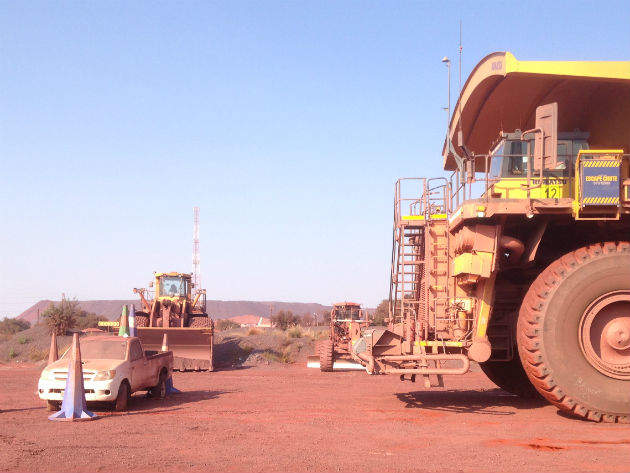
Mining operators are under increasing pressure to identify and exploit new reserves, reduce costs and boost productivity. Are these business imperatives really compatible with improving safety?
“Yes, safety is fully congruent with those imperatives, but it depends on the time scale,” says Fabien Kritter, product manager at Hexagon Mining, a US -based IT company that specialises in integrated life-of-mine vehicle safety solutions connecting surveying, design, fleet management, production optimisation and collision avoidance.
“The current economic situation compels mines to produce more − I have seen projects that extend 12-hour shifts by 30 minutes to increase production − but the question is, what safety measures have been implemented to mitigate the increased risk resulting from these longer working hours?
“Mines are dangerous places characterised by huge machines with terrible blind spots, heavy traffic, long shifts and monotonous journeys. If mines do not take preventive measures it is only a matter of time before an accident occurs and we live in a ‘zero harm’ society where fatalities are not tolerated.
“Yet too often safety during mining operations is seen simply as a cost or investment; this is a short-term view. The cost of an accident in terms of loss of production due to machine downtime, repair and injury can rapidly reach several million dollars. In the worst-case scenario where there is a fatality and the mine has to close for a few days, that figure can jump to many millions of dollars.
“The challenge is to find the right balance between production and safety, because they are linked. Technologies such as the SAFEmine CAS [Collision Avoidance System], FatigueMonitor and Vehicle Intervention System (VIS) can help operators accomplish their task and come home safe each day, despite intense work pressure.”
Safety first: the vehicle intervention system (VIS) explained
Unveiled at the MINExpo event in the US in September, the VIS is designed to add a further layer of protection to Hexagon’s CAS, which provides drivers of large vehicles with 360° proximity detection at any speed and in all conditions via cabin display units.
Installed in more than 25,000 vehicles in 55 mines, the CAS’ GPS unit calculates speed and path of movement so the operator can see where other vehicles are heading. The system’s in-built safety zone feature predicts potential collisions in advance and warns drivers using real-time traffic alerts.
“SAFEmine CAS improves safety and reduces metal contact by improving the situation awareness around vehicles by allowing operators to see vehicles that otherwise could not be seen,” explains Kritter. “However, incidents can still happen due to various factors such as human error and fatigue.
“The VIS is the natural evolution of SAFEmine CAS and the initial impetus came almost three years ago when the Sishen mine operated by Anglo American Kumba Iron Ore contacted Hexagon. They had conducted an extensive risk assessment of their operation to understand their major risks and together with the customer we defined a step-by-step approach to develop a solution.
“The VIS can take control of the machine in certain defined situations if the operator does not react appropriately to the initial warning provided by the CAS. The system can then act depending on the situation, either by inhibiting propulsion, activating the retarder or applying the service brake.
“VIS is fully integrated with Hexagon’s safety solution, and uses the same sensors and user interface to protect the customer’s initial investment,” Kritter continues. “We worked closely with an OEM to make this vision of a last-resort system that mitigates the consequences of a collision a reality.”
Safety in numbers: collision avoidance, production and maintenance
Quantifying the comparative success of engineering safety systems and initiatives is tricky, primarily because mining operators are notoriously reticent about disclosing such data, as Kritter concedes.
“In the long-term, safety is a good investment but it is difficult to quantify the return on investment, often because decision-makers are not aware of accidents prevented by such systems,” he says.
“However, a survey of over 540 operators indicated that 85% are confident that the SAFEmine CAS provides them with additional safety.
“At the 2014 Queensland Mining Industry Health & Safety Conference, a company reported that in the 12 months prior to CAS installation, the mine experienced 14 machine-to-machine incidents. Afterwards, there were only two over the next two years, one involving a vehicle not equipped with the system, while in the other the system warned the operator but he did not react properly.
“CAS, FatigueMonitor and VIS not only prevent accidents, they also enforce better driving behaviour. For example, a small mine in Canada reduced small over-speed events [<10km/h] by 54% and over-speed events [>10km/h] by 100% after implementing the CAS.
“Speeding also increases maintenance costs and can cause tire delamination. The Canadian mine realised a $300,000 in tire savings annually. Even if it is hard to quantify, I can confirm that overall the SAFEmine CAS has saved a couple of lives and several millions of dollars to mining companies.”
Driving innovation: human-assist technology and digitalisation
Despite these successes, is Kritter confident that the global mining industry is fully committed to the concept of ‘zero harm’ and that safety will not inevitably be sacrificed in favour of the bottom line?
“I am always extremely sad when a mining company that we have approached re-contacts us after a fatality,” he says. “It is a question of mentality. When the automobile industry introduced seat belts in the 1970s they took time to be accepted by drivers − today, nobody would buy a car without them. In a few years, such safety systems will be the standard in the mining industry, I’m sure.”
Hexagon Mining has established itself as a major player in the field of life-of-mine optimisation. What other technologies does the company have in the pipeline and where is mining safety technology heading?
“Hexagon Mining has many exciting projects in the pipeline,” he enthuses. “One important development axis involves human-assist products, such as vehicle intervention and intelligent traffic management, both of which offer immediate operational value by lowering operating costs, increasing efficiency and enhancing operator safety.
“Another developing field is mining digitalisation. Sharing and reporting the right data to decision makers means better and faster decisions, and better efficiency, better productivity.
“There are many possibilities to improve information flow in a mine across all hierarchy layers, from the haul truck operators to the mine managers. It means data sharing of our multiple sensors and systems to provide smart reporting and deliver the right information to the right people when they need it. Hexagon Mining is about to make this smart change happen.”