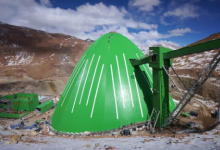
One grows and maintains picturesque vineyards to produce fine Chilean wine enjoyed the world over; the other scours the earth to dig up valuable gold, silver and copper. Though wildly different, the Chilean winemaking and mining industries are paramount to the country’s $320.5bn (GDP) economy and must co-exist alongside one another.
Once at loggerheads due to the amount of dust from mines polluting vineyards, the two industries are now able to co-exist, thanks to engineers at dome-designing company Geometrica, creators of standard and bespoke domes capable of shutting in the dust.
Most mines in Chile located in winemaking regions now have some sort of Geometrica dome or ‘freedome’ to ensure winemaking neighbours aren’t left with vineyards and water supplies that are covered in dirty mine dust.
Geometrica’s Chile representative Juan Pablo Jijena speaks about the challenges of designing and constructing the dome structures in the arid Atacama Desert and lofty Chilean Andes.
Heidi Vella-Starr: Please tell us a little bit about the ‘freedome’ Geometrica designed for the desert-based Carola Mine.
Juan Pablo Jijena: Carola mine plant is very old and has grown organically over time. It is located in a fertile valley in a region of the Atacama Desert in northern Chile. This valley is very prolific in vineyards and the mining plant is located precisely in the midst of a vast area of vineyards that are permanently contaminated with dust emanating from the production process of the mining plant, resulting in constant claims from farmers in the affected area.
By mid-2010, the Carola mine contacted us to evaluate an overall solution for the problem of pollution emanating from the plant. We identified three highly polluting plants on the ground; these we covered with bullet circular domes and a central, irregular shaped area was covered by the freedome.
In addition to permanently solving the problem of pollution at a lower cost with a highly aesthetic product, our freedome was built without stopping the operation of the plant, which undoubtedly was a significant advantage over other alternatives.
The project began in 2011 and engineering and design took around three months and construction about eight months.
HV: What were the main challenges of the project?
JP: Undoubtedly the greatest challenge was in the design and engineering. Several long studies found different alternatives suitable to cover the selected space, but there were many issues to fight against when the freedome was being built; such as the limited space on the ground, as the freedome needed to rise up from the floor.
HV: What was the cost of the freedome at the Carola mine?
JP: Regarding value, I cannot disclose the cost of the agreements we made to our customer. However, it is a solution with an excellent cost benefit ratio, and has been implemented in virtually all Chilean mines.
HV: The dome was constructed by local labour. How easy was it to train local tradesmen and did they need much supervision?
JP: Indeed the freedome was built with local labour, with the continued assistance from a geometrical engineer and with a strict adherence to our procedures and plans of assembling, which were prepared for the environmental conditions and resources available for this particular work.
HV: Were there any major construction challenges?
JP: There were several challenges to overcome to achieve the construction of the freedome. First, the plant continued to operate while the dome was assembled, which meant a very hostile environment for workers, mainly dust in suspension. Given the large number of projects carried out in the region there was very little available labour, so it was very difficult to get workers. Since there were several significant interferences with existing structures, it was necessary to have large steel frames to support the dome, which were mounted by cranes with very little room to manoeuvre.
HV: Regarding the Minera Lumina Copper Chile in the Chilean Andes, what were the main challenges of this project?
JP: Indeed Geometric has built several domes in the Andes, and in particular the mining dome at Caserones was 4000 meters above sea level, which was a major challenge, primarily because of its size and diameter – it is 143 by 90m high. It was a challenge also because of the environmental conditions, such as frequent snow, extreme cold, high winds, adverse topography, and difficult access and reduced working space. There were also inadequate occupational health conditions due to low oxygen in the air, which strongly hindered the performance of workers. The dome was required to cover the stack of thick copper ore.
HV: How long did this dome take to construct?
JP: The construction of the dome took around twelve months and was assembled by a local contractor, assisted by a team of engineers from Geometric.
HV: In general, do the domes require special ventilation for workers?
JP: Ventilation is generally not required because workers enter the dome only when the stockpile is not running or for very short inspections. Ventilation would allow the dust to clear out of the dome and pollute the environment.
HV: What is the maintenance requirement and lifespan of a dome?
JP: Domes are coated in galvanized steel and painted on both sides with polyester paint. They also have corrosion protection and are designed to greatly exceed the useful life of the project.
HV: What feedback has Geometrica received about the domes?
JP: Workers who have built our domes are highly motivated to work with a unique structural system that is modern and much admired. In general our customers are very pleased, not only by the results but also by the way we carry out the various stages of the project, from engineering, manufacturing, assembly and support. We are a boutique industry strongly oriented to our customers