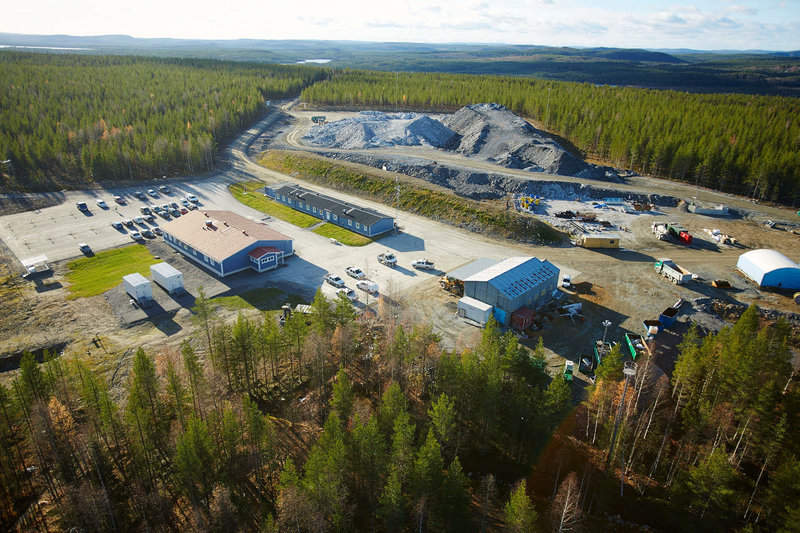
Swedish mine operator Boliden’s Kankberg gold mine is one of a kind. With help from telecommunications company Ericsson, along with partners ABB and Volvo, the mine has been completely automated as part of a pilot project overseen by Vinnova, a branch of the Swedish Government. The project, which began two and a half years ago, plans to eventually operate with no personnel in the mine itself.
As the world increasingly moves towards automation, the Kankberg mine is the most advanced example of efforts to digitise the mining industry. The mine has proven so successful at increasing safety and productivity that the project, which was due to finish in June, is continuing operations. A 5G network now connects every aspect of the Kankberg mine, including excavators and haulage systems, among other equipment.
While some are concerned about the effect automation will have on workers – as you need far fewer people to run an automated mine – others believe it is worth it. Removing personnel from such dangerous environments is certainly a positive when you consider that over the last year, mining has caused 63 deaths within International Council of Mining and Metals companies alone.
Automation has also been shown to increase productivity as mines can operate on a near 24/7 schedule, and reduce emissions and fuel consumption by as much as 15% through optimisation.
Creating an automated mine
The project’s origins lie with Ericsson and Vinnova. Ericsson approached Vinnova with the aim of conducting digitalisation projects, at which point the latter was able to suggest two pilots. The first was automation of manufacturing in Gothenberg, while the second was the Kankberg mine in Västerbotten.
Ericsson set about installing a 5G network throughout the mine in early 2016. “As it turned out, that worked extremely well,” says Ericsson research director, Torbjörn Lundahl. “We covered a path down to the mine area, we covered a mining area and we had 100 megabits in the whole mine.
“Also, where we had blind alleys and where we had caves without any line of sight to the antenna, we still maintained the high throughput and low latency on the network.”
Network reliability is very important, as a loss of signal, even for a few seconds, can cause major problems. The mine goes down to depths of 500m making connectivity a particularly technical challenge. The system is similar to that used to provide WiFi to underground train systems, such as the London Underground, but adapted to overcome rocks that can block the signal.
Following the introduction of Ericsson’s network different aspects of the mine could be automated, allowing another partner, ABB, to set about installing its SmartVentilation system. “Ventilation is a big thing in the mine and consumes a lot of energy,” says Lundahl. “A mine is consuming 36MW of energy in a year. That’s a lot, that’s a huge amount of energy!
“By having it all connected, automated and optimised, 54% can be saved. That’s a saving of 18MW a year of energy for that mining operator.”
In early 2017, the final objective of the pilot was reached as the machinery within the mine was also automated. “Volvo showed last spring that they could remotely operate an excavator down in the mine,” says Lundahl, “So, instead of being down in the mine, they could sit in a nice office environment with big screens.”
Time to prove the concept
The Kankberg mine faced a number of challenges, but Lundahl suggests it was the collaboration which caused initial concern. “The big thing was getting these big companies together,” he says. The technological challenges revolved around connectivity and speed of connection, both of which Ericsson is confident it has overcome.
“I know that previously there were problems with an excavator – it could not be loaded as much with remote controls or an autonomous machine as you can do with a man-operated machine,” says Lundahl. “So you are actually losing some of the productivity.
“But, I think this is more a matter of evolving and improving the computer programmes than a limitation of automation.”
As the mine moves into its extension period, the focus is changing. Ericsson is opening it up to other parties and small companies for innovation development. This will allow other groups to benefit from testing within an actual mine site and one that is complete with a 5G network.
“It has been extremely successful; it has been successful beyond all expectations,” says Lundahl. “When we first came in we had an objective to prove that our technology worked and that it can be very useful in these types of harsh environments.
“The mine is a good example of such an environment, meaning that if we can show applicability in that environment, then it will work in a number of other environments as well.”
Will automation become the mining standard?
Automation and digitalisation are being introduced globally throughout almost every major industry, with the benefits of increased safety and productivity plain to see. As mining takes place in hazardous environments, a clear trend towards reliance on digitalisation instead of staff has already begun.
“As we’ve seen in so many different areas in the mine, there are many things you can automate,” says Lundahl. “You can make machines turn on by communication; you can get machinery to cooperate down in the mine.”
However, despite the increase in safety, many are worried that as automation takes over, workers will be out of a job. “I think that this is a fear in all industries,” says Lundahl. “There are a number of reports on how many jobs you can actually replace by automation and the figures are typically up to about 50%.There are things that you cannot automate, but a lot of the work we do around us we could.”
“As soon as you have some improvement, some big change in an operation it always poses the question of jobs,” he continues. “You had it with steam, you had it with steel and you had it with fertiliser. But every time it has proven to create prosperity and a better working environment with better conditions for the people as a whole.
“Research from the US actually says that for every high-tech job that is created, you are creating five other jobs outside of tech, in different types of support services or other services needed in society.”
But this multiplier effect Lundahl refers to, and which is described in The New Geography of Jobs, by Enrico Moretti, takes time. Automation is also taking place at Rio Tinto’s Yandicoogina and Nammuldi mines in Pilbara, Australia, and Suncor’s oil sands in Alberta, Canada, and it’s happening fast, so a period of adjustment will be necessary.
“The world is going through a phase of change with automation, and there is a need to re-educate people and transform people from one skill to another,” says Lundahl. “On an intermediary basis, that could be very challenging and it will be a tough period to go through in many respects.”
“But as a society as a whole,” Lundahl adds, “I’m fully confident that this will just bring better things for society.”
It seems evident that automation will play an increasingly important role in mining, but there are still challenges to overcome before it truly becomes the norm. “I think for this to truly work in a mining environment there needs to be standardisation of how different machines talk to each other, how information is collected, how it is coded and the language your machine will use,” says Lundahl. “That could be a big hurdle, because there are typically different strategies from different suppliers, and some suppliers have already done some implementation. So, how you then bring standardisation in is probably going to be a big challenge to mining.”