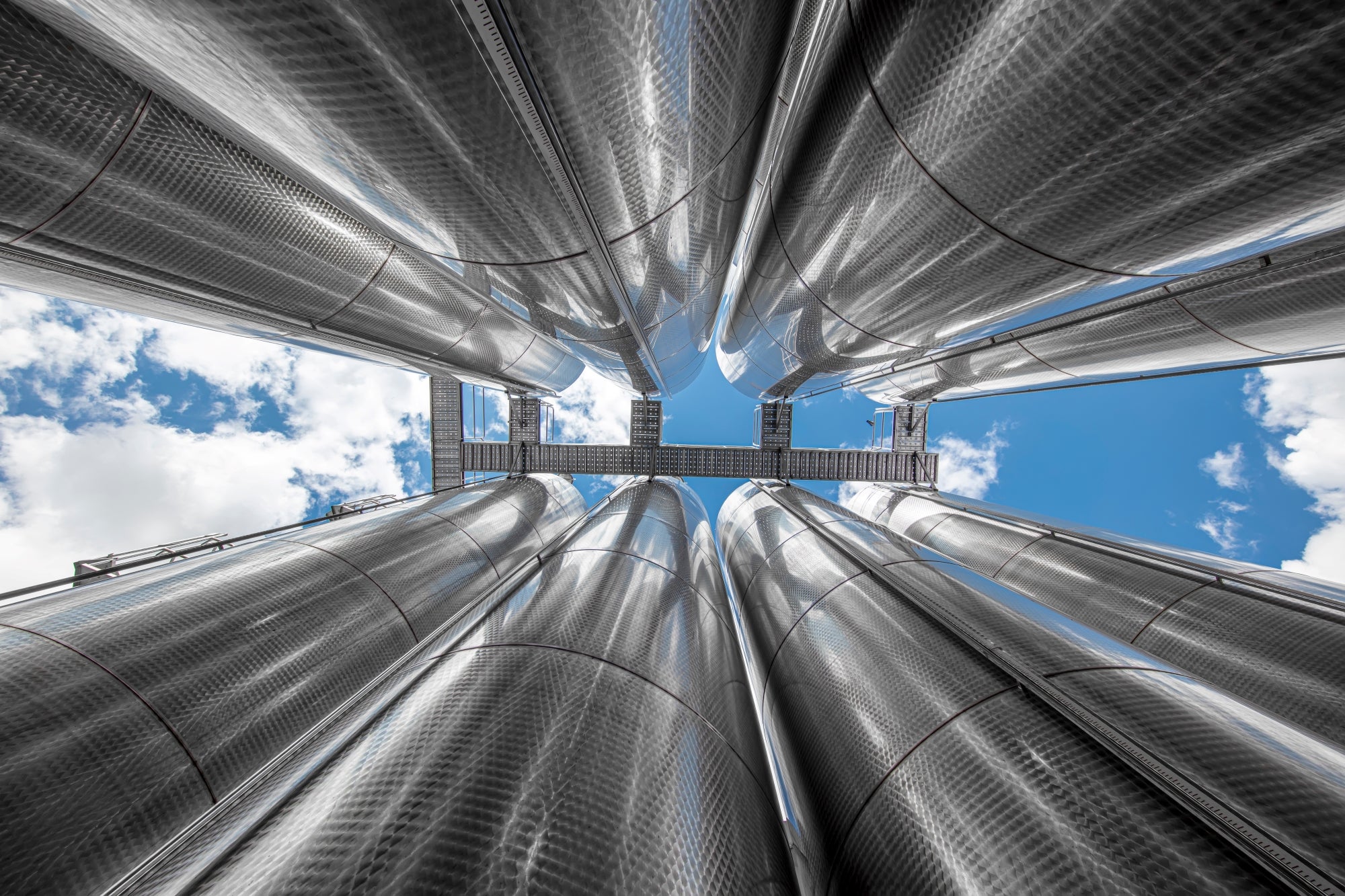
Steel production releases more emissions than any other industry, with the sector responsible for 9% of global carbon dioxide emissions. But the industry is changing with new, so-called “green steel” plants due to begin production in 2025.
According to the International Energy Agency, if 2050 emissions targets are to be met then the steel industry must cut emissions by 50%. As one of the oldest manufacturing industries globally, change has been slow but interest in green steel production is growing as producers seek alternatives for resource-intensive methods.
The EU increased the number of planned green steel projects to 38 in 2023, up from 23 in 2021. Additionally, Germany alone has invested $9.1bn (€8.5bn) into the decarbonisation of its steel industry, clear steps towards a more environmentally responsible form of production, and moves that could be the first significant steps in truly decarbonising steel production.
Decarbonising operations
Steel decarbonisation could be a viable process, as the production of steel relies on a number of processes, all of which are moving away from carbon-intensive forms of production. Typically, steel is produced by reducing iron ore in a blast furnace which is heated to temperatures of over 1,000⁰C. The burning of coal to reach these high temperatures is responsible for a significant proportion of the carbon dioxide emissions associated with steel production.
