The challenges facing critical minerals supply chains – including graphite – have been on the radar of governments, policymakers and businesses across the globe for years, and yet we are still hurtling towards a supply crisis.
One such critical mineral is graphite, which makes up 95% of the anode material in lithium-ion (Li-ion) batteries – almost half the total volume. Despite its essential role in the transition, the recent IEA Critical Mineral Outlook Report 2024 cited graphite as the critical mineral with the highest supply risk score when it comes to geopolitical exposure.
If we are to ensure a secure supply of this mineral as economies transition, we must address three key challenges:
- Meeting demand, with a graphite supply deficit of 777,000 tonnes (t) per year expected by 2030, according to International Energy Agency (IEA).
- Reducing dependence on Chinese graphite supplies, which account for 93% of graphite anode production, according to Benchmark Mineral Intelligence.
- Combatting graphite’s low environmental, social and governance (ESG) score, which makes reliance on the mineral in its current form a challenge when it comes to a truly green transition.
The scale of the graphite supply crisis
Within current supply chains, there are two forms of graphite used: synthetic and mined.
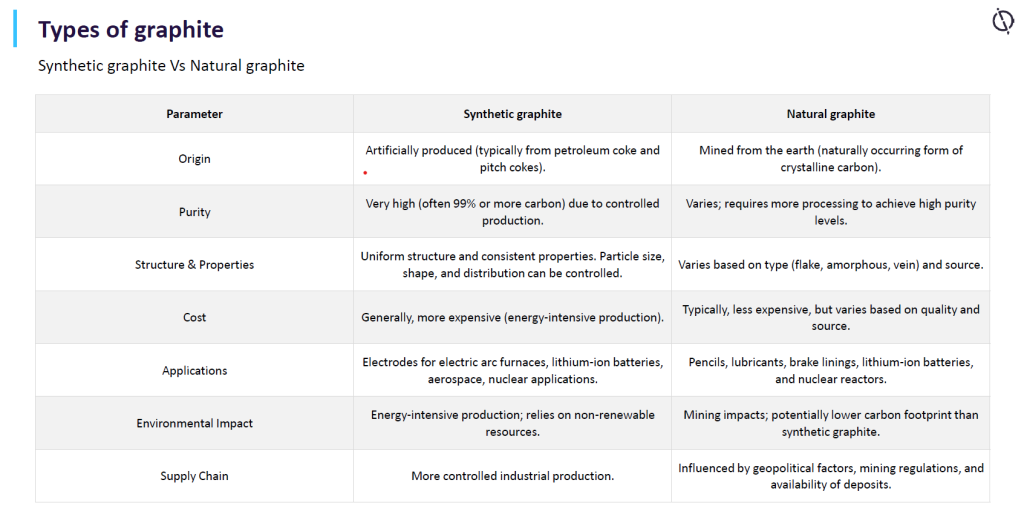
Production of synthetic graphite, which is favoured by businesses due to its higher quality, is both time-consuming and energy-intensive, requiring weeks to produce and extremely high temperatures.
Mined graphite, on the other hand is of an unpredictable quality and depends on opening new mines. To meet increasing demand, we would need at least 100 more mines, with each requiring a lengthy, expensive permitting process taking up to seven years.
Finally, the production of battery-grade graphite from mined graphite depends on fossil carbon, making both forms vulnerable to price fluctuations that can slow production, and reliant on a feedstock and process that is not only polluting but will run out.
To compound the issue further, the Western world’s historic lack of focus on building its own critical mineral supply chains has meant China is set to control more than 90% of the supply of battery-grade graphite by 2030. This is having a significant impact on US and European markets as the automotive industry competes against Chinese manufacturers that can source graphite closer to home, for a lower price – threatening nations’ economies and the green transition.
As electrification ramps up, the localisation of these critical minerals supply chains has moved up the agenda for policymakers. The Inflation Reduction Act in the US and the European Green Deal have sent clear signals that this is front of mind for these economies – it is essential to meeting demand.
Graphite's ESG credentials
According to the IEA, graphite has the lowest average social and governance score for mining, increasing its ESG and climate risk exposure significantly.
While China controls 80% of natural graphite production, much of this is imported from mines in Africa. These long and complicated supply chains are a problem. Not only can they impact price, but they also increase the emissions associated with graphite.
It is not uncommon to see graphite travelling around 50,000km before it is used in Europe, with recent studies also suggesting that emissions for graphite mining are severely under-reported.
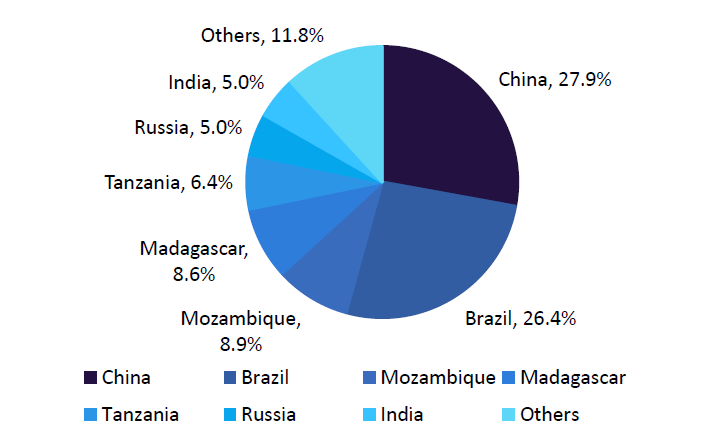
Supporting a greener transition
With critical minerals playing such an essential role in the energy transition, it is vital that we find a solution to the ethical questions mining graphite poses. If supply chains were to become more sustainable, this would enable communities to reap the full benefits of a thriving mining industry – through boosting employment, tax income and investment – without scarring the Earth.
