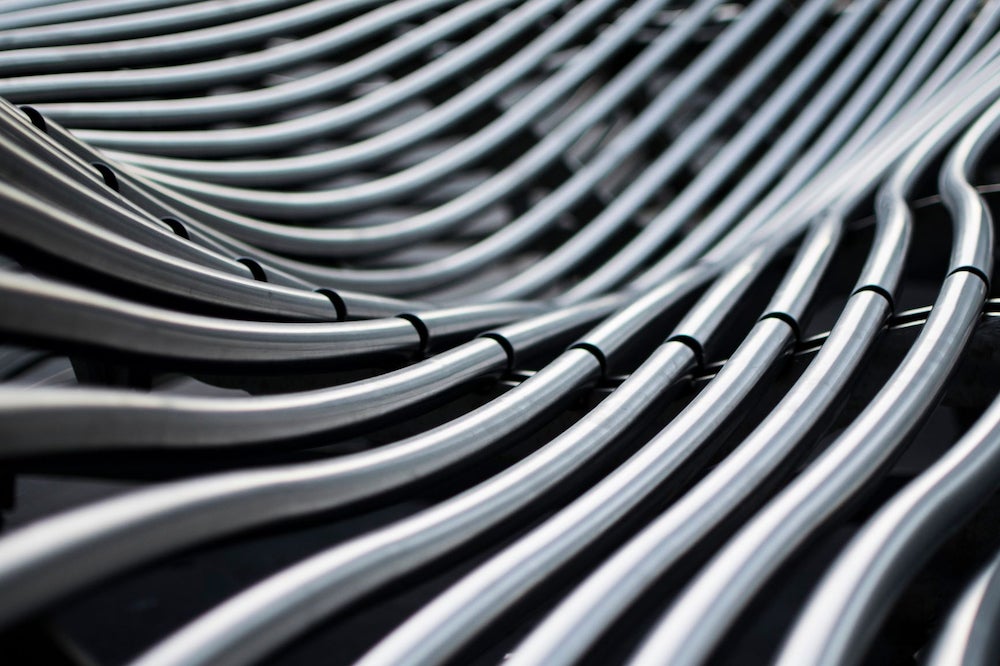
Alumina’s four per cent year-on-year growth figures are reassuring as a stand-alone number. While this creates a compelling case to produce more, the industry has been in oversupply since the global financial crisis, driven by the rise in China’s production capacity. So, what forces will shape the industry over the next decade?
Aluminium has the valuable properties of being lightweight, durable and economically recyclable. It has experienced exponential growth over the last 80 years as we continue to find novel ways for it to improve our lives.
The coming decades are no different. Electric vehicles (EVs) will displace the internal combustion engine and their build will need to be light to minimise battery costs. This means more aluminium will be needed to substitute steel.
Aluminium is also a great conductor and can replace copper in high-voltage cabling. This trend is expected to increase as the world electrifies and copper demand moves prices to levels where greater substitution is advantageous.
Some of the forecasted demand for aluminium will be met by increased recycling, but additional primary aluminium and thus alumina capacity is still required. Clear opportunities are emerging, but despite being a metal of choice for a more sustainable world, aluminium and alumina face some challenges. They need to ‘go green’.
Pressure is mounting for alumina to go green
CO2 emissions are still increasing. The 2015 Paris Agreement and decarbonisation commitments from countries and companies around the world are softening the curve, but there’s still a long way to go.
“To help meet emissions targets, the world is going to need more alumina to make the aluminium needed for things like solar panels,” says Jock Armstrong, Principal Consultant at Worley’s Bauxite and Alumina Centre of Excellence in Brisbane, Australia.
However, alumina’s energy intensity is becoming incompatible with a net zero world.
“To produce alumina, you need a few hundred degrees Celsius to dissolve it from bauxite ore. And you need a thousand degrees to calcine alumina,” explains Armstrong. “Generating this heat with ‘green’ energy is perhaps the industry’s biggest challenge since the creation of the Bayer process itself, requiring significant adaptation at existing refineries and in new designs.”
But it’s not just the energy the industry uses that’s shifting the goal posts. Geopolitics are having a significant impact, too.
The geopolitical landscape is levelling the playing field
The world is smaller than it used to be. Our interconnectedness across the globe brings immense opportunities. But shifting dynamics also bring challenges, and the alumina industry hasn’t been immune.