With a number of European steel plants due to be relined in the coming years, a spokesperson from NGO Reclaim Finance says that: “the steel sector is at a turning point and decarbonising to reduce climate impacts must be an urgent priority. Getting it wrong would be fatal as it would mean the development of coal-based capacity, which, with a lifetime of around 20 years, would lock in emissions for decades”.
Conversely, one of the main methods of producing green steel is through the use of renewable hydrogen in the place of coal. While the method of using hydrogen to create green steel exists as an idea in principle, its use on an industrial scale remains to be seen.
When burned, hydrogen produces only water as a by-product; therefore if hydrogen is produced via electrolysis using only renewable electricity then it can be considered entirely green. When using an electric arc furnace hydrogen can be used to produce the same chemical reaction which occurs in in traditional steel making but with reduced emissions.
The EU outlines in its briefing on the potential for hydrogen to decarbonise the steel industry that the main barrier for large-scale green steel production is access to green hydrogen. Traditionally, steel production takes place in the same region that iron ore and coal are mined. However, new green steel developments are less bound by geography.
The report states: “With the transition to green hydrogen, the local availability of cheap renewable electricity, or the existence of transport facilities for hydrogen [such as] pipelines [and] port facilities will become important aspects of steel industry competitiveness”.
The briefing found that: “Producing the necessary amounts of hydrogen for a full decarbonisation of the steel industry would require an increase in electricity production of the order of 20%.”
Challenges of scale
However, while the technology is impressive, questions remain as to its efficacy on a large scale. Suzanne Schenk, head of grants and steel campaigner at Europe Beyond Coal, says that: “You would need so much renewable energy to create the amount of green hydrogen necessary for the steel industry that we can’t ramp up enough quickly”.
Schenk also notes that some companies are planning to use blue hydrogen, which is produced using natural gas and supported using carbon capture and storage, in the intermediary period.
“On the one hand it is positive to invest in the clean technology because we also can’t wait until all of the green hydrogen is available to invest in the clean technology, but it is a risk,” says Schenk. “You need a very clear moratorium or an end date for the use of fossil gas and a very clear road to procuring or producing the green hydrogen.”
One company which has committed to using exclusively green hydrogen is H2 Green Steel, which has started production on Europe’s first green steel plant in Boden Sweden. The company claims that the first batches of green steel will be rolled out in 2025. H2 Green Steel will use hydropower from the nearby river Lule to power the electrolysis process which will generate its own green hydrogen on site.
The company recently announced that it has entered into an agreement with Fortum to produce carbon-free electricity for its steel production. Rikard Dagerbäck, sales manager and strategic customer director for Fortum said of the agreement: “We believe that the complex nature of electrification and hydrogen projects at scale require cross-sectoral partnerships as well as large amounts of clean energy.”
Schenk was supportive of this fully-comprehensive approach stating that “there should be some sort of commitment or secured access to green hydrogen when launching such a project”.
Recycling steel
In recent years the phrase “green steel” has, for the most part, been used to refer to primary steel production using carbon-neutral methods. However, recycling steel is also a meaningful method of ‘greening’ steel production.
Recent global events, such as the war in Ukraine and the Covid-19 pandemic, have slowed demand for steel but it is nonetheless still increasing and set to rise by 2.2% in 2023. 75% of steel is still made in coal-fired blast furnaces, as production methods for steel are developed to incorporate more sustainable tactics, with the aim of making steel production 100% recyclable and highly recycled.
According to the Galvanisers Association, 40% of all steel production is based on recycled scrap. In the UK 87% of construction steel is recycled. Recycling steel is much less resource intensive than primary steel production. According to Schenk: “The difference in carbon dioxide emissions in producing steel and recycling steel are hugely different […] because you don’t need the same level of heat”.
But in many countries well established systems for steel recycling do not yet exist. Schenk explains that much of the scrap steel collected in Europe is contaminated with dirt or rust and is exported overseas an “downcycled” into a lower-grade product. She claims that this “huge untapped potential” is key to ensuring a continued global supply of steel.
She adds that: “While green hydrogen-based steelmaking will be part of the solution, it’s highly expensive and the required green hydrogen is unlikely to be produced in large enough quantities in time. Policymakers and businesses should therefore focus more on high-grade steel recycling and circular solutions to ensure we produce green steel at the speed and scale we need”.
“The hydrogen buzz”
A number of industry heavyweights including ArcelorMittal, Nippon, POSCO and Baowu have announced green steel projects due to come online in the coming years, aligned with 2050 zero emissions targets. Hydrogen is cited as the principal means of achieving greener steel.
According to Schenk: “When people hear ‘green steel’ they think only about the primary, and that’s also what the companies are really pushing, but I think that is one of the biggest missing pieces in the public space”. She attributes a lot of these announcements to “the hydrogen buzz” as companies set their sights on the latest in carbon neutral trends.
Grand View Research found that the global hydrogen creation market size was valued at $55.35bn in 2022 and is expected to expand at a combined annual growth rate of 9.3% from 2023 to 2030. Interest in hydrogen is growing as various industries consider how to decarbonise their processes.
But in the steel industry, for many of the proposed projects the realistic plans of how sufficient quantities of green hydrogen will be supplied remains the key missing piece as it negotiates how it will reduce its carbon footprint.