The sector now faces an important and difficult question; how much should we really be relying on natural graphite, a finite resource that comes from fossil carbon, as we aim to decarbonise our systems?
The role of biomaterials in graphite supply
Despite the slow start, there is a way for Western economies to secure supply chains: biomaterials. Instead of relying on damaging mining or energy-intensive synthetic options, biomaterials can often be manufactured locally and from renewable feedstocks, promoting a more circular and ethical economy.
Biographite, for example, is produced from the byproducts of the forestry industry, specifically wood chips. This renewable feedstock contrasts sharply with graphite flakes sourced from mines in Africa, as it is local, abundant, low-cost and sustainable.
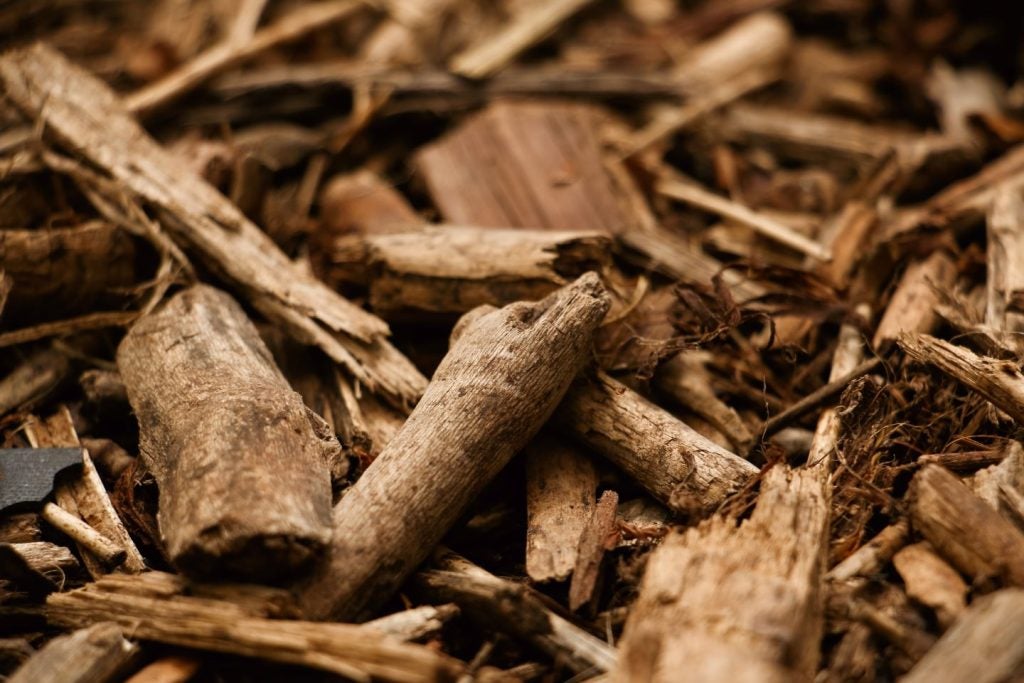
From a carbon perspective, synthetic graphite emits on average 25–35t of CO₂ per tonne of graphite produced, versus 10-15t for natural graphite. Biographite could have a negative carbon footprint as it utilises a primary feedstock, which locks in atmospheric CO₂ and low temperature processes. Additionally, by enabling localised production near electric vehicle (EV) manufacturing facilities, it reduces the emissions associated with long-distance shipping.
Biographite also consistently outperforms traditional synthetic graphite, which is favoured by battery manufacturers over mined graphite. It is a drop-in replacement that can be produced anywhere with a forestry industry, allowing countries to reduce dependence on long and complicated supply chains and take control of their own supply, bolstering local economies and green job creation.
Once scaled, CarbonScape projects that enough biographite could be produced to fulfil more than half the projected global demand for graphite in Li-ion batteries, all while using less than 5% of the forestry industry’s annual byproducts in Europe and North America.
Can biomaterials support the energy transition?
The current trajectory of the industry is unsustainable, with big questions around the reliance on mined graphite in face of growing demand.
Ultimately, the path to an economical, climate-positive future lies in onshoring the production of sustainable biomaterials like biographite – not opening more mines. This will not only provide EV manufacturers with a secure supply through cheaper, cleaner and shorter supply chains but will also open new avenues for local job creation and green industry development.
About the author: Vincent Ledoux-Pedailles, a commercial leader in the battery space, was CCO at Vulcan Energy, securing major OEM offtakes and co-leading more than €500m in funding. He was appointed as a critical raw materials expert by the European Commission and previously led battery materials research at IHS Markit, covering the industry's supply chain.