“Geopolitical influence on markets will reshape the alumina industry over the coming decade,” says Armstrong. “Government subsidies have underpinned energy projects and industry development, which help to support local production independence. However, the extent to which subsidies are applied has varied greatly from country to country.
“It’s a competitive industry, and extensive government subsidization has distorted production in certain geographies. Suddenly, there is a heap of alumina and smelting capacity where there wasn’t in the past. This has also resulted in significant oversupply, which has reduced the funds available for reinvestment in projects such as decarbonisation.”
These distortions have had a dramatic impact on the industry’s carbon footprint. Smelter power demand increased its carbon footprint globally from 7 kilograms CO2 equivalent per unit kilogram of aluminium (kgCO2-e/kg Al) in 2010 to over 10 kgCO2-e/kg Al in 2018.
Governments now understand the need for change, with recent actions taken to address market imbalances, which will facilitate broader industry investment. “We can expect to see increasing government and industry activity on alumina supply chain security and decarbonisation in the coming years,” says Armstrong.
Alumina decarbonisation pathways need to be mapped
The alumina industry needs to plan its path forward in a rapidly changing world.
“Our Bauxite and Alumina centre of excellence has mapped out potential pathways, and three major themes emerge in the decarbonisation roadmap,” says Armstrong.
These themes are:
- Continue using fossil fuels and incorporate carbon capture and storage.
- Electrification, potentially integrating some form of energy storage into the electrification design.
- Transition to zero carbon fuels such as green hydrogen.
“Each of these themes are underpinned by technology development, both within and beyond the refinery boundary,” adds Armstrong.
1. Fossil fuels with carbon capture
If we stay with fossil fuels, we’ll need carbon capture to meet our net zero targets.
“Carbon capture can be attractive where there’s significant investment in existing infrastructure and where stranded fossil fuels can be sourced at a competitive price,” explains Armstrong. “However, carbon capture for greenfield refineries may struggle to compete against the rapidly falling cost of renewable energy.”
2. Electrification with renewables
Electrification will be attractive in regions with lots of wind and sun. But reliability of supply remains a key issue.
“In regions with mature, well managed grids, this problem may be solved by others. But elsewhere, refiners will need to be part of the solution,” says Armstrong. “Irrespective of maturity, we predict scenarios where it’s advantageous for energy suppliers, distributors and energy users to locate energy storage facilities close to the alumina refinery.”
Numerous energy storage technologies are emerging. “We see technologies such as thermal energy storage or liquid air energy storage as having synergies with the alumina refining process,” says Armstrong. “Electrification is also heralding significant changes to the refinery flowsheet which is a quantum leap in our designs.”
3. Zero carbon fuels
Last, there is hydrogen and other zero carbon fuels. “In places where there’s less wind and sun, zero carbon fuels offer the advantage of being able to be transported long distances,” says Armstrong. “They also offer the ability to retrofit existing assets to use these fuels, but the operating costs are likely to be less favourable than electrification in many instances.
“Additionally, zero carbon fuels might ultimately prove to be the best solution for those aspects of a refinery that are challenging to decarbonise, such as the calcination process. Decarbonisation of calcination could prove to be fertile ground for technology development, with many alternative avenues being explored.”
What’s clear from each theme is that there’s no one best path to decarbonise.
“Each site will need to develop solutions based on specific factors such as the price of various energy sources, electrical and steam raising infrastructure and ownership, regional factors, refinery design, technology suitability and so forth,” explains Armstrong.” But despite the investment cost to decarbonise, there will be a level playing field as it’s a journey everyone must go on.”
One small step for sustainability, one giant leap for alumina
Refiners need to start their journey now if they’re to reach their interim decarbonisation targets and net zero 2050. And this needs to be done in a dynamic environment where new technologies are constantly emerging and prices continue to drop.
“This is what makes predicting the next five years difficult, let alone the next 30. Navigating this landscape needs careful analysis of the options as well as a close eye on technology development and the changing economic drivers,” says Armstrong. “Not all decisions need to be made now. But decisions, and a solid understanding of their implications for future investments, need to be made soon to reach interim decarbonisation goals.
However, despite these challenges, Armstrong believes there are opportunities to create a competitive advantage by successfully navigating this journey.
“Those that don’t decarbonise will simply lose their licence to operate. Those that make poor investment decisions will suffer the consequences of regret capital,” he says. “The success stories of the industry in 2050 will be those that find the best decarbonisation solutions for their assets.”