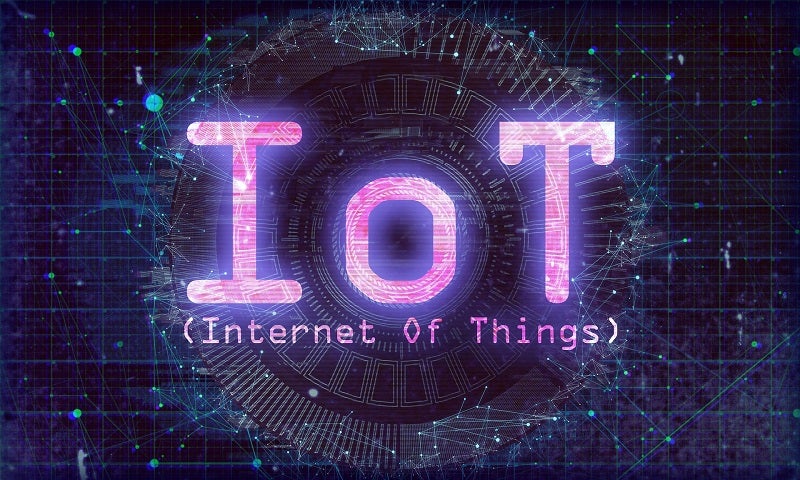
Digitalisation in mines, including data collection, data transfer and data analysis, is key to improving productivity in the sector. In recent years, digitalised open platform systems have been developed to implement Internet of Things (IoT) technology and analysis of Big Data, as well as aid the use of automated vehicles and equipment, all with positive results for operational efficiency.
However, the mining industry is still in the early stages of implementing these digital platforms. Looking forward, it is predicted that increased connectivity will further enhance mining operation efficiency, as well as enable remote diagnostics and off-site analysis while helping to improve site safety.
Why is the industry moving towards digitalisation in mines?
In order to remain competitive, mine operators must ensure that they are up to date with the latest technology, such as IoT features. After all, improved connectivity is essential to the future of mining and supporting the value chain.
“Companies are now developing an understanding of what they really want, and expanding their digitalisation,” explains Ari Mäenpää, director of digital services for Normet. “As innovators, a big driver for us is connectivity and flexibility; we don’t expect every customer to log in every day.”
With digitalisation, mine operators are given greater control over how mines are run. Data summaries on all machinery provide insight into fleet performance, material consumption and maintenance history.
As effective data analysis becomes a necessity, digital solutions are developing and evolving. In the mining industry, this will lead to reduced down-time and increased efficiency. Given the number of players in the market and the potential for future development, open platforms that allow integration of systems are crucial.
“Many companies understand that open platforms are a must-have when it comes to digitalisation.” Mäenpää adds.
What is holding back widespread rollout?
As with any industry development, a new generation of standards needs to be established, along with training and widespread adaption to meet them. Given the variety of options on the market, the implementation of standards and regulations has proven to be difficult.
“There are multiple players and they are missing standards at the moment,” says Mäenpää. “There is a lot of uncertainty.”
Normet has developed SmartWeb, which is designed to improve connectivity, maximise fleet usage and optimise maintenance and service planning. The solution can be easily integrated with Normet’s mining equipment, including concrete spraying and transport, explosives charging, scaling, lifting and installation works.
The system works by collecting data, which is then transferred by WLAN or LTE networks, or collected and stored on an IoT gateway unit. It is sent for analysis in the cloud or via a customised application before being visualised on the SmartWeb platform. Operators can then view information such as driving data, safety hazard alerts, fleet reports and service history. Normet follows Global Mining Guidelines Group (GMGG) best practises for the implementation of underground communication and data transfer.
About Normet
Normet is dedicated to innovation, sustainability and developing technology for the mining and tunnelling industry. In addition to SmartWeb, its digital technology solutions include SmartDrive, SmartScan and SmartSpray.