Mining operations have historically relied on inspection and manual survey to detect ground movement. However, the mining industry is rapidly evolving, and so are the technologies that support it.
Options range from the big-picture perspective offered by remote sensing techniques to highly focused insights from instruments deployed in the ground. Satellite INSAR, for example, provides precise measurement across wide areas but with limitations in terms of temporal sampling (typically 9 to 11 days between updates). Slope monitoring radar systems cover wide areas, but come with significant capital and operating costs. At the other end of the scale, geotechnical logging tools such as borehole inclinometers, extensometers and piezometers detect changes in subsurface ground stability and water content, but only at discrete locations. Selecting the right monitoring solution is a balancing act that must weigh up cost, precision, spatial coverage and sampling frequency. It's in this context that the sector is showing growing interest in wireless remote condition monitoring as a technology that is easy to use, delivers precise data from wide areas, and crucially, provides continuous updates and virtually real-time alerts.
Wireless remote monitoring systems typically comprise three elements: sensors such as tiltmeters and laser displacement sensors, communication gateways that collate and transmit data from site to a cloud-based portal, usually via the cellular network, and data visualisation software such as Senceive WebMonitor.
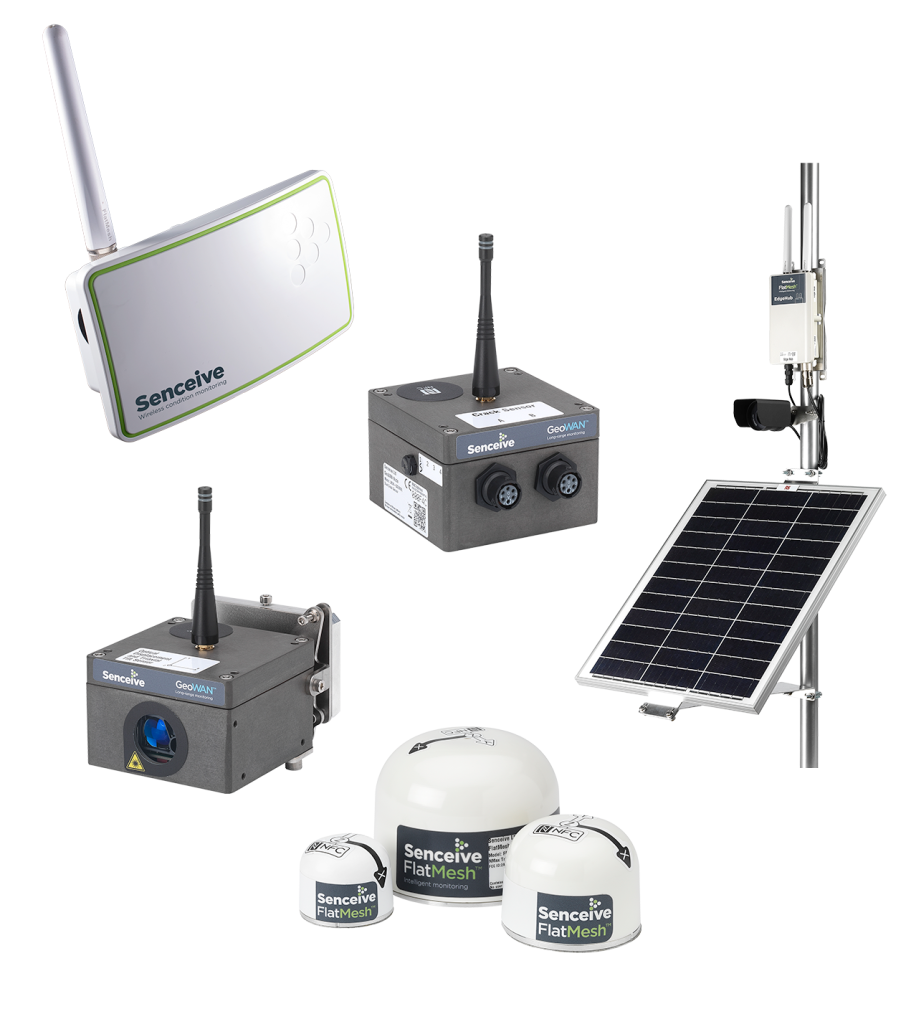
Applications
Remote wireless monitoring is transforming risk management in the mining sector, helping operators improve productivity and manage risk. Typical applications include:
- the use of tilt meters on benched slopes in open pit mines to monitor long-term movement and detect sudden failure events
- the use of multi-sensor systems on tailings dams, for example tilt meters, piezometers and vertical borehole inclinometers to detect early signs of failure such as shallow or deep rotational movement or increasing pore water pressure.
- structural health monitoring of mine infrastructure such as processing and storage facilities, railways and tunnels using a combination of movement sensors and devices to monitor engineering parameters such as strain, load and temperature.
Fewer site visits, lower risk
One of the most compelling reasons to embrace remote wireless condition monitoring in mining is the substantial reduction in site visits. This translates to a significantly lower risk to your team through:
- Keeping people away from danger: By reducing the time spent working in challenging and risky conditions our wireless remote monitoring systems allow mining professionals to focus on the data rather than the process of collecting it.
- Proactive Safety Measures: With remote monitoring and alerting systems in place, mining companies can act swiftly before ground movement and deformation evolve into dangerous and costly failures. This proactive approach helps safeguard not only the workforce but also the general public in proximity to mining operations.
