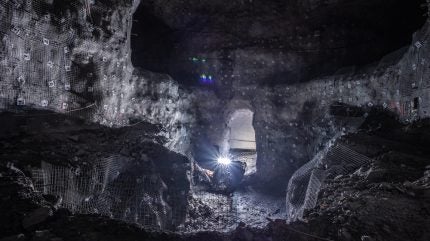
With demand for critical minerals expected to quadruple by 2040, surface ore deposits are being depleted at a rapid pace. In response, miners are venturing further into the earth to fulfil natural resource supplies.
In recent years, major mining companies such as De Beers and Rio Tinto have invested billions to extend the life of mines with dwindling production by moving operations deeper underground.
Less than ten mines in the world have reached 3km and only Harmony Gold’s Mponeng mine in South Africa has a record operating depth of 4km.
Along with financial returns and market fluctuations, the trend towards underground mining is influenced by developments in equipment. More physical and digital solutions are being commercialised to enable the detection and extraction of deep deposits.
Digitally connected hardware can gather spatial data of underground terrain, with communication networks supported by 5G technology for constant analysis and monitoring.
To enable the transition towards ultra-deep mining, research finds that “interdisciplinary innovation, experimentation and leveraging modern tools” are key for the advanced and fully equipped underground mine.
Traversing deep mines
Mobile equipment such as vehicles and robots is crucial to expansion programmes in underground mines and automation has become a mainstay in the sector.
Able to operate around the clock in extreme underground environments, mobile tools can perform automated drilling, installation support in tunnels, debris removal and ore transportation.
For drilling at increased depths, robotic continuous cutting methods pave the way for vehicle access. A range of companies including Boliden, Theiss and Sandvik are piloting advancements across drilling cycles.
Stantec vice-president of mining Steve Rusk highlights the important relationship between operators and original equipment manufacturers in spurring innovation. “They continuously work together on testing and applying equipment in underground mines. It is a symbiosis that can be slow to act because it is need-based, but it drives opportunity.”
For increased efficiency, analysis from the University of Sweden outlines how mining has firmly moved away from line-of-sight remote control — which is unproductive, slow and unsafe due to “the constant change between manual and remote operation” — towards tele-remote control.
However, as underground mining expands, challenges around safely and efficiently combining modern equipment with existing fleets have emerged.
South Africa’s Council for Scientific and Industrial Research (CSIR) chief mining engineer Theunis Otto tells Mining Technology: “One of the major challenges in many of our underground mining operations is developing a hybrid model that enables seamless interaction between driver-operated vehicles and autonomous vehicles.”
The organisation is developing collision prevention systems so equipment can stop automatically in emergencies, a solution which would bolster the already healthy underground mining vehicle market.
According to Mining Technology’s parent company, GlobalData, the total number of vehicles at active underground mines globally is forecast to rise from 19,718 in 2023 to 21,604 by 2030 at a compound annual growth rate of 1.3%.
The robotics industry is similarly robust, with a predicted value of $218bn by 2030, offering a boon to underground mine productivity.
Transporting physical equipment
To efficiently deliver physical equipment over lengthy vertical haulage distances, advanced hoisting systems are essential.
For shafts of up to 2km, friction hoists powered by electricity are used with multiple ropes but beyond this rope life becomes an impediment. At a depth of 3km or more, blair multi-rope hoists are needed for conveyance.
ABB global sales manager for hoisting Tim Gartner highlights the rapid advancement of hoists. “In 2005, we thought that a mine hoist would plateau at a 6m diameter with six ropes, but we were already delivering this in 2010. The advancement has been very fast and that is fundamentally a result of more companies wanting to get more ore out of the ground as quickly as they can.”
In early December, BHP made a major investment in hoisting systems for its Jansen Potash project in Canada, which features two 1km deep shafts. One of the hoists is reported to be the world’s largest by production capacity, capable of transporting payloads of 75 tonnes.
“The challenge with going deeper is not the hoist mechanics or the electrics. You can make them as big as they need to be,” Gartner says. “Once you start getting beyond 3.3km, the weight of the rope itself that is suspended in the shaft starts to become a significant proportion of the payload.”
