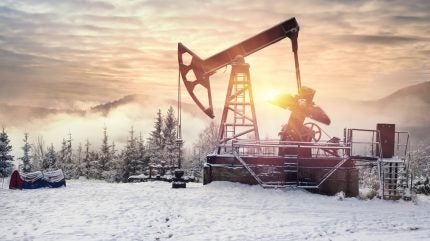
Remote mines are becoming increasingly exposed to extreme temperatures and weather patterns.
Climate change is at the root of this issue, with a report from the UN Office for Disaster Risk Reduction revealing that the number and severity of climate-related extreme weather events has risen by 83% from 1980–1999 to 2000–2019.
In 2025 and beyond, the World Meteorological Organisation (WMO) predicts an escalation in major floods, droughts and wildfires.
Whether in scorching deserts or arctic conditions, mining operations are highly vulnerable to climate change and erratic temperatures. So too is power infrastructure, leading to potential outages and operational disruption that miners cannot afford.
According to a report by the UN Environment Programme Finance Initiative: “Greater uncertainty in physical conditions will lead to decreased performance and reliability of power-producing assets, causing greater risks of downtime and blackouts.”
Miners isolated from centralised power systems are making efforts to diversify and hybridise on-site power sources as a defence against environmental disruption. Mining Technology looks at developing solutions and the interplay between mining, power and the climate.
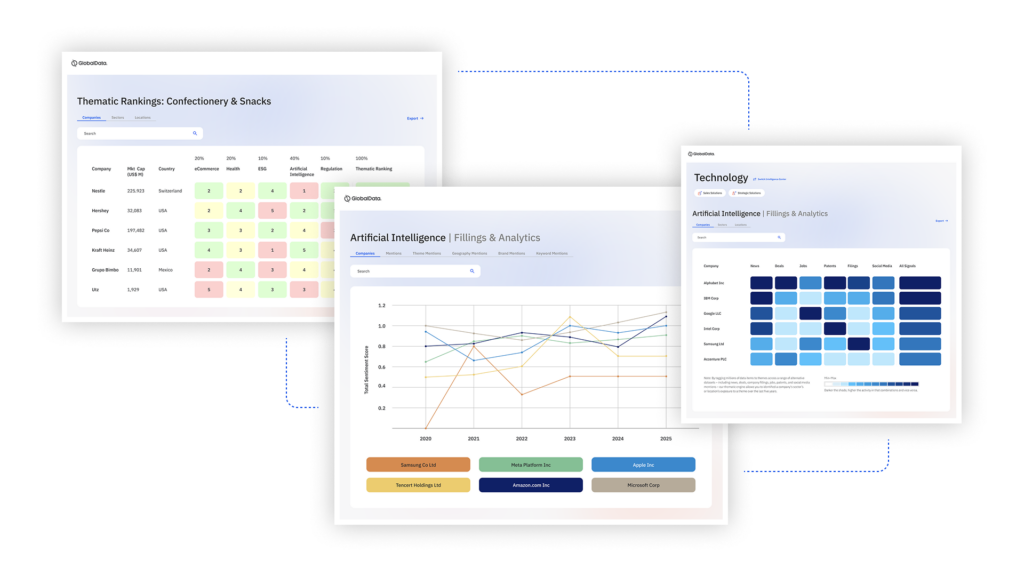
US Tariffs are shifting - will you react or anticipate?
Don’t let policy changes catch you off guard. Stay proactive with real-time data and expert analysis.
By GlobalDataThe impact of extreme climates on mining power supply
Valuable deposits of critical minerals are typically located in extreme climates, from metals in the Australian Outback where temperatures can reach 50°C to Canada’s mines with winter conditions dropping to -60°C.
Exposed to the elements, adverse temperatures and resulting weather events can cause havoc on surface mining operations and accompanying railways, roads and power infrastructure.
A major shutdown in 2023 saw more than 400 wildfires burn across Canada, affecting a range of mining companies including the Iron Ore Company of Canada (majority-owned by Rio Tinto) and Hecla Mining, as land access was prohibited and power line failures halted product transportation.
The power requirements for a mine can vary significantly depending on the mine size and type. The total load for daily surface mining operations ─ mostly from crushing and grinding operations ─ is estimated to be 1.5MW per 1,000 tonnes. This power requirement is complicated by fluctuating voltages, complex grounding and the daily operation of heavy machinery.
As well as this, remote mines typically operate on a fly-in, fly-out schedule with workers living in camps that require more energy to keep facilities and intense heaters or air-conditioners running.
The pressures of power demand continue to mount for mining companies and the consequences of failed supply in remote locations can expose workers to life-threatening temperatures on top of production and profit loss.
As such, the mining industry has come to look beyond dependence on individual and traditional solutions. There is an increasing awareness that connecting to centralised power is not a guarantee for stable energy supply, as national grids themselves are at high risk from temperature stressors.
Additionally, the historical dominance of traditional diesel generators in mining is developing as they become integrated with other power sources. In a hybrid system they can provide backup power if renewable energy falters, although they are also vulnerable to extreme temperatures.
