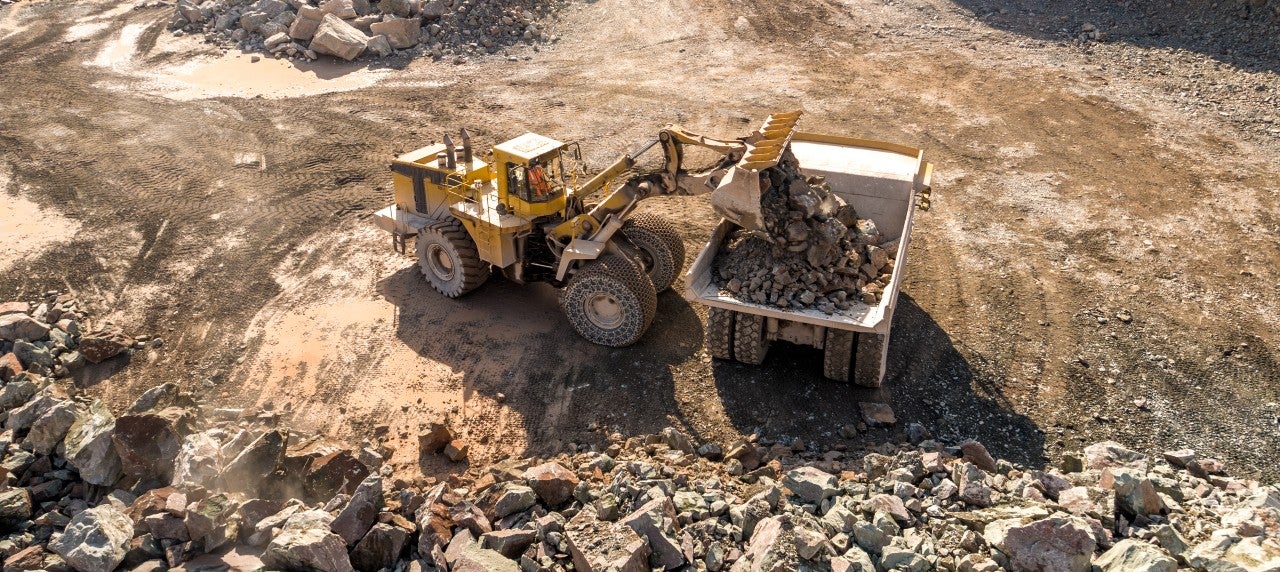
While production levels in the Australian mining industry continue to climb, the cost of production is rising at an even faster rate, leaving an ever-widening productivity gap. Companies are looking to strengthen margins and sustain profitability more than ever during the turbulence of COVID-19. The drive for productivity improvements runs all the way from board rooms focused on shareholder value, down to teams at the work face trying to reduce risk and improve efficiency. However, these initiatives are consistently observed failing to deliver sustained benefit. When productivity improvements are not directly linked to enabling and executing the mine plan, they often dissipate as a one-off activity, unable to be incorporated into business processes.
Productivity vs performance
Productivity is a measure of the ratio between inputs and outputs. If your inputs increase more than your outputs, then your productivity has decreased. Productivity improvements come from improving the efficiency of input utilisation. It is not a new concept. The term is ubiquitous throughout the mining industry. But just because a term is prevalent doesn’t mean it’s well understood. Perhaps the most widespread misconception in the industry is that improved performance equates to improved productivity, though this is not always true.
The confusion between productivity and performance stems from the obsession with increased output, and efforts to maximize the economies of scale. Performance is the measure of achieving business goals, and companies should always be striving to improve performance and productivity in unison. Achieving goals are essential to success, but when talking about productivity, focussing solely on output driven capability improvements is the very definition of putting the cart before the horse. Adding another truck to the system may help move more tonnes, exceed budget targets, and improve performance, but if your inputs increase more than your outputs, you are improving performance at the cost of productivity.
When comparing 43 mines from AMC’s SmartData™ database over two distinct periods, it is clear that production levels have increased significantly. But they have been surpassed by the accompanying increase in operating costs. The mining industry is producing more than ever, but productivity is not keeping pace with performance.
A case study
Looking at a real-world example, one mine set out to improve productivity and performance with an investment-led strategy. They spent significant capital on increasing system capabilities to develop further and faster.
