A rather bizarre trend gripped the internet in 2016 called the Hard Hat challenge. In this, workers at construction sites were filming themselves using a shovel to launch a safety hat into the air, in an attempt to land it on their head. While this produced some videos of people getting smacked in the face, it also paid testament to the strength of the hat that survived falling many a time.
The hard hat, once a rudimentary piece of protective headgear, has evolved dramatically over decades, incorporating innovative materials, colours, shapes, and the latest technological advancements.
Folklore has it that Franz Kafka, the renowned Czech author and playwright, had a role in the metamorphosis of the hard hat, having developed the first one in 1912. Management professor Peter Drucker credited Kafka for developing the first civilian hard hat while employed at the Worker’s Accident Insurance Institute for the Kingdom of Bohemia. His version of the hard hat is said to have lowered injuries throughout the workforce to 25 per 1000 employees. However, this claim is not supported by any documents from the employer.
Seven years later it was Edward Dickinson Bullard, running a mining equipment firm in California, who patented the “hard-boiled hat.” A prominent American industrialist, Bullard required his workforce to wear hard leather hats in an industrial setting. After the First World War, when Bullard’s son returned to the country with a combat hat, the idea of the hard-boiled hat was brought to life.
Made with a steamed canvas, glue and black paint, the hard hat became a standard protective gear in industry. Bullard was soon after commissioned by the US Navy to also create a shipyard protective cap, marking the beginning of its widespread use.
Since then, the design of the protective helmet has been a subject of many trials. From steel and aluminium hats to fibre glass and thermoplastics, hard hats in the mining industry have been carved out of various materials for different purposes. A spectrum of colours have been experimented with for the purpose of improving safety and visibility in underground mines. A century later, from when Kafka or Bullard modelled the first hat, the mining hat is now a sophisticated piece of equipment, found in every self-respecting pit and mine around.
Design- from hard hats to helmets
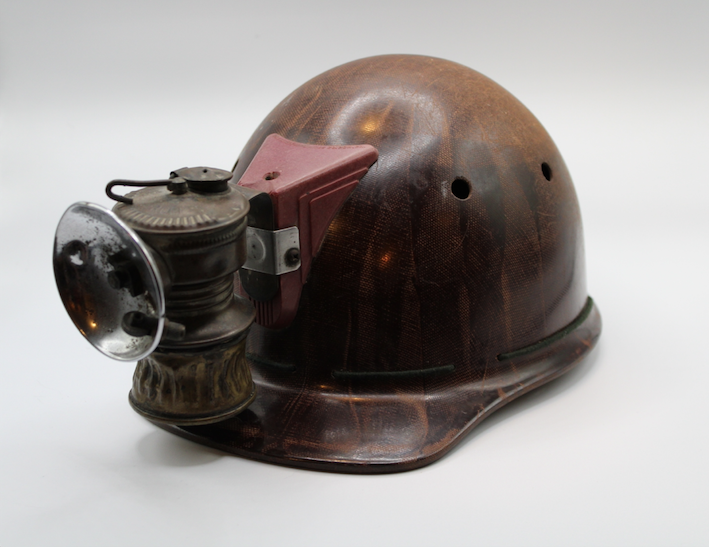
Almost each decade in history came up with a new material for the hard hat. In 1938, aluminium hats became a standard - except in the electrical industry. Moving on to the 1950s, thermoplastics were introduced, and could be injected into a cast, easily moulded and shaped with heat. Come 1997, regulators pushed to ensure that safety hats allow for ventilation, keeping wearers cool in an underground oppressive environment. The American National Standards Institute (ANSI), a private body comprised of 270,000 companies, pushed for this change, and continues to set and enforces workplace safety standards.
One pivotal moment in the evolution of mining hat shapes occurred with the introduction of the "low-profile" design. Lo-pro as they were called, these helmets featured a sleek, streamlined shape that reduced the risk of snagging on protruding objects and minimized the potential for neck strain.
From 2016 onwards, a new trend in safety hats caught on. Companies such as Bullard, taking the name of the Californian mine owner, released hats with a chin-strap, mimicking biking-style helmets. The new helmet was modelled to provide more lateral protection to the head, but more importantly wouldn’t be knocked off a worker’s head in case they trip or fall. Clark Construction, a US-based company, became the first to require employees to wear helmets instead of hats.
According to a study, the market for safety helmets was valued at $2bn in 2022, and is projected to reach $3.15bn by 2030, growing at a compound annual growth rate of 5.8% between 2023 and 2030. The mining industry is a key driver of the demand of safety helmets.
Regulatory measures for hard hats
Modern mining hats adhere to strict guidelines regarding impact resistance, electrical insulation, and flame resistance. These standards are the result of extensive research, testing, and collaboration between industry experts and safety organizations. Today's mining hats are designed to withstand not only the rigors of the mining environment, but also the unpredictable nature of emergencies such as fires and cave-ins.
Across Europe, all hard hat manufacturers are required to set a lifespan to the hat that is mentioned explicitly on the inside of the hat or embossed on its back. In the US, the ANSI enforces this.
The hard hat for underground mines therefore has to follow the ANSI Z89.1 Type I, Class G sticker regulations. New hard hats should also be logged into service by the operator when they are first worn, and accordingly removed from service when the shell of the hat is older than five years or the liner is older than six months.
The Class G hat is made to turn an impact of 6000 psi into less than 800 psi on the neck, even at extreme temperatures.
Adding cameras into mining hats revolutionized documentation and safety. These compact cameras captured real-time footage of work conditions, which could be reviewed for safety assessments, training, and incident investigations. The ability to record events from the miner's perspective provides invaluable insights into the daily challenges, but also changed the way underground resources could be accounted for in the mining industry.
Yes, hardhats can now also monitor respirable dust inhalation
In May 2023, Mining Technology reported on the latest innovation in mining wearables. Among those were hardhats now equipped with a dust exposure assessment tool, designed specifically for the mining industry.
To Bullard’s credit, he also designed measures to save workers from sandblasting accidents back in the day. While visiting the construction site for the Golden Gate Bridge in 1933, Bullard learnt how steel that was being used in the making of the bridge was prone to oxidation and needed to be sandblasted to remove rust.
Bullard’s granddaughter, Well Bullard, told the Smithsonian Magazine about how her grandfather came up with the idea “for a suit with compressed air to protect the workers.”
About 90 years later, the miner’s helmets now include a real-time aerosol monitor that goes into the backpack. The device records the person’s dust exposure at two-second intervals. Designed by Unimin and the National Institute for Occupational Safety and Health, the HELMET-Cam provides exposure data by synchronising video footage with logged dust exposure data to assess silicosis hazards, helping prevent the lung disease caused by inhalation of silica dust.