Jordan Paquet, marketing and communications specialist at diesel, gas engine and generator manufacturer Bergen Engines explains: “In hot climates we must consider overheating, so equipment should have cooling systems to protect performance and lifespan. Diesel fuel can also degrade more quickly in the heat, which requires better monitoring to ensure efficient combustion.
“In cold climates, an issue is fuel viscosity. When temperatures drop, fuels can thicken, which creates problems with starting or reduced combustion efficiency.”
With variances in power source performance in different climates, modern remote mines are benefitting from hyper-local power supply, using a range of generation and transmission solutions to adapt to extreme temperatures as needed.
Power cable design for extreme temperatures
Power cables remain indispensable in mining and are the first step in establishing energy infrastructure. Companies such as Tratos Group, which serves international mining clients operating in some of the remotest locations on Earth, work to innovate cable materials and designs to meet temperature extremes.
“Freezing is more common than melting, as cables can typically resist a minimum of 70°C,” explains Paolo Bragagni, sales manager at Tratos.
Material is the main factor. “Most cables are made from rubber-like PVC (polyvinyl chloride), which at -40°C and below begins to harden and crack. Specialised natural rubber is a good investment for remote mines as it can [withstand] -60°C,” he continues.
Other materials with high thermal stability include fibre-glass, silicone or PTFE (polytetrafluoroethylene).
Bragagni adds that keeping cables from freezing can be achieved by maintaining a constant power supply. “Power produces warmth, so cables stay at approximately 25°C because of conductors. If you do not keep a cable running in cold conditions that is where problems start.”
Conversely, fires pose another major threat to cables. Mining operations are already at high risk of fires due to the abundance of materials that are flammable or can spontaneously combust, and this is only exacerbated by recurring wildfires.
“We make cables that resist up to 500°C, but in the event of a fire that lasts three hours or more, nothing can be done,” says Bragagni.
As well as increased fire risk, hotter climates bring environmental hazards to cables in the form of pests. “Australia has a major termite and rodent problem,” confirms Bagagni. “Depending on the material and severity of chewing by animals and if there aren’t any replacement cables in stock, an unprepared mine could be without power for 20 weeks as this is the minimum production time for new power cables.”
When all environmental factors are taken into consideration, specialised cables can manage extreme temperatures and reliably power heavy-duty equipment and a network of distributed energy resources.
Synergising mining power
Building a microgrid requires diverse investments to interconnect renewables, conventional power and storage systems to suit specific environments.
Research from Energy Strategy Reviews confirms that solar is the most popular renewable in mining but points out that “each type has its own advantages and drawbacks. The proposal of hybrid systems achieves a synergy of strengths among different technologies.”
In selecting energy types, strategic investment based on mining locations is key. For its operations in Pilbara, a region which receives the most hours of sunshine in Australia per day, Rio Tinto is investing $600m (£463.78m) to build two 100MW solar plants with 200 megawatt-hours from an on-grid battery energy storage system (BESS) by 2026.
Global mining market director Warren Smith from engineering company John Crane tells Mining Technology that he sees promise in hydrogen power as well as solar and BESS.
“We are definitely seeing the effects of climate change and major miners moving away from traditional sources of energy. Anglo American is already testing autonomous vehicles with hydrogen fuel cells and I am hoping that there is a bigger uptake of this in the industry. The volume would require hydrogen production sites, either close to a mine or on-site in a containerised format.”
Hydrogen power is especially effective in withstanding extreme climates. Research by Cleveland State University finds that hydrogen fuel cells outperform battery-electric vehicles under severe temperature conditions, holding promise for long-range performance in remote mines.
Liquified natural gas is emerging as another alternative to higher-emission fossil fuels used to keep mining operations and workers warm in cold climates. According to a case study by industrial energy solutions provider Aggreko, a “virtual LNG pipeline” was built to power five 1.3MW generators at a remote silver mine in British Columbia and withstand winter temperatures of -55°C.
The possibilities for miners to hybridise power sources within a microgrid are numerous. In Western Australia, industry giant Gold Fields operates several leading examples of what can be achieved.
Paquet emphasises the supporting role of generator sets (gensets) that combine generators and engines. “When renewable energy is available it can handle most of the load, but when conditions change through natural events, low-emission gensets can take over within minutes.
“Hybrid systems are known for their flexibility, so that is why we believe they are so important for the mining industry.”
Future-proofing power in mining
The complicated cycle of mining’s relationship to climate change means that it simultaneously makes a significant contribution to greenhouse gas emissions but is also impacted in turn by resulting temperature shifts.
When strategising cleaner energy systems and considering investments in different technologies, mining companies must consider long-term climate forecasts in operating regions, alongside the life cycle of a mine.
Paquet acknowledges that many mine operators are cautious about the transition to more sustainable power solutions. However, he adds that “as weather events are becoming more frequent, hybrid renewable microgrids are a great option because they are designed to be resilient to sudden changes”.
With mines now having to factor in the impact of a changing climate on mine operations, ensuring power solutions are robust in extreme temperatures is key.
“As it evolves, the industry is now talking about reliability, which it never did in the past,” concludes Smith. “Energy saving is very important and that comes through utilising a range of advanced technologies.”