Dominance over global supply chains for critical mineral and rare earth elements (REE) is the next stage of great power competition, according to US Congressman Rob Wittman, who was appointed in June to co-lead the US House Select Committee’s new critical minerals policy working group.
The group is tasked with producing legislation and spreading awareness to counter China’s dominance of critical minerals. The country currently processes approximately 90% of all REEs, 75% of all cobalt and over half of all lithium. The US also relies on China for 16 of its 50 critical minerals.
Efforts are underway to diversify supply chains, with the working group’s co-leader, Kathy Castor, calling on Congress to “move quickly to support innovation in critical minerals recycling, substitution, and mining sustainability”.
While the US is looking to develop new mines and seek international partners, it is also exploring the scope for unconventional resources of critical minerals. These include recycling, reprocessing of waste from the country’s 100,000 abandoned mines, and more.
George Guthrie, principal deputy director of the US government-owned/operated National Energy Technology Laboratory (NETL), explains how his team is working to develop new US supply chains for critical minerals by recovering them from these unconventional feedstocks.
The aim, he says, is to “take materials that would otherwise not be looked at – perhaps clean up an environmental legacy along the way – and recover critical minerals at the same time”.
A broad range of unconventional resources are being studied, including produced waters from oil and gas, coal ash, solids from acid mine drainage and former waste piles.
Similar efforts are underway elsewhere, including by MTM Critical Metals, an exploration company focused on searching for niobium and REE in Western Australia and Canada.
Speaking to Mining Technology in July, Michael Walshe, who has since been appointed CEO of MTM, explained that having a potential in-country supply of critical minerals from waste streams like coal fly ash or spent e-scrap can only become ‘even more valuable’ in future.
“Historically it would not have been economic to extract metals from these waste streams,” reflects Walshe. But he points out that new technology alongside a strategic shift in response to global tensions could change the picture.
Extracting critical minerals from legacy mine waste
Recovering minerals from mine tailings has attracted increasing attention over the past several years, amid growing demand and geopolitical tension.
This year, Sweden identified significant levels of critical and strategic raw materials in mining waste in its Bergslagen region, including an estimated 21,500 tonnes of REE, 156,000t of phosphorus and 2.2 million tonnes (mt) of iron at Grängesberg, one of the area’s largest mines.
Spanish mining company Cobre Las Cruces is also testing new technologies that seek to extract cobalt, tungsten, gold and silver from mine waste as part of the EU-funded RAWMINA project. One of the methods is bioleaching, a process that utilises microorganisms to extract metals from rocks.
Back in the US, researchers at Missouri University of Science & Technology are leading the charge to extract tellurium from tailings. The material, used in solar panels, is primarily produced as a by-product of copper operations.
“I don't think there is a serious shortage for tellurium on the horizon,” explains Kwame Awuah-Offei, professor in mining engineering at Missouri S&T. “It's mainly on the critical materials list in the US [because]...if copper miners do not produce tellurium, then you would not have enough.”
China restricted exports of gallium and germanium - used in supercomputers and military tech - in August 2023. These materials, too, are primarily recovered as a by-product, in this case, from the processing of bauxite and zinc ores.
With China accounting for more than half of US gallium imports between 2018 and 2021, these restrictions have spurred new research and projects in the US.
MTM is working with Rice University in the US on a pilot project to extract gallium and germanium from waste streams.
Specifically, the company is looking to implement its flash joule heating (FJH) technology, an electrochemical process that rapidly heats material to both directly recover critical metals and make them more amenable to conventional acid leaching methods.
Missouri S&T also received $875,000 from Rio Tinto for a two-year project to recover critical minerals in by-products that come from extracting and refining copper.
Sourcing lithium from oil and gas wells
Another US initiative is looking to recover lithium from Pennsylvania wastewater, says Guthrie.
Given its critical mineral designation, the US Government wants all lithium to be produced domestically by 2030.