Monitoring critical infrastructure
The scope of remote monitoring extends beyond just tracking ground movement. These systems can comprehensively monitor critical mine infrastructure, including tunnels, shafts, processing facilities, and railways. Here's how:
- Comprehensive Infrastructure Monitoring: remote systems can monitor a wide range of parameters, ensuring the continuous health and stability of vital mining infrastructure. Through measuring rotation (tilt), out of roundness and convergence, wireless systems provide near real-time structural movement information. Further structural insights can be obtained using sensors to monitor crack movement and properties such as strain and load. Below ground, automated geotechnical logging of piezometers, inclinometers and extensometers can provide frequent updates relating to ground water and ground movement. This comprehensive approach minimises the chances of unexpected failures.
- Data-Driven Decision-Making: by continuously providing precise data, remote monitoring technology empowers mine surveyors and engineers to make data-driven decisions. Long-term trends can be analysed so that daily or seasonal trends can be distinguished from significant geotechnical or structural events.
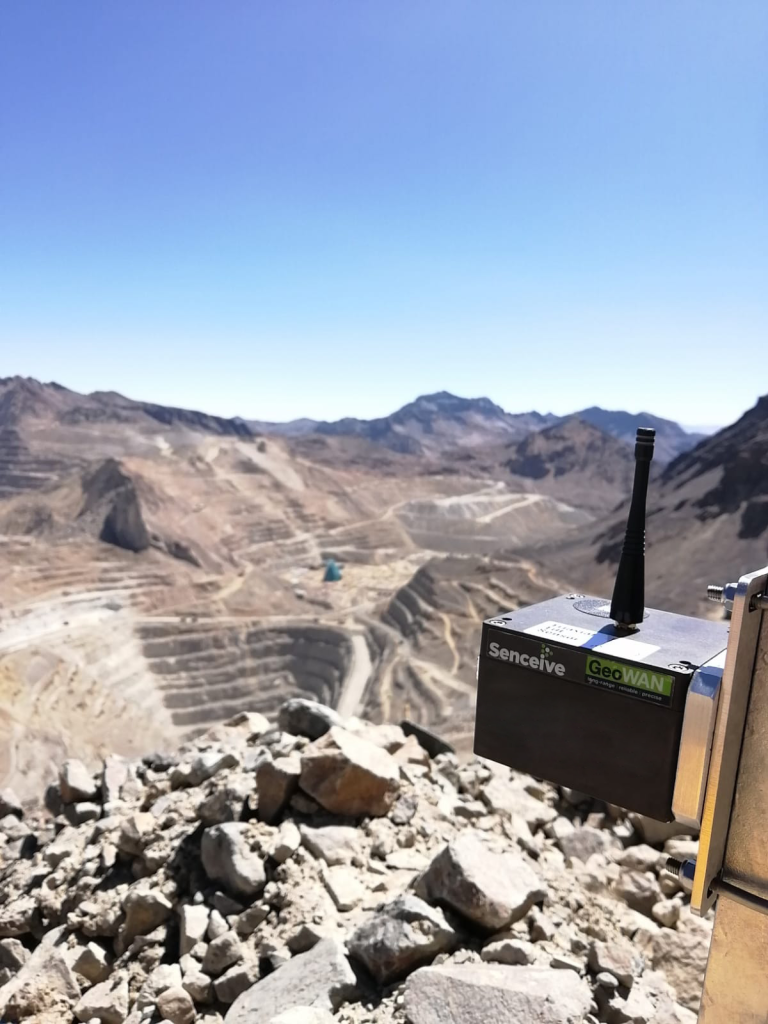
Cost-effective and low-maintenance
Remote wireless condition monitoring solutions come with several economic advantages that can make a significant impact on a mining operation's bottom line:
- Reduced Operational Costs: perhaps the most notable advantage is the drastic reduction in operational costs. It has been reported that remote monitoring can cut costs by as much as 80% compared to manual monitoring methods. This reduction includes expenses related to labour, transportation and equipment.
- Minimal Maintenance Requirements: remote monitoring systems are designed for long-life asset monitoring, with minimal maintenance requirements. This means reduced expenditure on system upkeep and more resources available for other critical aspects of mining operations. Wireless systems are made to withstand the challenges of industrial sites and harsh weather conditions.
Quick installation and data accessibility
Remote monitoring systems are designed for efficiency and convenience, with quick installation and immediate data accessibility:
- Rapid Deployment: setting up a wireless remote monitoring systems is a straightforward process, ensuring minimal disruption to ongoing mining operations. This means that you can start gathering valuable data almost immediately without running wires, lengthy calibration processes, or difficult mounting practices.
- Data at Your Fingertips: with remote monitoring technology in place, precise and up-to-date data becomes readily available. This empowers mining professionals to respond promptly to changing conditions and make informed decisions without the delays associated with repeated site visits.
The power of continuous data
Continuous access to precise data can help you move away from a deterministic approach, where slope angles are designed to a strict theoretical factor of safety, to a wider risk-based approach where a mine is designed for optimal safe performance. Here are some examples of how this can work:
- Safer, steeper slopes: a slope that is continuously monitored can be steeper than one that is not – this means reduced stripping and lower recovery costs. A slope that is moving can still be mined if monitoring data demonstrate a predictable and safe pattern of long-term creep when assessed as part of a comprehensive ground model.
- Less downtime: similarly, a risk-based approach to management of mine infrastructure can reduce the need for costly shutdowns and outages just because a defect such as a crack has been visually identified. With the assurance provided by precise condition monitoring sensors, continuous data and automated alerting it is often possible to extend the safe working life of critical assets.
In conclusion, the mining industry is transitioning towards smarter, safer, and more cost-effective solutions for geotechnical and structural monitoring. Remote wireless condition monitoring is one of the key technologies, providing numerous advantages over traditional methods. With continuous data, fewer site visits, comprehensive infrastructure monitoring, and cost savings, remote monitoring can be a game-changer for the mining sector. By harnessing the power of wireless technology, mining companies can not only improve their safety records but also optimise their operations for a more sustainable and prosperous future.
To read more about remote monitoring for mining, click here.