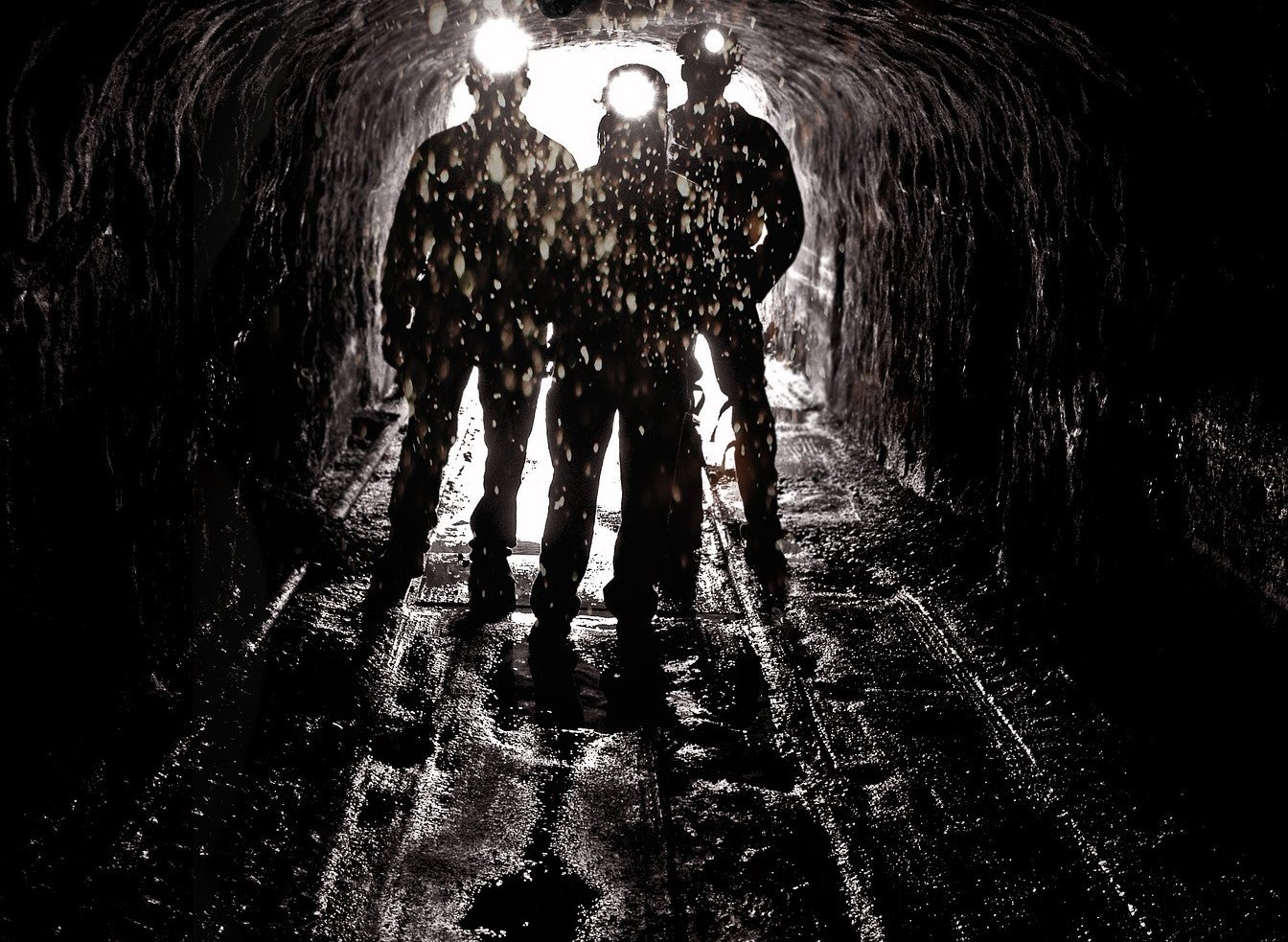
Underground mining looks set to reap considerable rewards via increased battery-operated vehicle (BEV) adoption. Potential benefits include dramatically improved health and safety conditions, efficiency, and reduced operating costs. Yet the size of the opportunity is matched by the scale of the challenge.
Sustainable mining is thought to be an essential part of the push towards the widespread electrification of transportation, as current battery technology for electric vehicles requires minerals like lithium, nickel, and cobalt. Yet beyond the broader all-encompassing goal of achieving net zero across the globe by 2050, the mining sector offers enormous potential for a tailored response to decarbonising its own modes of operation. Although mining has been relatively slow to adopt BEVs compared to the automotive sector, there is substantial scope for industry-wide electrification.
According to Mining Technology’s analysis of GlobalData’s mines and projects database, India and the USA are thought to have the greatest overall amount of mining equipment deployed at various locations. At least some of this equipment is thought to be electrified.
By contrast, Panama leads the world when it comes to electrified equipment, followed by Zambia, Sweden, and Namibia.
Our analysis also shows that countries with the largest equipment portfolios have the smallest proportion of electrified vehicles.
Many of the countries with the greatest amount of mining equipment, such as India, the USA, Australia, Indonesia, and South Africa, may therefore provide considerable investment opportunities for companies in a position to electrify mining operations at scale.
