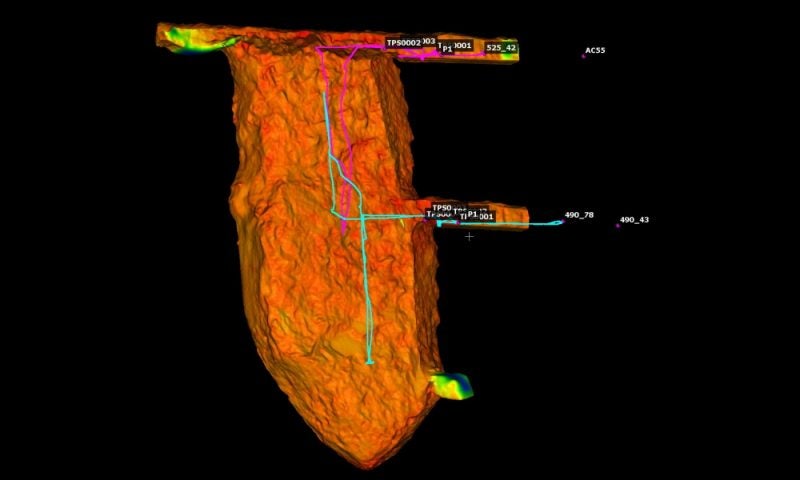
Unmanned Aerial Services (UAS) specializes in providing drone-based visual inspections and laser scanning of inaccessible environments—confined spaces, such as storage tanks, other hard to access areas, or in underground mines.
The company has years of experience in flying drones underground and selects the best technology to be able to capture data in restricted or cost-inefficient areas. Most inspections require the remote operation of drones, and UAS selected the Emesent Hovermap as the LiDAR mapping solution for most of its mapping applications.
The UAS team conduct inspections for customers around the globe. They recently expanded their network to support customers in Quebec, in partnership with Nemesis Intelligence, and in the US with an office in Butte, Montana.
We talk with Unmanned Aerial Services CEO Matt Mackinnon about deploying Emesent’s Hovermap technology.
When did you start incorporating Emesent solutions?
Beginning in October 2017, UAS was one of Emesent’s early adopters of the Hovermap payload for regular use in underground mines.
We performed our first paying job using Hovermap in February 2018. Since then, there has been no turning back as the mining industry has quickly adopted the technology into their daily processes and workflows. So much so that we are doing 4-5 inspections a week just in the Sudbury/Ontario area.
What problems do you help your customers solve with Hovermap?
We help customers get access to information critical to the effective operation of their mine—safely and efficiently—by reducing the data capture turnaround time from hours to minutes.
Traditional survey of underground excavations uses a cavity monitoring system (CMS), which is usually performed with a boom-mounted LiDAR scanner or borehole scanner. To maximize the CMS scanning capability, it has to be placed as far into the open area as possible so surveyors are overexposed to the dangers related to these confined and unsupported areas. These risks are avoided by using Emesent’s technology.
We can perform an inspection or survey, standing well back from the brow, arm the drone, and quickly fly into these areas. We safely capture data and the quality of the data is unprecedented: (a) it’s unseen before, the mine may not have previously had a mechanism to scan these areas; and (b) the data quality surpasses anything previously possible.
Hovermap is uniquely versatile. We are able to remove it from the drone to scan ore passes, raises, development drifts, any environment that is difficult to survey with traditional means. We attach it to a tether and lower it into areas that would be too tight to fly a drone to capture high-resolution, high-definition scans of these underground assets.
What are the customer projects you are most proud of or are most notable?
We’ve been to a bunch of different places around the world, assisting mining operations involving nickel, copper, platinum group metals, salt, and potash mines.
Kidd Creek was a memorable one because it was the closest to the centre of the Earth that a drone has been flown. Located at Timmins, Ontario, it is the world’s deepest base-metal mine below sea level, with shaft bottom at 3,015m (9,889ft). In May 2018, the customer needed information about a retired space and we were able to get all the information they required without risking personnel safety. We captured high-resolution point cloud data of multiple problematic stopes at 2,930m (9,600ft) below sea level. This is the deepest drone mission recorded in the world, with its attempt being submitted to the Guinness Book of Records.
Another memorable mission in May, 2019, was in the Democratic Republic of Congo. The mine has the biggest stope that I have ever flown (150m-tall x 40m-deep x 20m-wide). We captured this entire stope in just two, six-minute beyond line-of-sight flights. The customer had previously mapped this stope, and from their own admissions, it would normally take them over three hours with their traditional CMS from three mid cuts and the bottom drawpoint.
With Hovermap, personnel remained a safe distance from the brows and collars. The data was captured and processed to produce high-resolution, georeferenced point clouds with an accuracy ± 3-5cm – far exceeding the data coverage, quality and utility of previous CMS systems.
In November, 2019, we mapped an underground mine and infrastructure in Greenland. The underground crusher and plant were mapped with two walking scans, that took about 10-15 minutes each. To have a survey team cover the same plant area and to be able to capture all the pieces of equipment in the same amount of detail, all the corners, the foundations and all the key areas of interest, would have taken a couple of weeks and at least 40-50 setups.
We also mapped the rest of the mine, which comprised about 36 levels. We covered that entire area in less than three days with two 12-hour shifts and one 10-hour day. The main ramp area, from the portal all the way up the ramp to the very top of the mine, and its newest development were mapped by mounting Hovermap on our Land Cruiser and driving up. But all the other cross drifts we walked the scanner.
The digital mine and analytics are increasingly important for improving productivity and efficiency. How is the data used by your customers in the digital mine landscape?
Our customers are using the data from Hovermap for a wide variety of uses such as scanning stopes, structure detection, backfill heights and volumes; mine development drift over- or under-break, convergence monitoring, ground support QA/QC; and infrastructure inspections, vent raises, ore passes, and digital twins. The information we provide inputs directly to a customer’s digital mine platform.
We are able to digitize assets or infrastructure that previously were either too dangerous or too cost-prohibitive to scan, or are GPS-denied, and the data we produce improves operational decision-making.