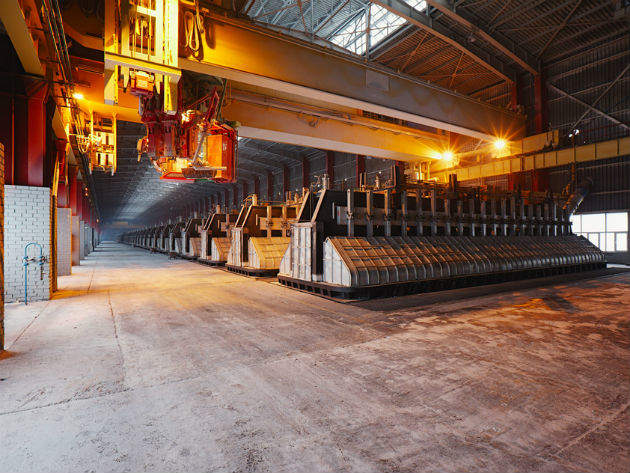
For centuries mankind has been using antimony, a semi-metallic chemical element that in its non-metallic form is a grey powder and when metallic is hard, brittle and silvery. While societies from thousands of years ago used it in the form of stibnite for decoration, in modern times it is used to make semiconductor devices, batteries, low-friction metals, cable sheathing and flame-proofing materials, paint, ceramic enamels, glass and pottery.
The traditional method of producing antimony metal is through heat smelting. However, researchers at MIT claim to have accidentally stumbled upon a new method of smelting using electrolysis rather than heat.
Research was funded by the US Department of Energy, the Advanced Research Projects-Energy (ARPA-E), and French energy company Total SA. The work was carried out by Donald Sadoway, John F Elliott professor of materials chemistry, post doctorate researcher Huayi Yin, and visiting scholar Brice Chung.
Electrolytic refining
Electrolysis, or electrolytic refining, is a technique that is already in use for the extraction and purification of metals, and it is a much more cost-effective and efficient technique than traditional heat-based smelting methods. Indeed, it was the discovery of the Hall-Héroult electrolytic process more than a hundred years ago that transformed aluminium from a precious metal more valuable than silver into a widely used, inexpensive commodity.
More recently, similar advances have been reported with regards to other metals. In 1997, a process to produce tantalum metal was reported. Since then, it has been scaled-up to provide 3% to 4% of the worldwide tantalum supply. Now Metalysis, a spinoff of Cambridge University’s Department of Materials Science and Metallurgy, is looking into the prospects of electrolysis for titanium.
The direct electrochemical reduction of titanium dioxide to titanium metal in molten calcium chloride was demonstrated in 2000 by Fray, Farthing and Chen. Then in 2012, Metalysis successfully produced titanium metal powder in a single step. It is now looking to scale-up production.
How well do you really know your competitors?
Access the most comprehensive Company Profiles on the market, powered by GlobalData. Save hours of research. Gain competitive edge.
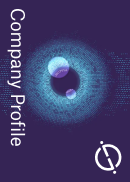
Thank you!
Your download email will arrive shortly
Not ready to buy yet? Download a free sample
We are confident about the unique quality of our Company Profiles. However, we want you to make the most beneficial decision for your business, so we offer a free sample that you can download by submitting the below form
By GlobalDataStumbling across a battery breakthrough
The breakthrough method for antimony came while the MIT team was in the process of trying to develop a new battery system. For years, the lab had been working on a variety of chemical formulations for all-liquid, high-temperature storage batteries.
Different parts of these batteries are composed of molten metal or salts and as they have different densities they form separate layers. Sadoway said the team was investigating the utility of putting a second electrolyte between the positive and negative electrodes of the liquid battery when it found that, instead of charging the battery, “we were in fact producing liquid antimony instead”.
The material they were using was antimony sulphide, a molten semiconductor that normally does not allow for the kind of electrolytic process that is used to produce aluminium and other metals. Although antimony sulphide is a very good conductor of electrons, an ionic conductor – a material that is good at conducting molecules that have a net electric charge – is required to do electrolysis. By adding an ionic conductor layer on top of the molten semiconductor, the team discovered that this second electrolyte in the cell countered the effects of electron conduction. It was this conduction that had previously stymied the efficient high-volume production of transition metals by electrolysis.