Electrified mining equipment typically consists of a variety of models which are either battery-powered, cable-tethered, or utilise overhead trolley-lines. The latter are particularly prevalent in open-pit mines requiring the use of large surface trucks. Research by GlobalData suggests that these electric trolley-trucks can already deliver savings of up to 50% with respect to fuel consumption and costs, however battery technology for such vehicles is still in its infancy.
Underground electrification
According to our analysis of GlobalData’s data, surface mines dominate the industry, although dedicated underground ventures still take a significant market share.
Prior to the ongoing Russian invasion, Ukraine led the world with the highest proportion of underground mining projects, however their mining sector is clearly beset by considerable uncertainty going forward.
Further analysis of GlobalData’s electric mining equipment database shows electrification is split across mine types, with trolley-line and cable-tethered equipment dominating surface mining, and battery technology coming to the fore in an underground context.
According to a report by the University of Adelaide in Australia, and Universidad de Concepcion in Chile, Electrifying underground mines can lead to significant benefits. They cite a study showing how electrified equipment may offer potential energy savings of “40% in ventilation and 30% in cooling”, resulting in lower operating costs. Additionally, worker safety and well-being can be enhanced via reduced “risk of flashover and electrocution” and the elimination of diesel particulate matter (DPM).
Normet are one of the companies offering BEVs designed to excel in underground environments. Their SmartDrive® technology is based on a modular BEV architecture which is “designed to optimize energy consumption and performance” with “zero local emissions”.
Mark Ryan, Normet’s Vice President of Equipment Offering and R&D, told Mining Technology about the realities of underground mines and tunnels serviced by machines running on diesel engines.
“In a tunnel environment think of something that would be running in excess of 100 degrees constantly beside you – and you’re in that environment for hours and hours… listening to the engine, getting the heat from that engine, the exhaust gas is also hot coming out, heating up the air, it can be pretty miserable actually.”
According to Ryan, miners have said that Normet’s SmartDrive® technology has a positive impact on their well-being, leading to reduced fatigue levels. The combination of reduced heat, noise, and DPMs has reportedly made workers “feel better at the end of the day.”
“I think that it’s only when you’re down there working and you see the difference, you hear the difference, you taste the difference. Being able to do the same job with a battery – it just really changes the game for the person in that environment.”
Diesel health hazards
A study by the Sustainable Minerals Institute at The University of Queensland (Australia), and The Norman B. Keevil Institute of Mining Engineering at The University of British Columbia (Canada), highlighted the well attested risks of DPM on human health. The authors point out that although up to “40% of an underground mine’s energy outlay” goes on ventilation, such systems are not able to sufficiently reduce diesel particulates to a safe level.
They cite an article written for ABC news Australia which hammered home the grave implications of long-term exposure to diesel nano-particles even in well-ventilated mines. According to the underlying report referenced by ABC, underground miners working near diesel engines can be exposed to over 100 times “normal environmental concentrations” of nano diesel particulate matter (nDPM). These particles are thought to have significant health implications going “beyond the human lungs”, which “diffuse into the blood stream” leading to a cavalcade of calamitous illnesses. Known effects include cancer, “short term irritation”, “headaches”, “smoking-like cardio-respiratory responses” and “systemic inflammation”. From a cold economic vantage point, the resultant effects of such long-term health problems in the mining workforce may have a profound effect on mine safety and productivity.
A contrasting case study cited by the Sustainable Minerals Institute report about Newmont Goldcorp’s Borden mine in Canada claimed that considerable benefits had already been reaped from its electrified equipment portfolio. These included improved safety, reduced greenhouse gas emissions and ventilation costs, “reduced megawatt hours of 33,000 per year”, and a significant uptick in staff well-being. Workers reportedly said that despite needing to adapt to new technologies, they would not want to go back to working in “traditional” underground mines alongside diesel engines.
Beyond the potential fiscal benefits of electrified mining equipment, Normet’s Mark Ryan stressed the importance of considering the human impact of adopting BEVs as opposed to persisting with diesel-powered engines underground:
“If we forget about the sales pitch for a moment, it’s about those people and their quality of life down there with this technology.”
Challenges and opportunities
Most mines across the globe do not benefit from significant amounts of electrified equipment, and there is a notable lack of such technology in countries with the largest mining portfolios. This may present a substantial opportunity for the future of mining electrification, as the market is still relatively nascent and ripe for investment. Yet considerable challenges remain when it comes to weaning the industry off diesel in favour of BEVs, particularly in surface mining where battery technology remains at the prototype stage.
Alongside technological challenges mining is facing a growing skills gap and pressure to decarbonise across the board, the latter of which relies on access to renewable energy sources which are not always readily available. According to Ryan:
“In certain parts of the world mining activities in general are obstructed by the lack of energy. The demand doesn’t meet the supply.”
This makes switching to electrified equipment in some contexts far less feasible which, coupled with industry hesitancy around the risk-reward ratio of adopting new technologies, poses a considerable hurdle for the sector ton the road to net zero. Yet as the Sustainable Minerals Institute report concludes, acquiring mineral deposits from deeper and more remote environments may make it harder for companies to stay competitive unless they evolve and take the risks required to innovate.
Ryan echoed this sentiment saying that though companies may be naturally cautious, continuing industry success stories twinned with bigger mining and tunnelling challenges may help to drive change.
Mining firms may need to take a long-term view balancing how they play their part in planetary sustainability, worker safety, and their own longevity and viability in an increasingly competitive marketplace. For those who do, the overall benefits may significantly outstrip any initial costs.