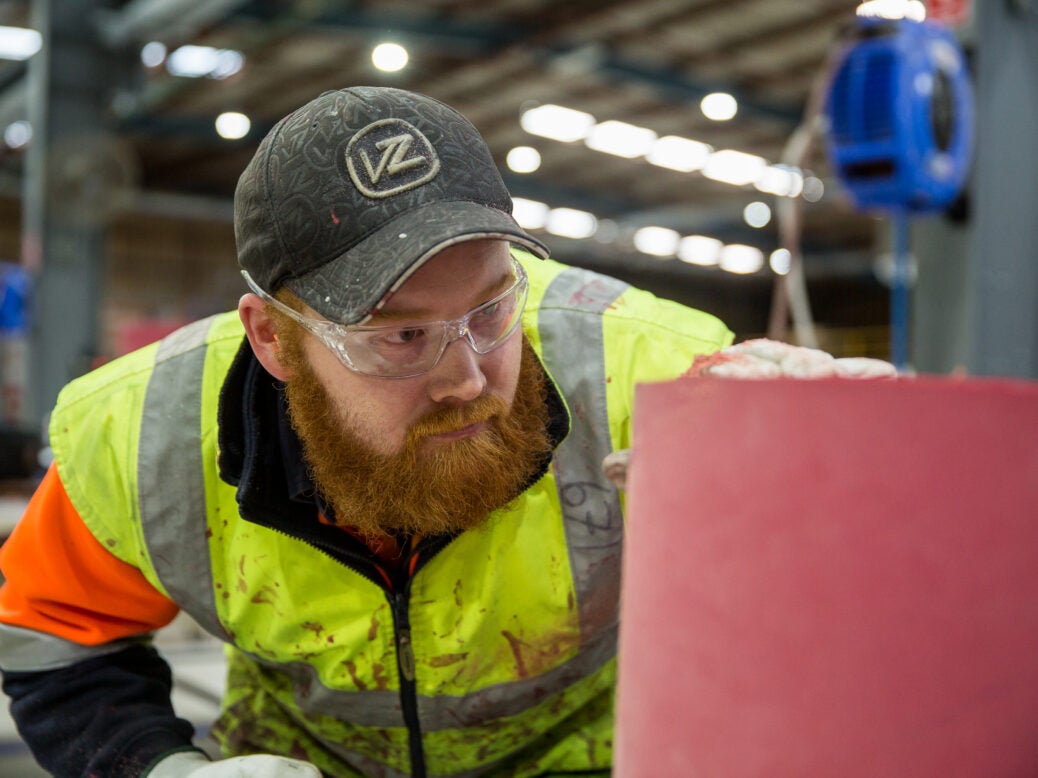
Le choix des matériaux est un aspect essentiel de toute décision en matière d’équipement. Si vous vous trompez, vous risquez fortement de compromettre l’ensemble de votre processus.
Weir Minerals propose une grande variété de matériaux résistants à l’usure, chacun d’entre eux offrant des avantages uniques et excellant dans différentes applications.
Même si la gamme peut sembler démesurée, il est crucial de choisir le bon matériau adapté à la tâche, car un matériau non optimal durera moins longtemps et augmentera le risque d’une défaillance grave qui pourrait entraîner une maintenance non planifiée.
Dans cet article, nous allons présenter notre gamme de matériaux et expliquer quand les utiliser. La première section est consacrée aux élastomères.
Quand utiliser un élastomère ?
Dans la mesure du possible, l’élastomère doit être votre choix prioritaire, car il offre généralement une durée de vie beaucoup plus longue et un coût total de possession nettement inférieur à celui des métaux dans une application similaire.
Au lieu de se dégrader, les élastomères se déforment temporairement lorsqu’ils sont percutés par des objets plus petits, absorbant l’énergie cinétique de l’impact et renvoyant ensuite l’énergie à la particule, limitant ainsi les dommages au substrat.
