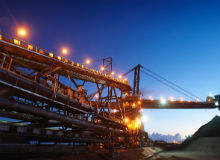
Situated in Australia’s largest coalfield – the Bowen Basin in Queensland – the Daunia Open Cut coal mine was opened in 2013 by BHP Billiton Mitsubishi Alliance (BMA), a 50:50 joint venture between BHP Billiton and Mitsubishi.
At the time, the 4.5 million tonnes per annum mine was one of the newest to open in Queensland, when mining jobs were being routinely shed due to the global commodities downturn. The mine created 900 new jobs during the construction phase, a further 450 people are used in its operation.
Now the staff at Daunia mine are breaking world records.
According to Advanced Initiating Systems (AIS), an Australian company that focuses on optimising blasting solutions in Australian mines, and BME, a leading supplier of explosives and services to the global mining industry and developer of the AXXIS digital detonation system, Daunia has broken two world records for mine blasting.
In 2015, the mine set a record for the largest AXXIS-controlled blast to date, when it successfully initiated 4,303 detonators in a single blast to break 2.8 million cubic metres of overburden.
At the beginning of this year, the mine set another record for the largest electronic detonator blast ever – firing 5,665 detonators in 2,683 blastholes using the AXXIS digital detonation system from BME.
"The record set initially last year was the largest AXXIS blast in terms of our own product," says Trevor Grant, managing director of AIS.
"This blast [the new record] is the largest global electronic detonator blast out of all manufacturers – I would go so far as to say it is the largest blast in terms of detonators ever initiated."
Grant says AIS confirmed this record with all manufacturers in an announcement at the International Society for Explosives Engineers in Las Vegas in January 2016.
Technology behind the blast
Drilling and blasting is the controlled use of explosives and other methods, such as gas pressure blasting pyrotechnics, to break rock for excavation. It is an essential part of the mining business, for both underground and open pit mining operations.
Blasting is typically done by a number of holes being drilled into the rock, which are then filled with explosives. Detonating the explosive causes the rock to collapse. Rubble is then removed and the new tunnel surface is reinforced.
BME’s AXXIS digital detonation system was selected for the Daunia mine in order to deal with its faulty ground conditions.
If not well controlled, faults tend to slide over each other during a blast; when using non-electric detonators, there is a possibility of the product being snapped by this movement of ground before it can be detonated, resulting in a misfire.
"These misfires are eliminated with electronics, as the detonator operates as a stand-alone entity the instant you push the ‘fire’ button," says Grant.
"The use of the AXXIS system and electronic detonators allowed the mine to better control and manage the shock waves and rock movement arising from the faulty ground conditions."
This risk of shock waves and misfires also increases as blast size increases. However, being able to undertake larger blasts can generate greater operational efficiencies by reducing the number of mine stoppages that must take place every time blasting is conducted.
"Electronic detonators do not suffer this risk and therefore provide a huge benefit to mining operations that want to blast large blasts and thus reduce the number of times a pit has to be closed for blasting," says BME technical director, Tony Rorke.
The average depth of each hole in the blast was 19 metres, and the explosive was initiated from both top and bottom.
"The improved control of the blast helps keep vibration levels down," says Rorke. "This in turn improves safety in the opencast mining environment, as high vibration levels can undermine the integrity of the pit wall."
Conducting the blast
Using a single initiation point and one master control box, Daunia staff conducted the blast after being trained for approximately three months by AIS, and following assessment and evaluation by BME for issue of manufacturer certification.
Enabling Duania staff to conduct the blast themselves "eliminates the need for costly technical support and other associated costs," says Grant.
This blast took approximately eight days to load and fire. This time was mostly spent on charging holes with explosives.
"The blast is primed normally by inserting boosters and electronic detonators into each hole," says Rorke.
"This is followed by the charging of bulk explosives into the holes. After each hole is charged, the detonators are electronically checked for functionality and allocated a firing time," he adds.
Masterminding the blast
To design the blast, the Daunia team used BME’s blast design software, BlastMap III.
The technology was launched in 2000 and has continually been developed since. The software works in conjunction with the AXXIS Initiation System.
According to BME, the program allows complex timing designs and analysis of the results for each blast, and has just been released in an updated, second-generation version.
Rorke says, in particular, the advantages of BlastMapIII Complex are that it is possible to time designs, which can then be downloaded directly to the detonators, thus ensuring that the designs carried out by explosives engineers are precisely executed.
"This has a huge advantage in eliminating timing application errors and therefore eliminates high costs for unexpected poor blast results caused by these errors," he adds.
"BlastMapIII also has advanced design features that allow for detailed hole positioning and charging thus enabling the modelling of blast results, complex large blasts designs and forecasting of vibration, fragmentation and burden relief."