According to data from the Pennsylvania Department of Environmental Protection, lithium from the wastewater of Marcellus shale gas wells could supply 30%-40% of US demand - if it can be extracted efficiently.
NETL researcher Justin Mackey says that lithium can already be extracted from water with “more than 90% efficiency” in the lab, but acknowledges that new technologies must be developed for use in the field. Firstly though, Mackey says, there is a need to quantify the resource both within the Marcellus and across the US, as well as evaluate the techno-economics of extraction.
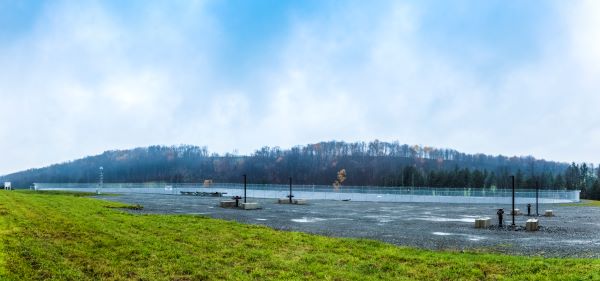
Guthrie adds: “As the next step we're working on characterising the resource broadly across the US. Our first national prospectus will be out in about six months and will be updated annually.”
This includes, he says, evaluating the potential for REE within these unconventional feedstocks.
In parallel, NETL is working to understand the environmental impact of extracting lithium and to implement a pilot facility to develop extraction tech.
The work at the US lab, which is managed by the Office of Fossil Energy and Carbon Management, is very much aspirational and faces several barriers.
Guthrie points out that the economics become “very challenging” for unconventional resources, given they are smaller in scale and typically less concentrated than a conventional feedstock. Nevertheless, it may be possible to offset some costs by looking at lithium production as a “beneficial use of that waste,” Mackay says.
Coal ash as a source of REEs
The US currently imports more than 80% of its REEs. However, many of these precious elements are present in coal wastes, which total billions of tonnes in the US alone.
Recent research led by the University of Utah documented elevated concentrations of REE (>200ppm) in active coal mines rimming the Uinta coal belt of Colorado and Utah. The findings will form the basis for a $9.4m federal funding request to continue the research.
MTM has also had success extracting REEs from coal fly ash samples using its FJH technology. A study using 60kg of ash found FJH to improve the acid leachability of REE, lithium and other metals by at least 50% compared to traditional acid leach methods.
The company says it will continue working with equipment designer KnightHawk and Rice University to further refine the process. It is also looking to trial the FJH technology on bauxite residue, e-waste and lithium-ion batteries.
Turning yesterday’s waste into tomorrow’s minerals
The challenge of extracting critical minerals from unconventional resources is two-fold: ensuring sufficient feedstock and making sure extraction is cost-competitive.
“There is overall a disconnect, I think, between societal desires to mitigate the worst impacts of climate change and the willingness to host projects that produce the minerals and metals that we need,” says Kwame.
“We need a willingness to tackle that with policies - either R&D dollars or tax incentives – to achieve the goal of the green transition and ensure that adversary nations don't use the supply chain against us.”
It is also imperative that efforts – whether mining, recycling or tapping unconventional resources – are conducted in an environmentally responsible way and this is recognised economically.
Guthrie says: “If you're thinking about developing new critical minerals supply chains in this country [the US], we need to do that in a way that's environmentally responsible.”
Kwame adds that if the US is serious, “there must be a way to compensate producers”.
Pointing to REEs, Walshe believes tech advances could help improve environmental credentials.
“It’s a complicated space, but there is lots of grant funding available for this type of technology because of the critical metals [needs] and the potential environmental benefits it could bring.”
Even with tech advances and cost reductions, unconventional resources will only go a portion of the way to securing the supply of critical minerals needed. Still, exploiting mine waste and byproducts offers the dual benefit of securing some domestic supply while dealing with legacy waste.