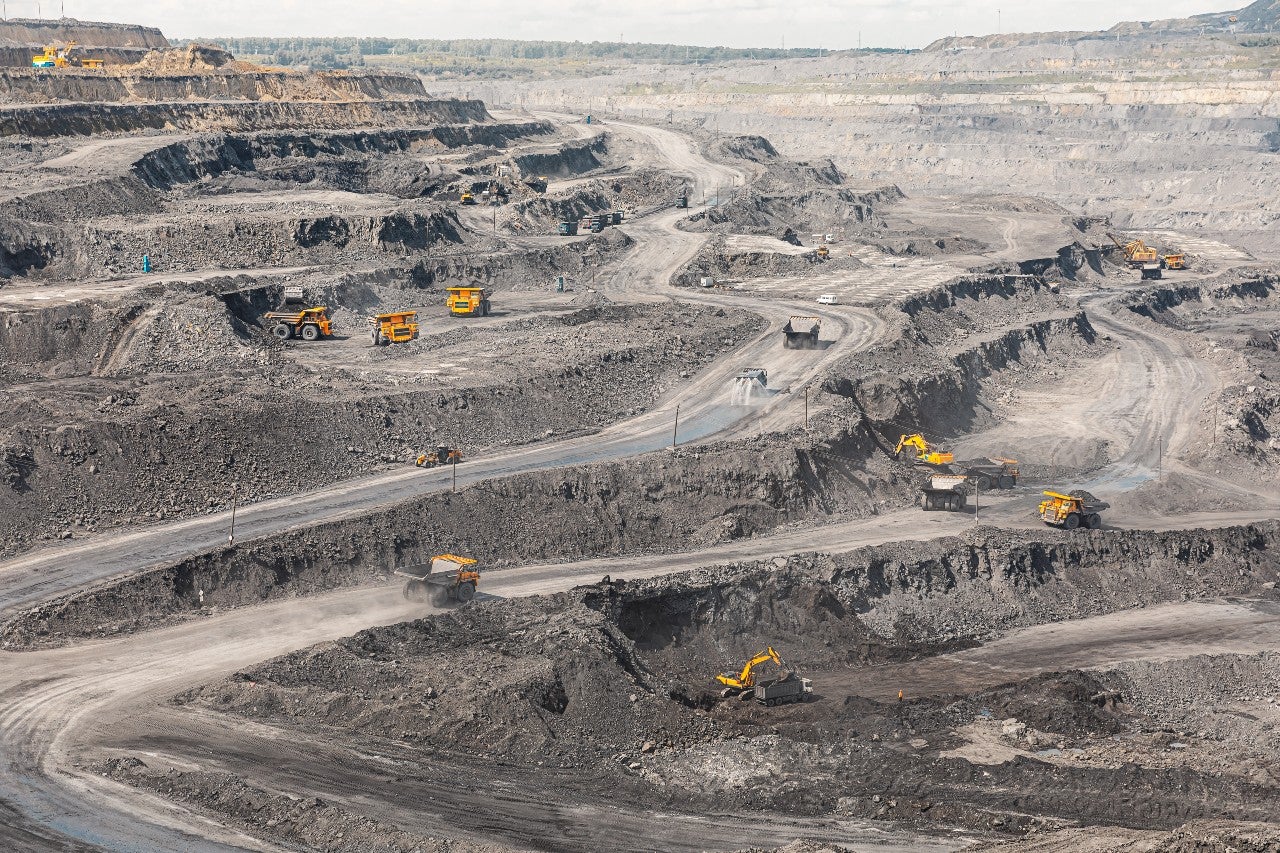
Home to huge numbers of personnel and pieces of equipment operating across numerous different locations, many mining sites are still overlooking the value of one abundant resource: data.
From personnel tasks and location information, to equipment condition and downtime durations, having a detailed oversight of exactly what is going on in the mine provides unparalleled opportunities to optimise operations. Once captured and analysed, operational data can be one of the mine’s most valuable assets.
Operators that successfully harness their data can leverage powerful insights to control and refine their processes, maximising their productivity. The problem is traditional, manual methods of management can’t keep up with this volume of data – pen and paper are not simply powerful or dynamic enough.