In the short term, the mine achieved a significant improvement in productivity and performance. Development performance (metres advanced) increased by 37% and maximum instantaneous productivity (metres advanced per day) increased by 33%. The business milestones were completed on time, and naturally, the project was hailed a success.
Months later though, at the end of the budget reporting period, productivity had dropped significantly below the initial baseline, performance was following suit, and operating costs were alarmingly high. So what went wrong?
The first problem was that the project was conceived as a reactionary response to a growing business challenge. The constrained timeline limited the scope of improvements to short-term, high-impact opportunities, which incurred a high cost and were implemented with minimal quantification of the expected benefit.
The second problem was that the project was considered in isolation of the mining value chain. Little thought was given to debottlenecking downstream process dependencies. Once the initial gap had been closed, the development unit hit a barrier as downstream processes laboured to keep pace and mechanical utilisation dropped sharply.
The third problem, as shown in a later audit, was that the project demonstrated minimal process rigour. Decisions were made in isolation with insufficient stakeholder engagement, change management wasn’t adequately captured and tracked, and costs were allocated to a number of different cost centres.
If there is one key point to take away from their experience, it is that all productivity improvements must directly link back to enabling and executing the mine plan.
“There’s no point being able to run 100 metres in 9 seconds, if it’s in the wrong direction.”
Measure twice and cut once
The truth is that productivity improvements can actually erode value when approached in isolation, with no thought given to the mine plan or sustainability of the changes. This is often seen when a company approaches productivity improvement through austere cost-cutting, prioritising production and constraining development. This will significantly improve productivity in the short-term. But once production fronts start to be exhausted, the result is often a production bottleneck and loss of productivity. Simple measurements of productivity are not enough.
“Not all productivity is good productivity.”
To start closing the productivity gap, any company embarking on a productivity improvement project must be able to precisely quantify the long-term and short-term effects it will have on delivery of the mine plan. Once the effects on the project are understood and you are ready to proceed, a sufficiently rigorous methodology needs to be used to identify all relevant stakeholders, upstream and downstream dependencies, resource requirements, and the expected benefits.
Progress tracking and reporting needs to be comprehensive but not onerous. Reporting should reliably and accurately track productivity projects with a variety of metrics and KPIs. The best measurements to use for reporting are those that can be related directly back to delivery of the mine plan.
In another real-world example, a mining company used monthly ore production (as opposed to the broader mine plan) as the main KPI for the contractor operating the mine. The contractor took this incentive and ran with it, supplementing the mine plan with other available production sources. The mine consistently exceeded production targets and the contractor was rewarded accordingly: they had done what they were asked to do. However, variance in contained metal and mineralogy of the ore was reported by the processing department. The contractor’s initiatives had resulted in tangible downstream impacts to processing recoveries, which had impacted the mine’s revenue stream.
This once again highlights the need for precise measurements of productivity and adherence to the mine plan. What the company needed were KPIs that tracked the right volume, from the right source, with the right quality – changes that were retrospectively incorporated.
Delivering sustainable productivity improvements
As uncertainties from the current pandemic continue to suppress markets and business fundamentals, sustainable productivity improvements are a must to survive the challenges of today and allow your company to thrive when it emerges on the other side.
Productivity should not be approached as a reactionary measure. When developing a vision and communicating intent to the workforce, companies need to focus on optimising inputs, rather than focusing on output. Many companies have already taken tangible steps down the productivity improvement path. For everyone else, it’s just a question of how long it will take them to follow suit.
The increased attention on productivity improvement in the industry has seen further development and maturation of productivity improvement practices. Most now operate using a traditional process improvement methodology. Many companies also have implemented a centralised centre of excellence to develop and test improvements and disseminate learnings. This progression is key to closing the productivity gap, as the process rigour that has long been missing from productivity initiatives is now applied.
Most importantly, the purpose and target of a productivity initiative must be aligned with a company’s strategy and mine plan to achieve a positive outcome. These may change in response to changing business conditions, but experience shows that well optimized strategies tend to remain stable.
The key to sustainable productivity improvements is to adopt a steady-state approach to mine plans, keeping processes in equilibrium, with periods of logical, well planned, and targeted ramp-up. Investments in innovation, reducing operating costs, and developing operational readiness are all admirable goals. But every initiative must sustainably contribute to the bigger picture. When a change in business strategy is warranted, productivity improvements should be re-evaluated and prioritized accordingly.
For further information, please visit AMC Consultants Smart Data™