In Australia huge amounts of rubber products reach the end of their life each year. Mining’s contribution is largely through off-the-road (OTR) tyres, and to a lesser degree conveyor belts. Annually 130,000 tonnes (t) of OTR tyres are discarded, the vast majority (79%) of which come from the industry, according to Tyre Stewardship Australia (TSA), with agriculture a distant second, accounting for 11%.
Those figures give pause for thought, but to add to that, for every 100 mining tyres that are cast off, just two are reused in some way. The remainder are either sent to landfill or stockpiled or buried at mines themselves. TSA believes that is no longer sustainable.
Australia isn’t alone; in Chile, for example, the amount of end-of-life tyres generated annually is closer to 180,000t. However, in both countries, and around the world, the question of what to do with these tyres is pressing, with mining companies increasingly looking for sustainable solutions and governments amping up the pressure to deal with them more considerately. Some countries have successfully tackled it head on – Canada, Denmark, Italy and France among them.
Chile, too, is regulating more aggressively, now imposing directives for a quarter of mining OTR tyres to be recycled; rising to 75% by 2027 and 100% by the end of the decade. This is no mean feat for a country that is known to have 500,000t of used OTR tyres stockpiled, a figure that increases by tens of thousands each month. That said, such a law has forced the sector to act, with the likes of Canadia-owned Kal Tire ramping up its activities.
The family owned company has a thermal conversion OTR tyre recycling plant and a handful of retreading facilities operational there. It says its investment in thermal conversion was to help address the significant environmental challenge scrap tyres present. The broader goal, it adds, is to promote a circular economy in the country, something TSA has targeted for years.
The facility produces alternative fuel, steel and carbon ash, as well as enough synthetic gas to operate the plant itself. Its latest addition is a carbon ash refining process that makes a high-quality recovered carbon black, which Kal Tire says “meets, and in some cases exceeds”, the specifications required by tyre manufacturers and compounders.
“We have gone about this in the most research-intensive way to ensure this solution is scalable,” says Terry Galvin, vice-president of Recycling Services at Kal Tire. “We are now at full production, recycling tyres that would have otherwise been sitting in scrap piles.”
“Huge opportunity” for Australia to lead the way
Writing in a foreword to its research report into OTR tyres, jointly funded with the Australian Government’s National Product Stewardship Investment Fund, TSA CEO Lina Goodman says: “Times have changed, and what we did in the past is no longer good enough in a world that has woken up to the environmental dangers and enormous social harms of industrial pollution.”
She notes that in Australia there is a “huge opportunity” to step up and become world leaders in recovering and recycling OTR rubber; but other stakeholders, not just miners, such as tyre importers, recyclers, governments, indigenous people and local communities, have to become part of the conversation.
Not surprisingly, Western Australia’s Pilbara region is by far the biggest contributor to OTR tyre generation with almost 44,000 annually, 49% of the country’s total.
According to Goodman the report “makes it clear that Australia’s persistently low resource recovery rate for OTR rubber products is simply not good enough”.
It highlighted what the TSA called five key barriers to progression: the high costs of logistics and recovery; uncertainty about technologies and waste management approaches; uncertainty about end market size and capacity; and a low priority for tyre waste stewardship. However, it was the perceived low costs of on-site disposal – because licensing exemptions allow the mining sector to bury tyres on-site without penalty – that is the single biggest issue.
Using OTR tyres to build highways
For their part, mining companies are acting. Last year, BHP embarked on a major trial in partnership with Queensland’s Department of Transport and Main Roads and the Australian Flexible Pavement Association to see if waste from mining OTR tyres could be used on highways.
Two of the company’s 4m tyres, each weighing 4.2t, were turned into crumb rubber and blended into bitumen binder for road surface spraying on a major highway. “This is a great example of how the by-products of mining can be used to positively affect the local communities where we operate,” remarked then acting BMA asset president Tim Day.