Cette résilience fait que, souvent, les élastomères sont le matériau de choix pour :
- Les bobines
- Le revêtement des goulottes et des réservoirs
- Le revêtement des tuyaux pour le transport des boues
- Les revêtements, roues et inlets pour pompes à boue
- Le revêtement des hydrocyclones et des vannes
Un certain nombre de facteurs influencent le choix de l’élastomère le mieux adapté à une application donnée, notamment la taille et la forme des particules dans la boue ou les résidus, les produits chimiques introduits dans le processus et la température de la boue.
Par rapport aux métaux, les élastomères réduisent également les risques liés à la manipulation des matériaux pour le personnel, car ils sont plus légers et ne s’usent pas au point de présenter un bord tranchant.
Afin de répondre aux divers besoins des mines du monde entier, nous proposons une large gamme de caoutchoucs naturels et synthétiques pour des applications spécifiques.
Pourquoi le caoutchouc naturel offre une excellente résistance à l’usure ?
Le caoutchouc naturel reste le matériau le plus efficace pour gérer l’usure à long terme par des particules fines, et le caoutchouc Linatex® est leader dans ce domaine depuis près de 100 ans.
Le caoutchouc naturel Linatex® est fabriqué à l’aide du procédé de mélange en phase liquide breveté de Weir Minerals, qui préserve les propriétés remarquables du latex naturel, produisant un matériau très durable capable de résister aux environnements humides et abrasifs de l’industrie minière.
La résistance à l’usure du caoutchouc est optimale lorsqu’il est préservé et conservé aussi fidèlement que possible au latex naturel de l’arbre. Chaque étape de la production du caoutchouc endommage les chaînes moléculaires et compromet l’excellente résistance à l’abrasion du caoutchouc brut. C’est pourquoi le processus unique qui permet au caoutchouc premium Linatex® de conserver les propriétés essentielles du caoutchouc naturel brut est aussi important pour assurer une excellente résistance à l’usure.
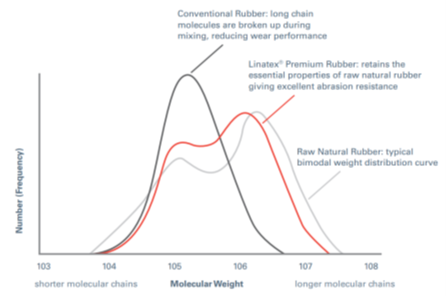
Quel caoutchouc naturel utiliser ?
Le caoutchouc premium Linatex®, notre composé de caoutchouc naturel leader sur le marché, conserve l’excellent poids moléculaire et la résistance à l’abrasion du caoutchouc naturel.
En ce qui concerne la durée de vie efficace et prolongée en cas d’abrasion causée par un angle faible et des particules fines, aucun autre revêtement ne rivalise avec le caoutchouc de qualité supérieure Linatex®. Pour les applications impliquant l’usure par des particules fines, le caoutchouc premium Linatex® excelle dans le revêtement de pompes, de tuyaux, de vannes, de réservoirs et autres. Sa résilience légendaire en fait souvent un choix avantageux en présence de particules de taille moyenne.
Sa résistance à l’usure en fait également un matériau de choix pour les travaux avec des quantités importantes de quartz dans la composition de la boue (comme c’est souvent le cas lors de l’exploitation de roches dures), et il est largement utilisé dans les activités liées au sable et aux agrégats, notamment pour le transport de sable humide.
Pour les revêtements impliquant des matériaux plus grossiers, notre gamme de composés de caoutchouc Linard® devrait être privilégiée, car elle associe une grande flexibilité à une excellente résistance à la coupe. Leur résistance à la déformation leur confère également des propriétés anti-adhérentes et anti-accumulation exceptionnelles, ce qui en fait le composé de choix pour résoudre toute une série de problèmes complexes.
