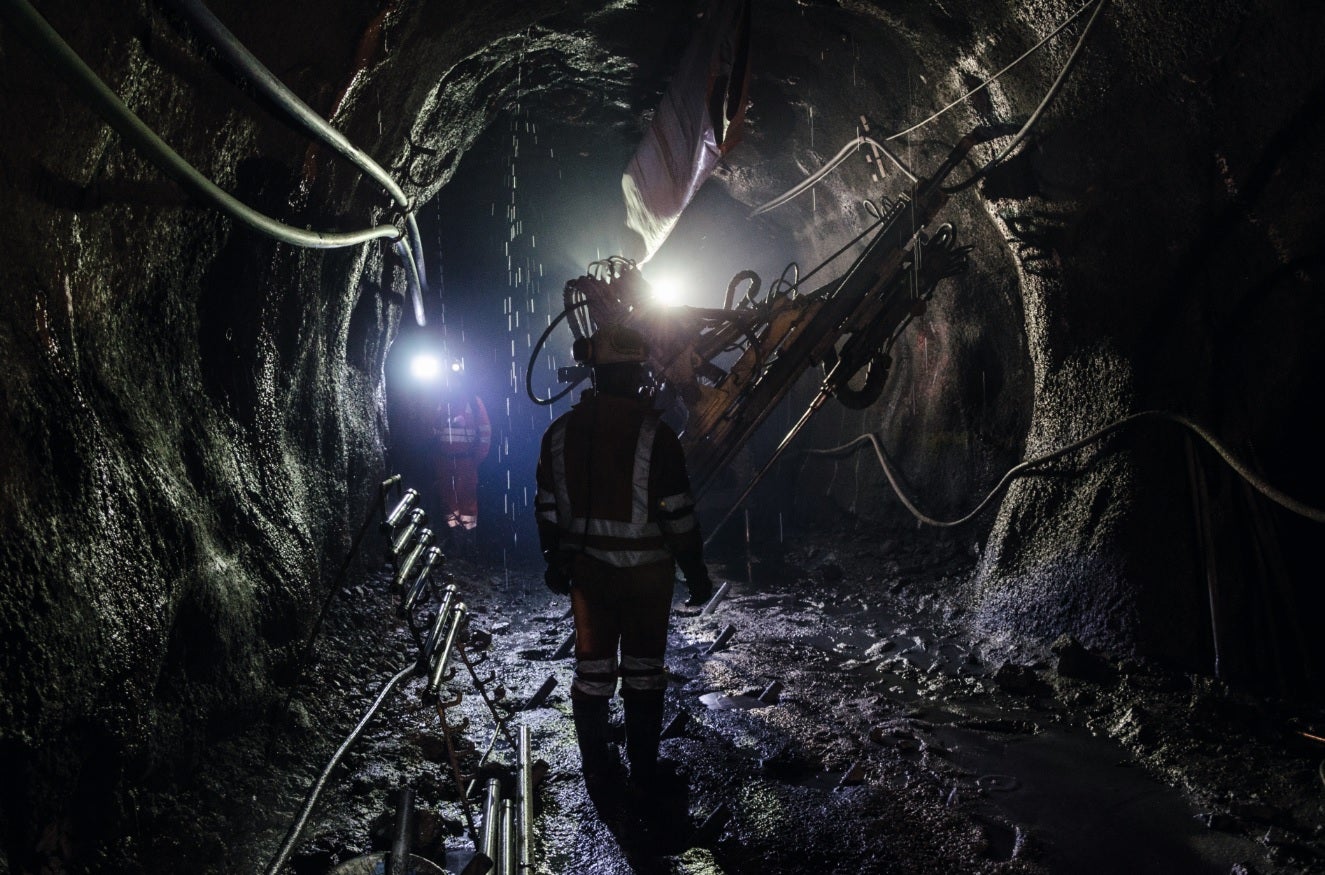
Mines are, historically and currently, a uniquely harsh environment for both people and machines to operate in. Indeed, it is these severe conditions that have typically prevented certain technological advancements from being brought into the sector’s sites, given the necessity for specialised, hardy equipment. Yet as we see a global shift to a more connected, digitally-driven sector, such tools are being brought into the mines to streamline operations and create the ‘smart mines’ of the future.
