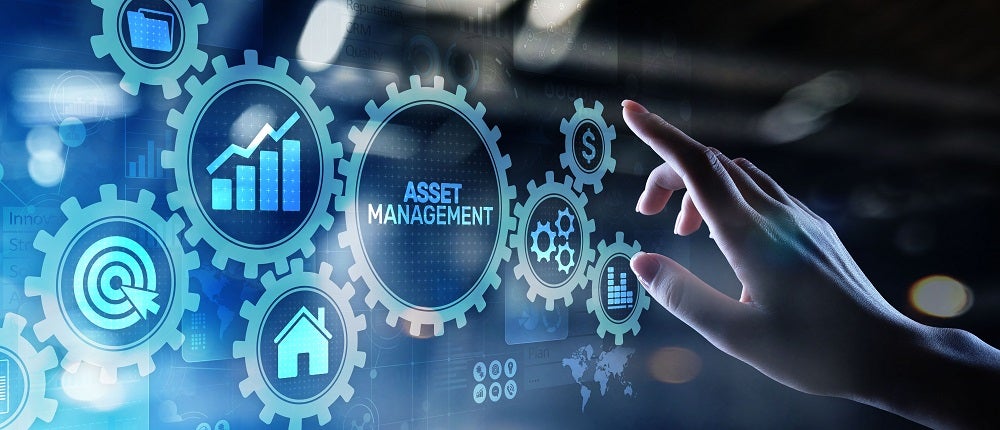
A good asset management strategy is nothing without effective execution, which means in order to run a successful campaign, businesses must turn the theory into practice in day-to-day operations.
Karsten Guster, managing director for asset management company Crystalise, weighed in on best practice in this area: “At the end of the day, owners and operators of facilities determine their strategies, including how they use teamwork and maximise their assets. But it’s what they actually do on the ground that will ultimately determine how efficient, effective and safe operations will be and whether they will be meeting regulatory requirements as well as their shareholders expectations.”
Companies such as Crystalise help business to understand their portfolio of assets by expertly analysing their facilities performance, condition and maintenance plans, comparing these metrics with industry benchmarks, and carrying out inspections of asset facilities. Included in this assessment is their management of people, contractors, materials and spares to ensure safe and reliable production at a cost-effective price.
Crystalise, headquartered in Australia, specialises in delivering “bankable results using asset improvement processes, using collective solutions and in-house industry experts” to help organisations implement best-in-class maintenance practices.
“We use analytical assessment tools when we dive into the client’s own tools, such as databases and Computerised Maintenance Management Systems (CMMS), and we join the dots.” Guster explains. “So our tools actually run on top of their existing investments. Typically, our expert practitioners will look at the history of actual maintenance activities going on at a particular facility and we develop actions plans. We look at what is going right, what is going wrong, and look where the gaps are.”
“We look at tool time, conduct surveys to determine industry best practises, we also look at the maintenance plans (both long term and short term) to see how these synergies group together. This is what we call a campaign.”
Based on this information, businesses can create more suitable maintenance strategies and change the way they are executed and operated. Incorporating these strategies into policies enables business to move away from a reactive maintenance plan, which can be myopic and inefficient, to a proactive maintenance plan. This means that asset condition and requirements are fully understood to foresee what assets will require maintenance and when, reducing the risk of business being disrupted by breakdowns.
Consistently executing a proactive, predictive maintenance strategy is key to ensuring reliable operations. Not only does this make processes more productive, it’s also a more cost-effective method of maintenance planning in the long term. Unexpected maintenance requirements and missing critical spares can lead to costly downtime and repairs. Additionally, safety and reliability go hand-in-hand, as Guster explains: “Assets that perform with very few issues normally have superior safety performance. There’s less panic, people are in control and they’re managing the work.”
“People spend a lot of time developing contracting strategies, but you’ve got to understand the synergies; where are you actually maximising your effectiveness in terms of execution of the work. Just transferring a problem to a contract doesn’t work, the responsibility is always with the actual owners for the performance of the facilities. You cannot transfer responsibilities or problems. What businesses need is to understand what contracting strategies work best for you; whether you need specialist contractors, how often do you need them, what synergies can you get with existing contractors.”
Getting the most out of maintenance and reliability improvements boils down to informed decision making to build proactive maintenance plans and carry out effective execution to optimise business assets.
“Some people think execution is just about setting a target and a budget and getting to work,” Guster explains. “Best-in-class companies understand what needs to be done so they can develop a bottom-up-budget, which is the money they need to satisfy all the requirements to deliver the performance, reliability and regulatory standards in a safe and efficient way.”