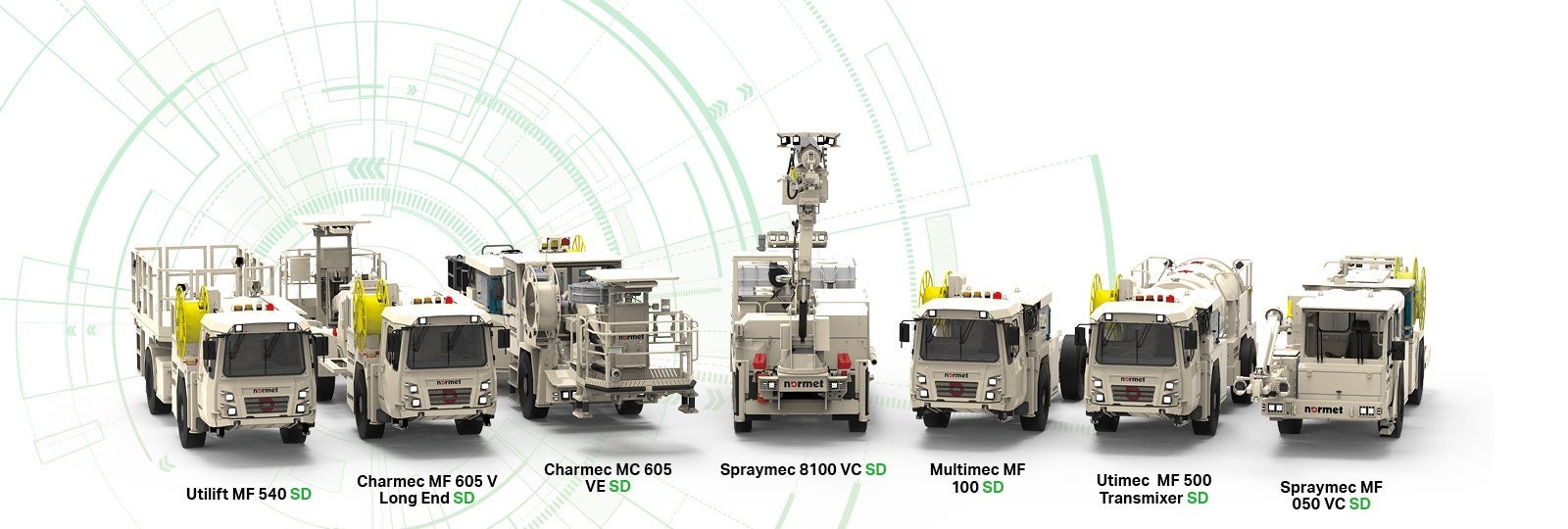
The way the mining industry operates has developed significantly in recent years, and further improvements are afoot as technology advances and is adopted globally. With approaches to environmental impact, safety, and efficiency changing, Mining Technology spoke with Ed Santamaria, chief executive officer at Normet, about future and ongoing trends that look set to shape the future of the industry.
Sustainability and waste prevention
“Sustainability is a real headline issue for the industry,” Santamaria explains. “When I talk about sustainability, I tend to think beyond a reduction in greenhouse gas emissions. That’s still a big component and very important, but there are other elements of sustainability beyond this.”
Mines are increasingly asking manufacturers and suppliers about how equipment can reduce waste and use energy more efficiently. Technology such as Normet’s SmartScan for sprayed concrete ensures that shotcrete is used efficiently to reinforce tunnels and underground mines. Additionally, Normet supports tunnelling and mining projects to ensure that products are being used optimally. For example, when used correctly, additives used for tunnel boring machine projects can drastically reduce water consumption.
Additionally new mine development takes often place in a fragile or ecologically challenging environment, hence minimising impact to environment and communities surrounding the mine is of utmost importance.
Big data and digitalisation
According to Santamaria: “Digitalisation and data is also one that is a headline issue, and we’ve seen across the mining industry that they’re using data to become more efficient. Data in itself won’t give us the improvements and the impact that we’re all looking for, it’s about understanding what data to use and how to use it.”
IoT networks in mines are continually collecting data, so operators are more informed on how every part of a mining operation is running. From predictive maintenance to making more informed decisions about production process improvement, utilising big data means that mines are running more efficiently and more productively than ever before.
Battery-electric vehicles
“Battery-electric vehicles tend to have higher levels of technology interfaces, and they’re useful in the areas of safety with collision avoidance. Additionally, diesel emissions are harmful, and electric vehicles reduce the amount of ventilation required, which is typically a huge cost to underground mines and consumer of power.”
Normet’s SmartDrive battery electric vehicles (BEV) include Li-ion battery technology and high-torque electric motors. Industrial grade components and redundant design mean that these vehicles are highly reliable, and fully reversible four-wheel drive ensures safe movement in difficult underground conditions.
Remotely operated equipment
“Something that’s really evolving is that we are all learning how to work more remotely, and part of that has been due to the Covid pandemic,” Santamaria explains. “But when you consider the location of some of the emerging mining projects, you consider some of the changes in the political landscape around the world. We’re learning to adapt and equip ourselves, and discover how can we be safe, efficient and productive in a different way than we have in the past.”
Mine excavating is increasingly going deeper, which means more dangerous environments. Above all else, the safety of mine workers is a key priority, so machinery that can be operated remotely is a major trend that will continue to shape the way mines operate.
Reskilling the workforce
Automation and remotely operated equipment doesn’t mean that the job of a miner is redundant, but rather the way that they work is changing. Hands-on workers are still required for maintenance to ensure that this new technology continues to work efficiently, and technology such as Normet’s SmartScan and SmartDrive is making their jobs easier and safer.
“What we probably haven’t done well as an industry is help our people understand what automation means, because there is a human element along with the changes in technology,” Santamaria explains. “There are locations and operations where they’ve had a huge hunger and appetite for these technology shifts, and they embrace it at all levels in the operation, but there are other examples where we’ve seen machines that have gone underground only to end up sabotaged.
“People are confronted with this technology and worry it will displace them, so we’ve got to educate people around the benefits of these technologies and what role they have to play in the transition to adopting these new technologies.”
For more information, download the whitepaper below.