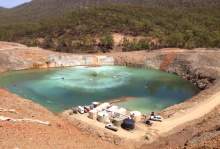
Current methods of treating the huge amounts of acidic, metal-heavy wastewater generated by the Australian mining industry every year are costly and time-consuming. But a new technology developed by Australia’s national science agency CSIRO, which actually uses the contaminants within the water to treat it and is fast gaining momentum, is not only cheaper and quicker than conventional methods, but it’s also much more environmentally sound.
Wastewater is a big issue for Australia’s fast-growing mining industry. It’s estimated that millions of tonnes of wastewater, which often contains substantial concentrations of metals such as magnesium and aluminium, are generated each year by more than 400 mines currently operating in the country. On top of that, there are around 50,000 abandoned mines in Australia with water issues of their own; in New South Wales alone the 500 derelict mines have resulted in thousands of hectares of contaminated land, affecting farming and aquatic ecosystems.
Mining wastewater generally contains a large range of different contaminants and the current techniques used to treat it – most commonly the addition of lime – result in the formation of a large volume of sludge, which is difficult to deal with as it either needs to be further treated to extract the contained water or be disposed of, something which requires significant amounts of space.
Now, a new technology, developed by CSIRO scientist Dr Grant Douglas, is addressing these issues more effectively than ever before. And it’s surprisingly simple. Dubbed Virtual Curtain and developed almost by accident when Douglas was working on some contaminated groundwater seven or eight years ago, the system essentially uses the contaminants already present within the wastewater to purify it, reducing the amount of sludge formed by up to 90% and eliminating many of the challenges associated with lime-based treatment methods.
Using what’s already there
"What we do is firstly look at the composition of the mining wastewater, and then creatively use some of the contaminants that are already present to our advantage," Douglas explains.
The history of mining in the Kingdom of Saudi Arabia stretches back thousands of years.
The concentration of these contaminants is tweaked, then alkaline compounds are added to increase the water’s pH level and a mineral called a hydrotalcite is formed, which can simultaneously trap a variety of contaminants including arsenic, cadmium and iron in one simple step, something conventional waste management technologies simply can’t achieve. The contaminants can then be easily removed from the wastewater as a solid.
And the technology really does work; it was used for the first time at a commercial mine in Queensland earlier this year and discharged the equivalent of around 20 Olympic swimming pools of rainwater quality water. This is just one of many trials that are currently underway in Australia.
High quality, low cost
Says Douglas, Virtual Curtain is both much more cost-effective and environmentally friendly than the limed-based methods currently favoured by mining operators. Firstly, as it uses contaminants already contained within the wastewater, expensive infrastructure and complicated chemistry are not needed. Secondly, the life cycle cost of the process is significantly lower. And finally, it results in the reuse of both the water and the contaminants.
"If you use lime, you often have to further treat the lime and remove a lot of the water from it – it doesn’t settle well in the mining pits," he notes. "Whereas with our technology, it often settles very rapidly and most of the water is immediately available for either reuse or discharge."
This is because the quality of the water produced is so high, something that is particularly important for mines in arid Australia or in other similar climates, Douglas emphasises. "You’ve only got very limited water at arid sites. So the more times you can recycle and reuse your water, the better."
The technology also produces a material high in metal value, which can be reprocessed to increase a miner’s overall recovery rate and partially offset treatment costs.
Global impact
Another key differentiator of Douglas’s technology is its versatility. "It works in both fresh and highly saline waters, and in water with low pH as well as very alkaline waters," Douglas says.
"It really covers the whole spectrum of water types and that’s one of its key points of difference. It’s very adaptable."
Indeed, in Douglas’s experience of working with mining operators so far, no two situations have been the same. "We’re always learning and implementing it in slightly different ways to suit a client or a particular type of water," he notes.
"They can be witches’ brews sometimes, but on pretty much every occasion we’ve been able to adapt the technology to suit that water type and remove the contaminants."
The potential of the technology is therefore enormous; simply treating the abandoned and operating mines in Australia will only be the beginning. "We have a number of trials with Australian mining companies and there is interest virtually every day or every other day, both locally and internationally, in the technology," Douglas remarks. "It’s really starting to build and gain some momentum, with at least two good prospects in Europe, interest in North and South America as well as interest from a number of other regions."
Emerging market companies are drastically outperforming their counterparts from the developed world.
Resistance to change
Douglas is remaining realistic, however, about how fast his solution is likely to be taken up across the sector. "The mining industry is often quite conservative so there is a reluctance to adopt new technologies," he admits.
"That’s been one of the barriers – many will continue to use lime because they’ve always used it and they know how it works, even if in many cases it’s a sub-optimal solution.
"All we can do is continue to complete lots of trials, as we did in Queensland with full scale mine pit treatment, and gradually engender confidence and knowledge and hopefully it will start to build on that basis. It’s a hard road, but you’ve got to start walking on it sometime!"