Today, digitisation is transforming mine management. Innovative technological tools are unlocking new ways to enhance efficiency, engagement, and safety. But achieving the right level of transparency, communication and action is not always easy – it requires the right partner.
Alcoa of Australia is one of the world’s leading bauxite producers. Over the past seven years, it has nurtured a close, valued partnership with mining operation technology experts Haultrax. Based on a strong history of collaboration and mutual respect, Alcoa and Haultrax have worked hand in hand to develop the best operational tools for the job.
Alcoa’s Willowdale site, located near Waroona, was the first customer of Haultrax’s flagship FleetOps reporting system and helped develop FleetOps into the most cost-effective way to measure a mine’s productivity. Now, Alcoa has launched fleet management system FleetControl at its Willowdale site with huge success.
What lies at the heart of this productive and dynamic working relationship? Mining Technology explores the enormous value of working with a trusted partner and reflects on the challenges that Alcoa and Haultrax’s partnership has enabled them to overcome.
The FleetControl difference
Before working with Haultrax, Alcoa, like many other operators, relied on highly administrative management processes.
“Everything was really manual – there was no visibility of where our fleet and people were and what they were doing,” says Alcoa production superintendent Jodi Racco. “We had two-way radios and telephones and that was about it.”
Data availability was slow and limited, making it difficult to visualise production rates from a short-interval perspective. For planning and budgeting, inaccurate or deficient data meant that more assumptions had to be made, and costs could go overestimated.
Haultrax’s lightweight fleet productivity reporting system FleetOps had already demonstrated its value, enabling accurate mine plan management and real time productivity accounting. With FleetControl, Willowdale’s operation opened a new dimension of analysis around the reasons why production targets weren’t being met.
“Now we can find out in real time where our assets and people are, what they are working on and what is stopping them from operating,” explains Jodi. The data covers not just high-level production but also details delays, queues, and other operational inefficiencies. These crucial metrics can be viewed at any time by accessing the FleetControl dashboard on a phone or tablet, giving Alcoa’s operators maximum mobility and flexibility.
“It gathers enough data to give us the ability to dispatch in the way we would like to dispatch. Keeping everyone informed all at the same time about where everything is makes our operations more transparent,” Jodi explains. “We’re able to make real-time decisions and identify trends to take directionally correct actions.”
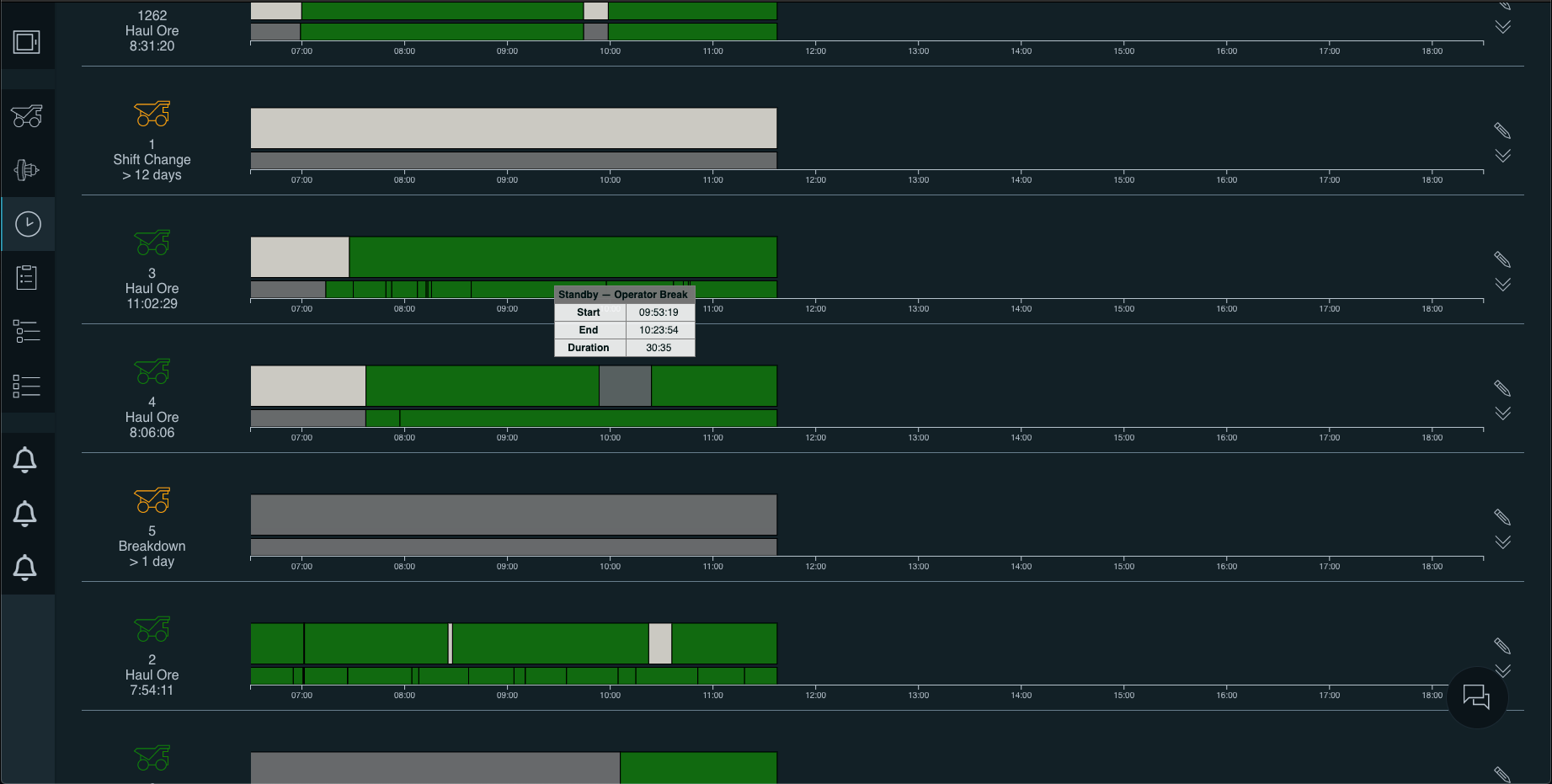