Fiber optics is just one of the solutions being introduced to increase efficiency, safety, and environmental impact at these sites. While traditionally these cables were too delicate for use in mines, specialised fiber optic solutions are beginning to gain momentum in the industry, and HUBER + SUHNER’s toolbox shows the demonstrable benefits of harnessing this technology correctly.
A smart solution
A study by Allied Market Research projected a growth rate of 14.9% for smart mining by 2022, an increase that was anticipated to be driven by stakeholder demand for better safety, productivity, and financial gain. Speaking with Thomas Paul, head of market unit industry at HUBER+SUHNER, he says that fiber optics are a crucial part of getting to this new, smart way of mining.
“Fiber optic usage in mining is proliferating rapidly, in fact it is becoming state-of-the-art,” he says. “The success in mining also helps to foster confidence in fiber optic’s applicability to other harsh environment applications.”
While fiber optics were known to work effectively in the industrial sector, finding ways to safeguard the technology against the impacts of mining’s somewhat inhospitable sites was crucial in transferring its use to the world of mining.
“Mining is probably the toughest environment any industrial equipment can be exposed to, and the barrier to entry was high for fiber optics,” Paul adds. “We were able to transfer many learnings from our other work however, as we have lots of experience in adjacent industrial applications such as railway, defense, oil and gas, etc. Working with our Australian partner Ampcontrol, a very successful and renowned player in mine electrification, also brought in detailed application knowledge and pivotal ideas for network requirements.”
Once installed, fiber optics can allow for the transfer of vast amounts of data across a site. Among other things, this can enable companies to more intricately understand the land being mined and thus adapt operations to not only be more efficient, but also more environmentally sustainable.
“Mines need to convey ever larger streams of data in their effort to push automation and to make mines more productive, safer, and reduce their impact on the environment,” says Paul. “This is only possible with fiber optics, but the harsh environment means conventional fiber optic cables, connectors, and accessories cannot be used. Operations need special connectors: they must be resilient to contamination and handling, must be easy to clean, and must be easily connected and disconnected.”
In addition, Paul adds that miners are often not trained to deal specifically with fiber optics, and so cannot take special care with equipment such as this. As such, the more delicate tasks such as splicing or connecting wires and connectors cannot be carried out by miners. This, Paul says, is where HUBER+SUHNER’s toolbox comes in.
Case in point: reducing downtime
Network flexibility is also a typical issue in this industry, given mines’ dynamic nature. Single core cables don’t, therefore, work for these sites, and again this is what HUBER+SUHNER seeks to remedy, offering 4, 12, and 24-core cables as well as the accompanying connectors and distribution units. This technology was harnessed for a Australian gold and copper mine that needed a fast solution when a cable snapped.
“That’s an example where downtime could be dramatically reduced following a cable outage,” Paul says. “Standstill of production in mining has rapidly inflating financial impacts – today, without data communication links, everything comes to a stop, so fiber optics sit very much at the center of operational reliability.”
Instances of cable breakage are, Paul says, a typical moment where these fortified fiber optic cables can really make a difference to a mining company’s operation.
“Fixing a fiber optic cable has no similarity to fixing an electrical cable – it’s much more complex and delicate,” he says. “Usually when this happens the mining company will bring in an expert or order a replacement cable, which needs to be exactly the right dimensions. In our solution, we have our toolbox of standard assemblies that can be stockpiled easily, and the network can be designed to use a small variety. Thus a cable is rapidly fixed by replacement from stock without any hassle.”
When asked about what else will be making a difference in creating the mines of our future, Paul says wireless communications and remote or autonomous operations will have a huge impact on the industry – something that in itself will rely on fiber optics for effective deployment throughout the sector.
“We’re already starting to see 4G/LTE and 5G networks be deployed in mines around the world, with several pilots also ongoing,” he says. “All of that needs backhaul through fiber optics, again because data volumes are just exploding. So that trend is giving additional momentum to fiber optics in mining.”
It seems the fiber optic revolution is already well underway, and will serve as a crucial piece in the establishment of more connected, efficient mines.