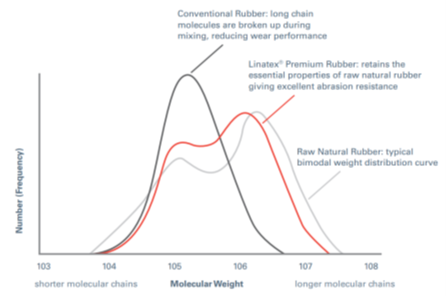
Les composés de caoutchouc naturel Linard® se retrouvent généralement dans les plaques d’impact à usage intensif, les plaques de séparation, les plinthes, les tuyaux à revêtement intérieur transportant des résidus particulièrement grossiers et offrant une protection dans les environnements abrasifs où l’accumulation de boue est un problème.
Pour les applications moulées, le composé de caoutchouc naturel R55® offre une résistance à l’usure exceptionnelle dans une grande variété d’applications de pompage de boues. Cela est dû au fait que le composé de caoutchouc R55® est suffisamment souple et résilient pour résister à l’usure des particules fines, mais aussi suffisamment solide pour résister aux dommages causés par la coupe et la déchirure de particules plus pointues pouvant atteindre 20 mm de diamètre.
Le composé en caoutchouc R55® se retrouve dans la plupart des applications moulées de Weir Mineral, notamment les hydrocyclones Cavex® ainsi que les revêtements, les roues et les inlets de pompes Warman®. En raison de sa polyvalence, depuis 15 ans, il a été déployé du circuit de broyage à l’élimination des résidus, traitant tout ce qui va des flux de flottation à la pâte.
Dans les applications hautement érosives, le R508, notre nouveau composé de caoutchouc naturel haut de gamme, offre une durée de vie encore plus longue pour les composants moulés qui doivent durer plus longtemps jusqu’à la prochaine saison. Conçu pour les applications à usage intensif telles que la décharge des broyeurs, le R508 utilise nos dernières avancées en matière de formulation du caoutchouc afin de prolonger la durée de vie des revêtements d’hydrocyclones Cavex® et des composants moulés Warman®.
Quand utiliser les caoutchoucs synthétiques ?
Notre large gamme de caoutchoucs synthétiques est formulée pour répondre à une variété d’applications spécifiques lorsque des caractéristiques autres que la simple résistance à l’usure des particules sont requises. Il s’agit notamment du traitement d’une variété de produits chimiques tels que les acides de lixiviation et les hydrocarbures, ainsi que des températures de boue supérieures à 70°.
Nous proposons des solutions synthétiques spécifiques pour les sables bitumineux, les applications du charbon, l’industrie alimentaire, les environnements acides, les alcalis et autres produits chimiques.
Notre composé de polyuréthane Linathane® est formulé chimiquement pour offrir une résistance supérieure pour les tâches générales telles que les plaques d’impact et les plaques de séparation, particulièrement adaptées aux applications avec des particules tranchantes ou du métal « résiduel », en raison de leur excellente résistance aux coupures et aux déchirures.
Chez Weir Minerals, nos ingénieurs possèdent une vaste expérience de l’utilisation des élastomères dans les mines du monde entier, et optimisent les applications pour offrir une excellente durée de vie à l’usure pour une large gamme de minéraux.
Peu importe ce que vous devez protéger, nous pouvons vous aider à trouver l’élastomère le plus efficace. Contactez-nous dès aujourd’hui pour en savoir plus.
Comprendre les métaux résistants à l’usure de Weir Minerals
Pour les applications où les élastomères ne sont pas indiqués, les fers blancs chromés de Weir Minerals, Hyperchrome® et Ultrachrome®, offrent une durée de vie exceptionnelle. Nous étudions comment chacun d’eux peut être déployé au mieux dans la mine.
Il est essentiel de choisir le bon matériau pour l’application, car un matériau non optimal durera moins longtemps et augmentera le risque d’une défaillance grave qui pourrait entraîner un arrêt non planifié.
Dans cette deuxième partie de notre article en deux volets, nous allons explorer notre gamme de métaux, en mettant en évidence leurs propriétés de résistance à l’usure et les applications pour lesquelles ils sont particulièrement efficaces.
Quand utiliser les alliages métalliques ?
Il existe un certain nombre d’applications pour lesquelles le caoutchouc ne peut simplement pas être utilisé. Les alliages métalliques demeurent le matériau de choix pour gérer les particules plus grosses et plus grossières, les températures élevées et les hydrocarbures.