Gartner asserts that if rope technology is developed to weigh less with hybrid or composite material “then we can start exploiting some of these deeper ore bodies. There is no question the rope is the limiting factor.”
Digital mapping underground
In the dynamic geotechnical environment of deep mines, physical equipment would be ineffective without the real-time connectivity and data provided by advanced software.
Otto confirms that “just implementing equipment in a mine doesn’t stick or add value unless you take a systems approach and look at the adoption and integration of technology. It should be about allocating resources where it is necessary.”
He identifies spatial mapping as a “foundational enabler” for deep mining, pointing to laser and radar scanning as key digital tools. Attached to robotic equipment, sensors and scanners provide detailed and accurate 3D representations of underground spaces that are undetectable to normal cameras. A popular mapping technology is LiDAR (light detection and ranging) for calculating volumes of ore piles.
Once a 3D model is produced with real-time data on geological conditions, operators can plan excavation routes for vehicles and robots while using AI to monitor and predict shaft stability or potential hazards across thousands of metres.
Speaking to Mining Technology at Resourcing Tomorrow, ABB vice-president of mining Max Luedtke emphasised the importance of digital data collection. “Even if there isn’t an immediately clear picture of how the data will be used, with AI and machine learning coming in you can build patterns. This is important for an industry with small margins on critical time scales.”
Underground 3D mapping equipment is rapidly becoming an active investment area. In the final quarter of 2024 alone, Rio Tinto and Gold Fields announced separate deals with Fleet Space, an Australian provider of smart seismic sensors with 3D Ambient Noise Tomography data that reaches 2.5–4km underground for mineral exploration.
“If you don’t have that background information of where the assets are in an underground mine, it becomes challenging to track equipment performance in terms of safety and productivity across different areas,” confirms Otto.
Underground connectivity
For comprehensive connection in today’s ultra-deep mines across core physical and digital equipment, 5G technology is crucial.
5G’s presence in mining is increasingly pervasive, with a predicted value of $12.75bn by 2029. Its high bandwidth and low latency offer a promising alternative to conventional optical fibre-wired networks, which have cabling that can be easily corroded in the underground environment.
Ericsson head of enterprise for Australia and New Zealand Ian Ross explains how 5G connectivity is delivered underground. “It is not as simple as putting a radio or antenna on a tower and covering kilometres of distance. We need to manage propagation of radio signals through complex networks of declines, drives and cuddies.”
Once implemented, data captured by scanners, sensors and cameras, including high-definition images and videos, can be transferred above-ground over a 5G network for analysis. The technology also enables the automation and remote control of robots and vehicles and detection of potential equipment failure.
Ross clarifies that safety and maintainability are reasons why “we don’t see a lot of public 5G coverage underground. Carriers are unable to cost-effectively deploy and manage extensions of their networks themselves. Mine operators proceed to invest in their own private 5G networks, so they have all the benefits but via an infrastructure that they own, operate and control.”
According to a report by Ericsson on connected mining, the applications that private cellular networks enable, including remote drilling, autonomous vehicles and real-time condition monitoring, offer a 256% return on investment in under ten years for an underground mine.
Descending into the future of underground mining
GlobalData’s 2024 Mine Site Technology Adoption Survey finds that underground operators have focused their investments on mine planning and scheduling software and communication networks. By 2026, they expect to prioritise predictive maintenance for mobile equipment.
Rusk concurs that mobile equipment is the most active area for development but highlights an issue with reactivity instead of proactivity. “Surface technology is much more advanced than underground. The higher costs and lower productivity of deep mining is typically not fertile ground for more capital investment.
“We have to get more ahead of the curve when we are going deeper but this isn’t pervasive in the underground mining business. Taking a purposeful look at deep mining will drive the next wave of equipment innovation.”
The interdisciplinary combination of physical and digital equipment is vital, says Otto. “Investing in hardware alone, without the corresponding software, won’t deliver maximum benefits. There is no one-size-fits-all solution for the industry – understanding the unique characteristics of an ore body and the existing mine design is crucial.”
As industry looks downwards to the next stage of deep underground mining, major investment in interconnected physical and digital equipment will be a key enabler to future-proof the extraction of critical minerals.