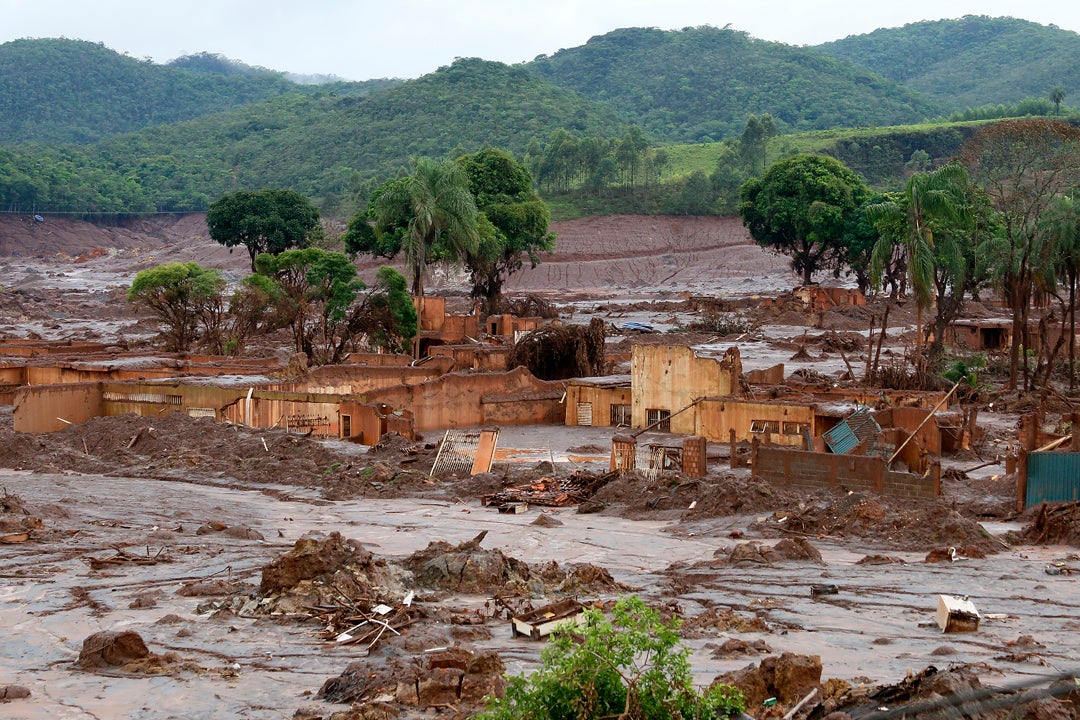
The reliability of tailings dams, used to store byproducts of mining operations after separating the ore from the gangue, has long been an industry issue.
According to the ‘Comprehensive review on reasons for tailings dam failures based on case history’, published in the Advances in Civil Engineering journal, on average, three of the world’s 3,500 tailings dams fail every year and the likelihood of tailings dam failure is several times higher than other conventional water-retaining dams.
With burst tailings dams often being highly toxic and potentially radioactive, companies are progressively turning to big data and digital intelligence to better understand and manage the most challenging task in the entire mining process.
Yoana Cholteeva (YC): What has prompted the need to monitor tailings dams closer than ever before?
Lyzandra Boshoff (LB): The mining industry’s focus on tailings dam safety has been spurred by a series of accidents in the past few years. The most recent one was the dramatic failure of the tailings dam at Vale’s Córrego do Feijão iron ore mine in Minas Gerais, Brazil, in early 2019, in which 250 people lost their lives.
A key challenge in the field of tailings dams is the engineering complexity of this infrastructure, due mainly to its dynamic nature and growth over time. Dam content changes continuously as the orebody and mineral processing parameters alter its chemical and structural composition.
YC: How does big data complement existing tailing monitoring techniques?
LB: Detailed data from tailings dams, when continuously gathered, analysed, and modelled, holds great potential for improving safety in tailings dam management. The data is particularly useful when it can give a real-time picture of changing conditions in tailings dams.
This demands that we harness technology in the way we collect, process, and interpret data. For instance, SRK has used automated vibrating wire piezometers (VWPs) to gather and communicate real-time data on tailings facilities. As importantly, we are developing visualisation capability, as well as interpretive tools to make this data meaningful to engineering decisions.
The work underway at SRK, with the specialised input of its data services department, is changing the landscape of data flow and interpretation. Significantly larger datasets can now be generated for analysis and decision-making.
By harnessing the power of big data, we can now test our assumptions and substantially raise the confidence of our observations. With the exponential growth in the application of technology in this field, more data is being generated and is available to be interpreted.
YC: Could you tell a bit more about SRK’s initiatives using automated vibrating wire piezometers on tailings facilities?
LB: Our use of VWPs has been valuable in providing the data on which we base real-time visualisation of changes in phreatic levels within a given monitoring area. This is important, as the seepage and associated pore pressure regime within a tailing facility is a vital aspect of the integrity and stability of the structure.
This has conventionally been tracked by manual standpipe piezometers whose performance, while accurate, depends on the quality of installation and aftercare – and manual data collection is subject to human error. However, this equipment currently remains useful as a back-up source of information while the reliability of VWP technology is gradually improved.
An important advance in VWP technology has been the improved wireless capability from many telemetry hardware developers. Cloud technology now allows data to be quickly uploaded and stored, for immediate access by engineers and management. These VWP networks are also useful when needing to confirm whether the mitigation measures in place are having the desired effect.
YC: What are the benefits of substituting manual labour with data technology when monitoring tailings dams?
LB: The real advantage of using VWPs is that we can generate much more data with less effort, and this can be digitally communicated to us in real time. A limitation of the traditional system was that the data may not reflect the prevailing conditions in the tailings dam by the time the information reaches the engineer for analysis.
YC: Could you tell me a bit more about the customised database and visualisation platform for VWP data that SRK is developing?
LB: Our pioneering work in rolling out automated VWP networks allows us to visualise cloud-based databases and analyse the information for better engineering decisions. This has required a number of technological innovations, including built-in, automated validation and interpretive tools to automate some of the routine engineering interpretive work.
However, any useful technological advance must still give the engineer the ability to apply judgement, and to consider all the factors relevant to each site’s unique geotechnical model. Each tailings dam needs its own piezometer network to be properly customised, and the evaluation approach must be based on the specific geotechnical model to ensure that all the right elements are tracked and controlled.
As the capability to process and interpret data from VWPs improves, the tracking of tailings dams promises to become a more exact science. The behaviour of the infrastructure can be observed continuously and in more detail, reducing the need to interpolate between the regular, but relatively static, snapshots of information.
This will contribute significantly to mines being able to manage tailings facilities more proactively and safely. It should be noted though, that observational methods employed by experts will continue to be vital in tailings dam management. Data assists mainly where changes cannot be readily observed from the surface.
YC: Are there any disadvantages?
LB: It is important to avoid the danger of becoming ‘lost in the data’ without adequate validation or assessment, which can only be achieved with high levels of engineering understanding. Such discernment from an experienced professional can ensure that anomalies do not occur and skew the data.
The data can only be understood in terms of the geotechnical framework in each case. We won’t get the right answers from the data if we don’t ask the right questions, or if the data is not correctly applied.
To effectively harness the power of technology, we need to marry two worlds – data analytics and engineering. Data analysts have the information technology skills, but not necessarily sufficient engineering insight. These two capabilities need to be adequately meshed if we are to realise the full benefits of big data in tailings management, and indeed other fields too.