Un autre scénario dans lequel le métal est privilégié est celui des zones de « haute pression », où une roue ou un autre objet rotatif tourne rapidement à côté du caoutchouc et déclenche un processus appelé inversion d’hystérésis. Dans le cas présent, les fréquentes impulsions de pression entraînent une accumulation de chaleur à l’intérieur du caoutchouc, le dégradant de l’intérieur.
Des zones de haute pression seront présentes dans toute la mine, surtout si des pompes sous-dimensionnées sont surchargées.
Quelle que soit l’application pour laquelle vous avez besoin d’un alliage métallique, il est important de comprendre les différentes propriétés de nos deux types d’alliages, Ultrachrome® et Hyperchrome®, car l’utilisation du mauvais alliage peut avoir de graves conséquences sur votre activité.
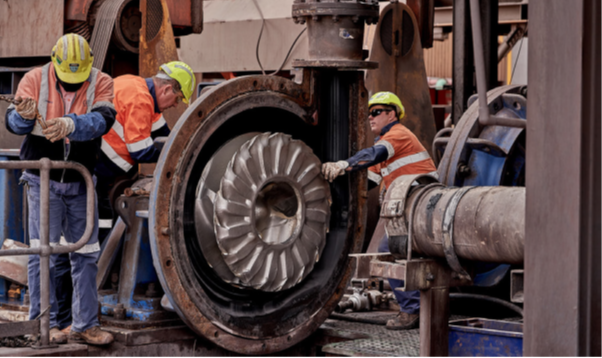
Comment Ultrachrome® fournit une résistance à l’usure inégalée dans les environnements corrosifs ?
Les alliages Ultrachrome® forment une série de fers blancs à haute teneur en chrome qui offrent une excellente résistance à l’usure dans des environnements modérément à fortement corrosifs.
Ces alliages contiennent des quantités variables de carbure de chrome, un matériau incroyablement dur mesurant 1600 unités de dureté Vickers qui procure une excellente résistance à l’usure. Les minerais typiques présentent une dureté Vickers comprise entre 300 et 1100 unités. La dureté élevée de la phase de carbure de chrome est donc essentielle pour la résistance à l’usure.
Notre alliage le plus populaire est l’Ultrachrome® A05, qui contient environ 27 % de chrome en poids, ce qui donne une teneur en carbure de chrome d’environ 25 % en volume.
Avec cette teneur modérée en carbure de chrome, l’A05 est ce que l’on appelle un alliage « quasi eutectique ». Cela permet d’obtenir un excellent équilibre entre la dureté et la résistance, ce qui le rend efficace pour les applications de pompage à usage général, ainsi que pour les applications avec des matériaux de très grande taille – parfois jusqu’à 300 mm.
Adapté à un pH de 4 et plus, l’A05 offre une résistance modeste à la corrosion à un certain nombre de composants, tels que les roues, les carters, les revêtements de volute et les inlets de la légendaire gamme de pompes Warman®.
Notre gamme Ultrachrome® compte également plusieurs alliages « hypoeutectiques », qui présentent une proportion plus faible de carbures de chrome résistant à l’usure, mais une proportion plus élevée de chrome libre dans la matrice de fer, ce qui améliore considérablement la résistance à la corrosion.
L’A49 contient 23 % de carbure pour les environnements plus corrosifs, tandis que l’A53 contient environ 18 % de carbure et convient aux environnements extrêmement corrosifs avec un Ph de 1, remplaçant souvent l’acier inoxydable. Pour les applications dans lesquelles l’érosion et la corrosion sont toutes deux responsables de l’usure, l’A53 peut atteindre une durée de vie bien supérieure à celle de l’acier inoxydable. Il est fréquemment utilisé dans les circuits de lixiviation et d’extraction acide, tels que ceux des raffineries de phosphate et de la désulfuration des gaz de combustion (DGC).