When handling vast amounts of data, balance is crucial. The challenge is to deliver the most relevant information to the right decision-makers. Jodi explains: “What attracted us to the Haultrax model is we see what we want to see in small enough chunks that you can digest it, providing us with simple and effective production information.”
As well as better budgeting and workflow management, greater operational transparency and more effective communications also improve safety. “Data is power,” Jodi emphasises.
The key to successful implementation
At the heart of the success of FleetControl’s implementation at Willowdale is the cooperation, communication, and support between Haultrax and Alcoa.
“The biggest thing is that if I ask for something to be done, it’s done in a timely manner,” says Jodi. “And if it can’t be done, we are informed. It’s the relationship that makes it work.”
Internal communications were just as crucial to implementation across the entire operation. Including operators at the pre-implementation phase means that every crew member feels that their voice is heard, and their needs reflected in the FleetControl solution.
“We met with each crew beforehand, and they had input about what they wanted to see,” says Jodi. “We were able to sit with them while they were designing and making it. That crew engagement makes it much easier to implement.”
This approach allowed Haultrax to develop a system for Alcoa that worked for the site and met the needs of the personnel.
“The difference with Haultrax has been the levels of customisation and personal service. Haultrax understands how we work and works with us to achieve what works for our operation,” says Jodi. “We knew we had a business partner who would work with us through everything.”
An essential part of the successful change management process has been taking a ‘bite-sized’ approach. At the Willowdale site, implementation started with a simple production accounting/reporting system (FleetOps) and then grew with the addition of the mining operation management and dispatching module, FleetControl. Rather than a complete overhaul overnight, Haultrax and Alcoa have worked together to implement change one step at a time, with success following success. The result includes time, material and activity tracking as well as digital pre-starts.
“It’s not just the technology that’s important,” says Jodi, “but working together to overcome challenges to make sure that implementation and beyond is successful.”
The vision
“The thirst for knowledge is getting greater,” Jodi observes. Workers on the mine site are increasingly interested in the bigger picture. “It’s always been my vision to see a tablet for every employee that they use to do everything from the time they come to work to going home, to be able to see everything from productivity to dollars per ton.”
Haultrax is well on the way to leading Alcoa towards this vision, and FleetControl is making huge strides to provide better visibility, transparency, and oversight.
To find out more, download the whitepaper below.