The team was able to separate the metal out of the sulphide compound to form a pool of 99.9% pure antimony at the bottom of their cell. Pure sulphur gas, meanwhile, accumulated at the top where it could be collected for use as a chemical feedstock. In a typical smelting process, this sulphur would have immediately bonded with oxygen in the air to form sulphur dioxide, the major cause of acid rain.
Antimony captures electronic niche markets
What the effect of this discovery will be on the global antimony market is hard to guess. Antimony, together with others such as cobalt, gallium, germanium, zirconium, rhenium, titanium, tungsten and the rare earth metals, is classed as a ‘minor’ metal, and world antimony production does not exceed 50,000t per annum (tpa) from total reserves of five million tonnes (Mt).
The main suppliers of virgin materials are China, Russia, Bolivia and South Africa, however, although the overall antimony market is small by comparison with base metals, it is growing in importance.
A new report from Hexa Research points to substantial growth in the antimony tin oxide (ATO) market to 2024. Growth is expected on the back of increasing demand for touchscreen phones, particularly in the Asia-Pacific region. The touchscreen is an important electronic market segment in the smart TV and mobile phone manufacturing industry, and the changing market trend in mobile phones and increasing demand for touchscreen phones is expected to drive the market for ATO.
Use of antimony trioxide as a flame-retardant mineral, meanwhile, has risen sharply and nanotechnology is expected to play a major role in improving the performance of the flame-retardant market in years to come. The largest sales market for flame-retardant materials is Asia-Pacific, with China alone currently accounting for about 24% of the global demand. India is also expected to increase its share in this market.
Steel-making is the ‘holy grail’
The main beneficiaries of MIT’s electrolysis breakthrough are likely to be the much bigger copper and steel industries. Sadoway explained that if the process could be applied to other common industrial metals, it would have the potential to significantly lower prices, as well as reduce the air pollution and greenhouse gas emissions. “The thing that made this such an exciting finding is that we could imagine doing the same for copper and nickel, metals that are used in large quantities,” he said. Although the higher melting temperatures of other metals add complication to designing an overall production system, the underlying physical principles of electrolysis are the same.
Antimony has a melting point of 631°C compared with copper’s 1,085°C and iron’s 1,540°C melting points. The ‘holy grail’ would be steel production as it is the number one industrial source of carbon dioxide, the main greenhouse gas. Also, despite the difficulties presented by the much higher melting point of iron, Sadoway believes that electrolysis is feasible. “On the horizon is molten oxide electrolysis, which has been shown to produce liquid iron and by-product oxygen,” he said.
Refining precious metals
But electrolytic refining is already playing an important, albeit minor, role in the production of base metals. Electrolysis is also widely used in the production and refining of precious metals, for instance, electrolytic gold is produced using hydrochloric acid as an electrolyte, known as the Wohlwill process, which produces gold at 99.5% purity.
Further electro-refining using the Miller chlorination process can improve gold’s purity to 99.999%. The electrolytic silver refining method is similar to that of gold’s, but the silver anodes are dissolved in a nitric acid bath. This process can produce silver at 99.9% purity. In the case of copper, its extraction from other ores through electrolysis, using lead-coated anodes, is well-known in the industry. Indeed, the two-stage solvent extraction and electro-winning (SX/EW) process accounts for 20% of worldwide copper production. This technology is also successfully applied to a wide range of other metals including cobalt, nickel, zinc and uranium.
However, the conversion of solid feedstock into solid metal product using these processes cannot be done in a single phase. The discovery by the MIT researchers enabled them to overcome these limitations by resorting to an all-fluid system: molten semiconducting feedstock converting to liquid metal product and sulphur vapour by-product. As a result, the metals industry may soon be on the brink of a revolution in its smelting technology which could play a major role in bringing about a much cleaner and ‘greener’ world.