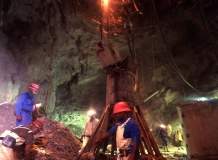
South Africa is home to the deepest underground mines in the world. Delving nearly four kilometres below the earth’s surface, the depth of AngloGold Ashanti’s Savuka gold mine is second only to the company’s neighbouring Mponeng mine.
Extracting materials at these depths magnifies the challenges of underground mining, from ventilation and high stress levels to installing adequate infrastructure. A whole host of new problems are heaped on top of these in the event of an unexpected crisis.
AngloGold had to face one such crisis when a seismic event measuring 2.7 on the Richter scale, along with two serious aftershocks, hit the Savuka mine shaft in May 2009. The epicentre of the seismic activity was around 2km down Savuka’s shaft, and the damage it caused was catastrophic.
As well as killing one mine worker, all production was brought to a halt after rock falls damaged underground infrastructure and the mine’s underground cooling dams burst, flooding the mine with more than 1.3 million litres of water. What’s more, Savuka serves as a support to its neighbour mines Mponeng and Tau Tona, so the sudden shut down of the mine also disrupted operations at AngloGold’s other local assets.
For more than a year after the seismic event, AngloGold laboured to bring the battered, 50 year-old shell of Savuka back to life. The bodies of water and dislodged rock inside the mine, coupled with tiny entrance points and immense distances to cover, made this $30 million refurbishment project a massive and potentially dangerous task.
However, the use of 3D modelling software allowed workers to map out the contours of the mine and minimise delays, turning a seemingly improbably task into an achievable one. We talked to Martin Allerston, one of the two designers dispatched to Savuka by AngloGold to oversee what he describes as a true "crisis job".
He reveals the challenges of the project and the advantages of approaching the refurbishment in three dimensions.
Chris Lo: When you surveyed the damage at Savuka, what were the major challenges that were immediately apparent?
Martin Allerston: One of the problems was that we lost all our cooling towers and our cooling dams. They broke, and it was about 135 million litres that went down the shaft and into the sub-shaft. So we had flooding on a whole level, about 100 metres of water. The first thing we had to do was establish a way of pumping all the water out.
All our piping was damaged, so we only had a 150 metre column that we could use that was still in the shaft. It took about two months to pump the water out. On top of that, we re-flooded the shaft so that we could blast some rocks that were still in the shaft area – the water was used as a buffer so that we didn’t damage more rocks.
Pumping that water out again took another two months, so before we could even get in for design, we were already four months into the project.
After that, we went down and we were swimming in six metres of water to get to the silos. A lot of areas were still closed down and it was actually very bad to go into these areas, so we took a project team of three very experienced mining crew and two designers to go and assess all the damage underground.
CL: Was 3D modelling software always going to play a large part in the company’s refurbishment of the Savuka shaft?
MA: Yes. I’m one of the guys who has used 3D for almost the last seven years. On all the projects I do, I try to work in 3D.
We use the 3D because of the long distances that we cover. In local areas like loading stations, pumping stations and where we established the bulkhead, there we use 3D modelling to a great extent.
CL: What mining software did you use for the project and what role did it play?
MA: In our office, we use Bentley MicroStation. I use Structural Modeler v8 and the 3D package. So we model everything we need from the site, we get our extractions out into 2D and so on.
This is a very old shaft, it’s now about 50 years old. Most of the drawings for the loading station and so on were done by hand. All the steel works in the shaft area were remodelled to build a base to see how we were going to do the project.
We had an ore pass feeding from the 100.25 level, which fed into two conveyors on the south side of the shaft into the skips. We lost that ore pass in the seismic event. Luckily, in 1985 they developed a secondary loading station but it was never put into use.
So we could extend the conveyors on top of the 100.25 level and then come down on the north side of the shaft. But the challenge was then to get the rocks into the skips, because they were on the south side of the shaft.
We built a model and we played around with three or four options that we could manipulate very quickly and show in the boardroom so everybody could get a clear idea. With 2D drawing, some of the guys can’t really see what’s happening, but if you’ve got a real model of the area, it’s much easier to explain what you’re planning to do.
The option we took was actually to go around the shaft with three conveyor systems and then throw back into the existing flasks. It’s not really a good engineering practice, but it was the quickest solution to get the mine back into production, and it’s working perfectly.
CL: At nearly 4km, Savuka is one of the deepest gold mines in the world – does modelling software have any particular advantages when you’re working on a mine that deep?
MA: The actual accident was not at that depth, it was a little bit higher up, at about two kilometres down. What makes the 3D so valuable is that we could model the haulages. For the structural installations, we preassembled the steel on the surface and we modelled the underground areas to ensure it would fit in perfectly.
This was a crisis job, so there was a bit of reverse engineering, but on normal installations, we would build a model, fit everything in and make sure it works.
Savuka is a three-shaft system, openings are about 2.8 by 1.6 metres and you’ve got to manhandle all this steel through these areas. So Bentley software allowed us to assemble the steel on the surface, knowing it would fit in the holes at the bottom. I can’t imagine how we would have done it without 3D modelling.
CL: Do you think the cost of modelling the mine was offset by efficiency savings during the project itself?
MA: As I said, this was a crisis job, so we threw a lot of money at this project to get the mine back into production.
But from what I’ve seen from other projects we’ve done, sometimes the engineers change the equipment that they’re using, and it’s easier to just change one 3D model that links back to your 2D drawings with the changes.
With 2D, each drawing would have to be changed manually, so the time savings are big. Also, you’ve got clash detection to pick up problems, whereas with 2D it’s very difficult.
CL: How widespread is the use of modelling software in AngloGold Ashanti’s general operations? Has it become a core technology for the company?
MA: We’ve made quite a lot of investment into 3D modelling, especially at Mponeng.
There is quite a lot of 3D taking place – some of the younger generation are grabbing the technology with both hands, whereas the older guys are a bit reluctant to change.
I don’t see anybody in the future not using 3D. The packages are getting better and better; there were problems when I started with 3D seven years ago, but all those issues are sorted out now.
At the moment we’re also reviewing ProSteel, another Bentley product, which has automatic detailing and so on. It was running on AutoCAD for quite a while, but Bentley has now come on board too. That cuts your drawing time enormously.