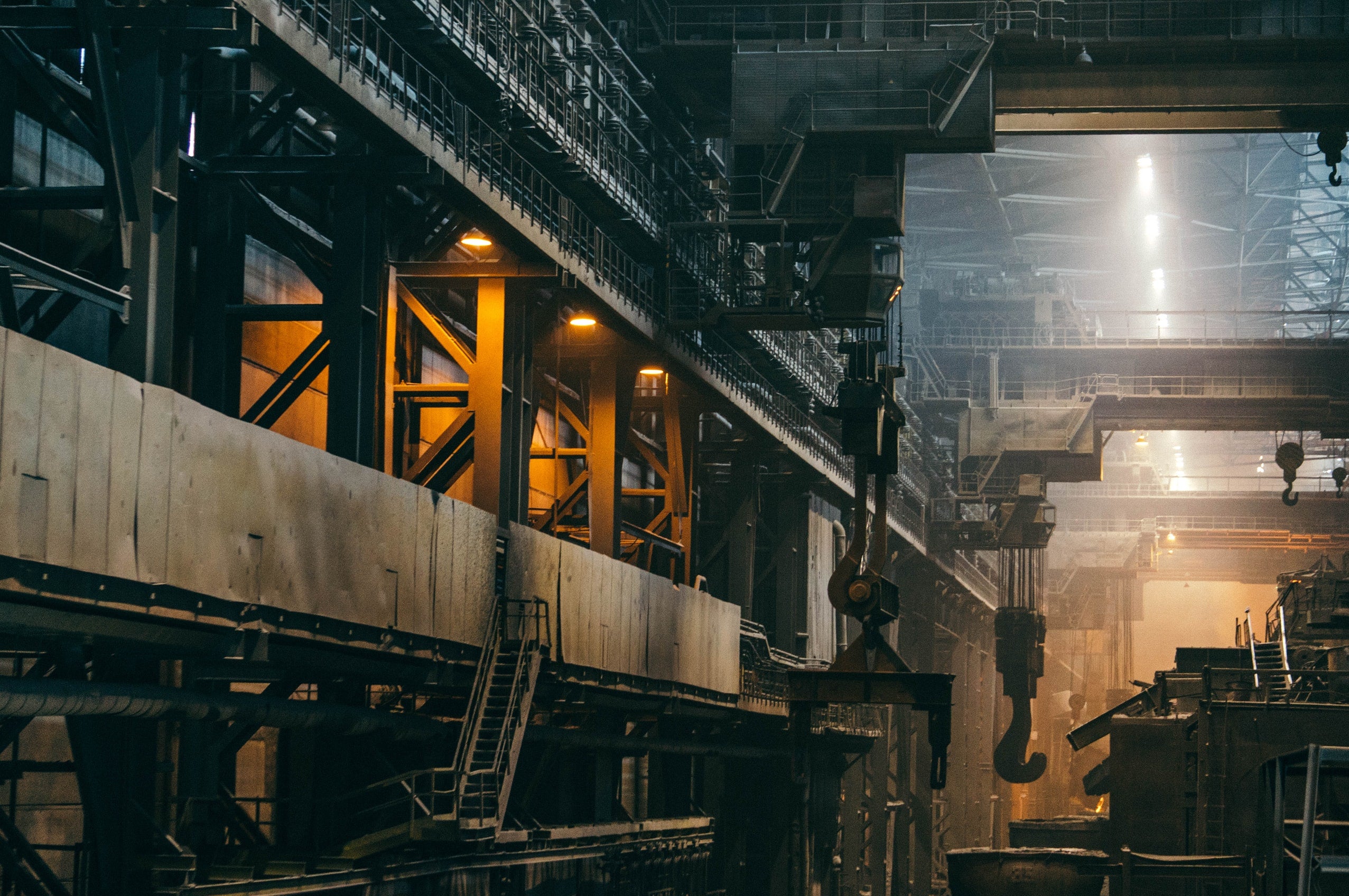
Swedish steel manufacturer SSAB has announced that it has “produced the world’s first fossil-free steel”. The steel was delivered to its first customer, Volvo Group as part of a trail delivery. Volvo had said that it will begin using the steel in its manufacturing process from this year. Plans are for smaller-scale serial production to start during 2022 and for a gradual escalation towards mass production to follow.
The steel is the product of the HYBRIT partnership between SSAB, LKAB, and Vattenfall and was manufactured by the world’s first fossil-free steel plant, which uses fossil-free hydrogen instead of coal and coke. HYBRIT’s pilot facility for the production of fossil-free sponge iron in Luleå was commissioned in August 2020 and in March 2021, Gällivare, Sweden was chosen as the location for the planned demonstration facility for industrial scale production.
“The first fossil-free steel in the world is not only a breakthrough for SSAB, it represents proof that it’s possible to make the transition and significantly reduce the global carbon footprint of the steel industry. We hope that this will inspire others to also want to speed up the green transition,” says Martin Lindqvist, president and CEO of SSAB.
The Hybrit project was first set up in 2016. Its long-term goal is to develop the technology so it can be demonstrated at an industrial scale, with hopes that this could happen as early as 2026. The idea behind the project is to produce fossil-free pellets, fossil-free electricity, and hydrogen, which involves eliminating carbon dioxide emissions from the process by using fossil-free input materials and energy across all parts of the value chain.
The production of steel is incredibly energy intensive. On average, every ton of steel demands about two tons of carbon dioxide, globally. Each year, steel production accounts for more than 7% of the world’s greenhouse gas emissions. SSAB currently produces 10% of Sweden’s carbon emissions through its steel plants, making the scaling up of fossil free production methods especially critical to achieving Sweden’s carbon emission reduction goals.
Anna Borg, president and CEO of Vattenfall stated: “It’s a crucial milestone and an important step towards creating a completely fossil-free value chain from mine to finished steel. We’ve now shown together that it’s possible, and the journey continues. By industrialising this technology in the future and making the transition to the production of sponge iron on an industrial scale, we will enable the steel industry to make the transition”.
The International Energy Agency has noted that the steel sector is “the largest industrial consumer of coal, which provides around 75% of its energy demand”. This new method of steel production therefore has the potential to reduce the reliance on coal for industrial processes such as steel production, critical in facilitating a green transition.
“By industrialising this technology in the future and making the transition to the production of sponge iron on an industrial scale, we will enable the steel industry to make the transition,” says Jan Moström, president and CEO of LKAB.