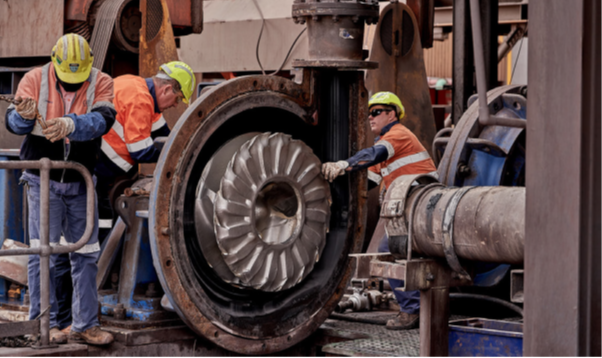
Quand utiliser Hyperchrome®, notre métal le plus solide ?
La gamme Hyperchrome® de Weir Minerals se compose d’un certain nombre d’alliages fer-chrome hypereutectiques, présentant des proportions élevées de carbure de chrome pour produire des métaux incroyablement résistants.
Ces alliages hypereutectiques étaient traditionnellement évités, car ils contiennent généralement de très grands carbures de chrome (jusqu’à 100 μm de taille ou plus), ce qui résulte en un moulage très fragile. Cependant, Weir Minerals utilise un processus spécifique pour affiner les carbures et s’assurer qu’ils ne dépassent pas 50 μm, afin de fournir une résistance à l’usure de qualité et de conserver une résistance mécanique utile.
Notre alliage le plus courant est l’Hyperchrome® A61, qui contient 50 % de carbure de chrome. Il présente une résistance exceptionnelle à l’érosion, ce qui le rend idéal pour les conditions présentant une vaste répartition de la taille des particules, telles que les boues de décharge des broyeurs.
Inversement, pour les flux contenant des particules plus grosses, l’alliage Ultrachrome® est préférable car il est plus résistant à la force d’impact de ces particules. Dès que 20 % ou plus du flux est constitué de particules d’une taille égale ou supérieure à 1 mm, l’alliage Ultrachrome® présente une durée de vie nettement supérieure.
Notre dernier Hyperchrome® A68, bénéficie de nouvelles avancées métallurgiques qui associent la résistance élevée à l’usure de l’A61 aux propriétés anti-corrosives de notre Ultrachrome® A05, ce qui en fait l’alliage idéal pour les environnements moyennement corrosifs qui nécessitent un alliage plus dur que celui de l’Ultrachrome®.
L’association de ces deux éléments dans un même matériau apporte un avantage synergique à la résistance à l’usure globale, que l’on retrouve dans les inlets, les roues et les revêtements de volute utilisés pour le traitement des boues de décharge et des résidus de broyeur.
Erreurs courantes dans le choix des matériaux
Si l’on n’utilise pas le bon matériau pour la tâche à accomplir, la durée de vie d’un composant peut être considérablement réduite et l’usine risque de subir un arrêt non planifié.
L’erreur la plus fréquente dans le choix d’un matériau d’usure est peut-être de ne pas tenir compte des différents processus et produits chimiques auxquels est soumis un flux de boue en amont de votre application. Le choix du bon matériau résistant à l’usure n’est pas seulement déterminé par les paramètres immédiats de votre application, car une multitude de processus en amont peuvent avoir des répercussions importantes sur l’usure en aval, ce qui est souvent difficile à anticiper.
Des quantités apparemment faibles de produits chimiques « inoffensifs » peuvent avoir un impact considérable sur la durée de vie globale des matériaux qui ne sont pas conçus pour être utilisés dans des environnements corrosifs.
Une autre erreur majeure consiste à utiliser le caoutchouc naturel dans des circuits contenant de grandes quantités de produits chimiques. Un exemple classique est l’utilisation de caoutchouc naturel pour manipuler des boues contenant des produits chimiques de collecteurs de flottation. Ces hydrocarbures (souvent du carburant diesel) provoquent un gonflement du caoutchouc naturel et peuvent entraîner une usure plus rapide des composants en caoutchouc.
Lors du choix d’un matériau pour des composants stratégiques, rien ne vaut une collaboration directe avec votre équipementier pour vous assurer de choisir un matériau rentable qui tiendra la route.