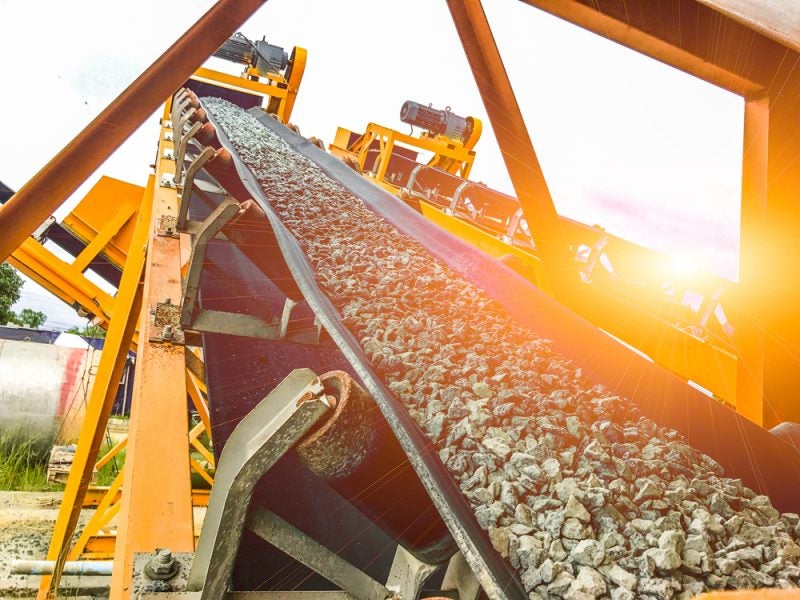
The importance of efficient level measurement at conveyor belt transfer systems can often be overlooked in a mining operation. That is, of course, until it breaks down. Some companies even predict that a malfunctioning conveyor belt accounts for up to 50% of unscheduled disruptions in production.
In fact, it has been estimated that a blockage can cost an iron ore operator as much a $1million an hour in lost production. The loss is not only significant in terms of revenue but, in the event of damage to equipment, the overall costs of replacing a system must also be considered.
According to John Leadbetter, managing director at leading mining equipment provider Vega: “Level measurement at conveyor belt transfer systems is a critical process, and not just for big mining operations. As material flows around the plant, it needs to run efficiently. If you experience a blockage or a disturbance, it can cause major setbacks and breakdowns.
“Over the years, there have been a variety of methods tried and tested to get around these problems. At Vega, we have examined these particular issues over the last 30 years and worked with the mining industry around the world to come up with solutions that are easy to maintain and don’t interfere with the operation.”
A small investment
Each of these conveyor belts systems come with a weighing system. By measuring the weight and multiplying by the speed of the belt, operators are given the mass, so they know how much material is being moved around within a specified timeframe.
With of tonnes of material produced and transported around a mine on a belt each day, it’s essential that it is not overloaded and that blockages are avoided through effective level measurement equipment.
Vega offers two solutions; a capacitive probe and a microwave beam. Leadbetter explains: “A capacitive probe is a rod which sits inside a vessel and, as the chute fills and the materials build up and make contact with the rod, it creates a circuit informing operators that the chute is full.”
The VEGACAP 62, for example, is a point level sensor for use in all areas of industry that can be positioned to provide limit control. It comes with a proven mechanical construction that offers high functional safety, increased flexibility through a retractable probe, and an extended lifetime and low maintenance requirement thanks to its robust mechanical construction.
The second solution is a microwave beam, which consists of a transmitter on one side of the chute and a receiver on the other. As material falls through and backs up to create a solid mass, it breaks the beam and stops the conveyors.
The VEGAMIP is a microwave, non-contact device, meaning it has no direct contact with the medium and can guarantee a continuous, wear and maintenance free operation. It is available as a separate instrument version to enable mounting in installation positions difficult to access, while providing reliable measurement even with very abrasive products and changing product features.
According to Leadbetter: “Operators are able to adjust the sensitivity depending on the material being measured. So if you are measuring a light material such as talc, you increase the sensitivity of the equipment to register that material, and then adjust the beam’s strength for heavier materials such as coal.
“But the way we recommend these products is based on the installation. If the operator can get access to both sides of the chute, we would recommend the microwave unit. If there is only access on one side, we would recommend a capacitive probe.
“Ultimately, whichever solution you choose, you are making a small but sound investment that can help to protect your operation from millions of dollars in lost revenue and damaged equipment.”