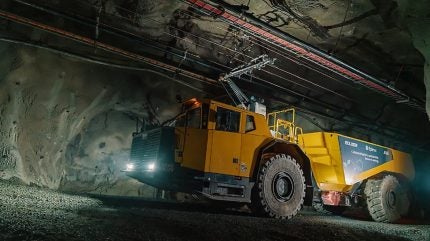
Mining company Boliden, mining equipment maker Epiroc and technology company ABB have deployed the first battery-electric trolley truck system for underground mining in Sweden.
The technology is set to revolutionise mining operations by reducing carbon emissions and enhancing productivity.
The parties deployed the first fully battery-electric trolley truck system on an 800m-long test track at Boliden’s Kristineberg underground mine in Sweden, with a 13% incline.
This marks a step closer to the all-electric mine of the future, with sustainable, productive operations and improved working conditions.
ABB global business line manager mining Max Luedtke said: “Seeing the industry’s first battery-electric trolley truck system live is not only the result of a collaborative achievement with Boliden and Epiroc, but it is truly an industry milestone.
“We launched the ABB eMine concept of methods and solutions to bring electrification to the whole mining operation, from the grid to the wheel, and the installation at Kristineberg demonstrates the power of these capabilities.”
Epiroc has added dynamic charging to its battery-electric Minetruck MT42 SG and battery system, while ABB has provided the DC converter, HES880 inverter and AMXE motors to boost power.
The mine truck is equipped with a trolley pantograph connected to an overhead catenary line, ideal for long haul ramps.
The electric trolley line aids the battery-electric mine truck on demanding up-ramp sections while fully loaded, extending its reach and enabling battery regeneration during drift. This significantly increases a mining operation’s productivity.
ABB was responsible for creating the infrastructure from grid to wheel, including the design of the electric trolley system and the rectifier substation for the test track. The standards and vehicle interface were developed jointly by the project partners.
This project is supported by funding from Swedish innovation agency Vinnova.
Boliden plans to implement a full-scale, autonomous electric-trolley system in the Rävliden mine, an extension of the Kristineberg mine.
It has placed an order for four Minetruck MT42 SG Trolley trucks from Epiroc for a total distance of 5km at a depth of 750m.
The partners in this initiative are working to demonstrate that the underground working environment can be significantly improved with fewer emissions, noise and vibration, while also reducing the total cost per tonne.
Last year, Epiroc and Byrnecut joined forces to develop future electric drive underground loaders.