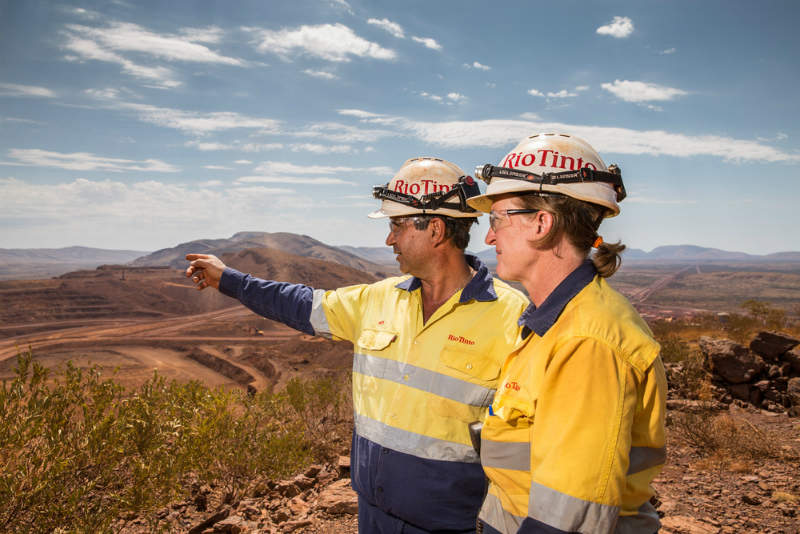
In 2008, Rio Tinto launched its ‘Mine of the Future’ project. Envisaging a near-future where human miners and robots worked side-by-side to extract minerals more efficiently, safely and sustainably, the Anglo-Australian multinational took the then radical step of automating its iron ore rolling stock.
A decade later, driverless trains, trucks and drones are commonplace in the remote Pilbara region in Western Australia’s north-west. Rio Tinto monitors operations there from 1,500km away in Perth.
Similarly, experts in the company’s processing excellence centre in Brisbane, Queensland, analyse real-time data to optimise mineral processing at seven sites across Australia, the US and Mongolia.
The internet of things (IoT) and Big Data are now used to automate machinery operation, enhance safety, facilitate predictive maintenance and improve traceability and environmental monitoring.
But while mining operators in Western Australia have switched on to automation, they have yet to address the state’s yawning digital skills gap through meaningful investment in tertiary education.
Once again, Rio Tinto is leading the way, investing $2m in a vocational education and training (VET) initiative to prepare potential and existing workers for advances in technology and innovation.
“We are generating opportunities for our current and future workforce to gain skills and competencies for smart mining,” said Rio’s iron ore chief executive Chris Salisbury. “The new curriculum will enhance the capability of those in the mining sector and form part of the learning pathways for those seeking to enter a range of industries applying automation and technology.
“By working with South Metropolitan TAFE and the state government, we will deliver the courses that will prepare young West Australians for the jobs of the future.”
The digital mine: what skills do miners of the future require?
The new modular courses, designed to upskill workers in key areas such as analytics, robotics and IT, will offer the first specific qualification in mining in the 200-year history of the industry in Australia.
“Where the gap was was in an accredited, highly qualified, high quality, transferable course that companies then can build on,” explained Rio Tinto’s head of human resources Nicky Firth.
“It is also relevant for other industries like maritime, health care, logistics, police, airline and the defence sector,” she told ABC. “It will fill a gap in the workforce and complement our apprenticeship programme. We have employed 600 apprentices in six years and there is another intake underway right now for another 40 apprentices.”
In addition to apprentices, Rio Tinto has employed close to 650 graduates, and will recruit a further 160, plus new vacation students, apprentices and trainees in Western Australia throughout 2018.
The VET curriculum, which includes a high school pathway programme, is due be completed by the end of 2018, and delivered through new industry traineeships and post-secondary courses by 2019.
“The demand for people educated in the areas of science, technology, engineering and mathematics will continue to grow,” said Salisbury. “I invite my industry partners, who are also investing in automation technology, to join us in this collaborative education initiative as the state economy continues to diversify.”
Human capital: investment in people and technology
The digital skills gap has not only highlighted shortcomings in the TAFE curriculum – Salisbury points out that some courses have not changed in 20 years – but also the degree to which market volatility, increased cost base and the scarcity of resources has transformed the mining industry in Australia.
“We’re looking forward and what we see is the surface mine deposits will be depleted,” Stuart Tonkin, CEO of Northern Star Resources, one of the country’s largest gold mining firms, told ABC.
“The industry has already moved from 75% of the mines being open-cut to now only 56%. And with the push to remove diesel trucks from underground and move to autonomous electric vehicles, we need to be preparing for that future.”
Northern Star is investing $50m over ten years to train a workforce with the requisite digital skills in the belief that people, not technology, are still mining’s most valuable and oft-underrated resource.
“As soon as you move to those electric vehicles, there’s a whole different skill set in trades that need to be involved in keeping that gear running, like diagnostics” said Tonkin. “Everything in industry is driven by people, so we’re investing in people, and the skills, and recognising what skills they will require in the next two decades. We need to start training them now because it does take time.”
“There’s no point displacing labour,” he continues. “You need the same labour and there is a shortage of labour, a shortage of people who are interested in going into underground mining.
“So just the sheer education and getting people excited about it is part of this whole programme we’ve embarked on.”
School of thought: attracting and retaining talent
Like the oil and gas sector, mining is waking up to the idea that in order to retain top talent and attract the next generation of young, environmentally aware, tech-savvy employees, the industry must market itself as switched-on, forward-thinking and progressive – and that starts in the classroom.
“I think we’ve got two challenges,” said Mining Education Australia director Steve Hall. “We need to compete with the Ubers and the Goggles of the world and attract the IT, the mechatronics, the robotics people and get them to look at mining, and get involved in it.
“But we’ve also got to get the mining people to understand what’s really going on in those same disciplines; it’s got to come at it both ways.”
The Business Council of Australia (BCA) has also waded into the debate, proposing a single tertiary funding system across higher education and vocational training. The BCA claims that to prevent workers slipping through the cracks and to make vocational courses more attractive to students.
“Industry employees [make up] ten million of our working population of 12 million, and it understands what’s needed as it’s already dealing with disruption and transition across markets,” said BCA CEO Jennifer Westacott. “This is urgent and state governments need to act on this immediately.
“We’re having a national debate about foreign workers [when] what we should be doing is debating the skilling up of our own workers.”