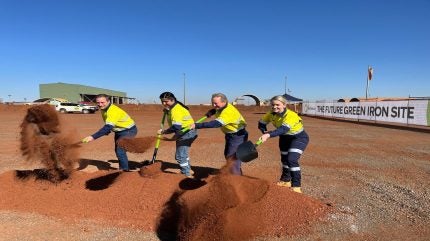
Fortescue has initiated its $50m (A$75.37m) Green Metal Project at the Christmas Creek site in Western Australia’s (WA) Pilbara region.
This plant is estimated to have an annual green metal production capacity of more 1,500t, with its first output expected next year.
It will utilise green hydrogen from the company’s gaseous and liquid hydrogen facility along with an electric smelting furnace to make “high-purity” green metal.
The company’s new green hydrogen plant can generate around 530kg of hydrogen gas each day, which totals approximately 195t annually.
New Zealand-based Fabrum collaborated on the design, build and commissioning of the liquid hydrogen plant, which it said is Australia’s largest at a mine site.
Partially powered by solar energy during daylight hours, the plant at the Green Energy Hub includes a gaseous hydrogen refuelling station (HRS) that supports ten hydrogen-driven fuel cell electric coaches.
How well do you really know your competitors?
Access the most comprehensive Company Profiles on the market, powered by GlobalData. Save hours of research. Gain competitive edge.
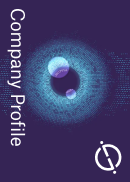
Thank you!
Your download email will arrive shortly
Not ready to buy yet? Download a free sample
We are confident about the unique quality of our Company Profiles. However, we want you to make the most beneficial decision for your business, so we offer a free sample that you can download by submitting the below form
By GlobalDataFortescue added that the gaseous HRS was backed by the WA Government’s Renewable Hydrogen Fund, which provided a $2m grant.
The Green Energy Hub also features a hydrogen liquefaction facility, liquid hydrogen storage and a liquid hydrogen refuelling station, as well as Fortescue’s zero-emissions decarbonisation prototypes.
Additionally, the liquid hydrogen plant will supply power to Fortescue’s Offboard Power Unit and the hydrogen-powered haul truck prototype, which recently arrived at Christmas Creek.
The Green Energy Hub also features Fortescue’s prototype battery-electric haul truck and a 3MW fast charger prototype.
Fortescue executive chairman Dr Andrew Forrest said: “Today is a celebration of innovation, collaboration and stretch targets, and marks a pivotal moment in Fortescue’s journey to build a green metal supply chain.
“Iron and steel are the backbone of our infrastructure; however, traditional iron and steel production processes are among the largest sources of greenhouse gas emissions. By rethinking the entire iron and steel value chain we can produce an entirely new, green industry here in Australia.
“Today’s milestone is the culmination of bringing together green sustainable mining, large-scale renewable power and green hydrogen to produce green metal. Right now, we have a once in a generation opportunity to build a green supply chain, and Fortescue is wasting no time to seize it.”