Adding that such initiatives could prove to be a sustainable way of reusing tyres instead of sending them to landfill, he said it would have a positive environmental impact that could see more than 6,000t of tyres used on Australia's road network. After a hot summer of heavy use, the road was said to still be performing well.
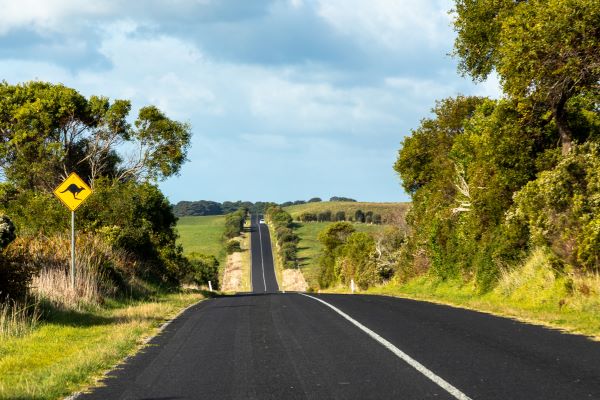
Initiatives like this may promote the so-called circular economy TSA is hoping for, but it says there is no silver bullet – and that waiting for one is “no longer good enough”. While acknowledging change doesn’t happen overnight, it warned now is the time to act. “The world has moved on and we need to move with it. We can’t bury our heads in the sand about onsite dumping of OTR rubber products anymore.”
Recycled materials for mining tyres
Like Kal Tire, manufacturers are also ramping up their efforts. Michelin has adopted metrics such as life cycle assessment to evaluate the environmental impact its products have across their lifespan.
“We recognise the profound impact tyres and services have on the mining industry and the economy. The industry is under continual pressure to meet the growing demand for critical metals and minerals, which are essential to the global energy transition, while finding ways to operate more responsibly and sustainably,” it says.
Michelin is already using sustainable, recycled or bio-based materials where possible, but has committed to producing as much as 40% of its tyre products from recycled materials by the end of the decade, and all products via sustainable materials by 2050.
To help it reach that goal, Michelin hopes to recycle 30,000t of earthmover tyres each year through its first recycling facility in Chile – adding to the purpose-built plant Kal Tire already has there. However, even before tyres find themselves at such a destination, Kal Tire’s Maple Programme aims to extend their life through its Ultra Treadä retread, and Ultra Repairä conventional repair offerings.
“Demand is growing for sustainable supply chain solutions, and to be able to demonstrate those efforts,” says Miles Rigney, vice-president of Kal Tire’s Mining Tire Group Australian company. He adds that customers choosing proven and environmentally friendly tyre solutions "can show their stewardship and make a significant contribution toward a lower carbon future”.
Drive towards a more sustainable future
Clearly a more sustainable approach to OTR tyre use and disposal is becoming mining’s next environmental, social and governance frontline. Capitalising on that, TSA says many miners have been enthusiastic about finding solutions, working on real-world demonstrations and market development, as well as tackling the issue of OTR waste products at mines.
In unison, the supply chain that includes Ascenso, Bearcat, Bridgestone Mining Solutions, Goodyear and Yokohama, in addition to the already mentioned Kal Tire and Michelin, has joined the association’s voluntary Tyre Product Stewardship Scheme, which applies a levy based on the type of tyre and rim size, capped at a maximum of A$50 per tyre. The scheme, TSA says, promotes the “responsible management of end-of-life tyres to achieve sustainable outcomes”.
The circular economy TSA hopes for is one that all participants must work hard to achieve. Its ambition is to see OTR tyres go from the factory to the mine and ultimately back to the factory for reuse. However, TSA is open about the challenges faced, particularly those specific to Australia.
“If recyclers are to create a viable market from the valuable products that can be made from OTR rubber products, we need the heft and reach of everyone involved to help us create a circular economy,” says Goodman.
She says vast distances, the logistics of moving huge and heavy tyres and other obstacles will have to be overcome. “This will be hard, we are under no illusions.”
It is clear change is coming to Australia; the question is not when but how?