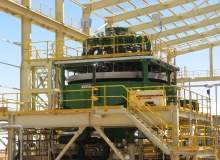
"You don’t go into these things expecting to win awards. It’s like icing on the cake," Laureate Professor Graeme Jameson of the University of Newcastle Australia says when asked how it feels to be honoured with awards such as one of the Prime Minister’s Prizes for Science, which he won in October.
This isn’t Jameson’s first award. In 2005 he received an Order of Australia Medal and in 2013 he won the world’s most prestigious honour in mineral processing, the Antoine M Gaudin Medal, to name but a few.
The accolades are an acknowledgement of Jameson’s groundbreaking flotation technology, the Jameson Cell. The technology, which was made available in the late 1980s after 20 years of research, enables the mining industry to create billions of dollars of extra value by using bubbles to capture super-fine particles of less than a hair’s breadth during mineral processing.
The process involves grinding mineral ores into small particles, suspending them in water and placing them into stirred tanks known as cells. A large mine can treat 10,000t an hour using the cell.
Over 300 cells across 25 countries are currently in use for copper, coal, zinc, nickel, lead, silver and platinum extraction.
Getting started
The Jameson Cell started off as a research project. Using surplus money from research contracts, which Jameson could have kept for himself but decided to reinvest in R&D due to "punitive" tax laws in Australia at the time, he started to make small prototypes with equipment bought at the local plumbing shop.
At the time, 1986, Jameson was working at the remote Glencore-owned Mount Isa mines. When the miners saw what Jameson was working on, the company saw its potential and tested the technology at its facility for a year, eventually taking the licence from the university.
Remarkably, the technology only cost around A$65,000 to develop. Jameson attributes the low cost of development to the equipment already available to him and quick industry adoption.
"That was because the people at Mount Isa were very receptive, they had a long history of developing very good, high-level technology," he says.
Due to the mine’s remote location and complex ore body the company had an in-house research team and as a consequence "there was a culture of trying new things". Jameson was able to take advantage of that.
The industry today, Jameson says, is much changed.
"The whole development chain is a terrible business model for the inventor," he laments.
"The miners will take the view that they shouldn’t put money into the development of your equipment. They’ll say, ‘Oh well, we’ll wait five years for it to be developed and then we’ll just buy one off the shelf.’
"Equipment investors say, ‘Well, the return on this machine is not very great, it will take over ten years to pay back development costs, it’s not worth doing.’
"So unless the industry is in good shape it is very difficult to get funding."
The Novacell
Nearly 30 years after his first groundbreaking innovation, Jameson is currently working on another type of flotation cell, the Novacell, which increases the upper particle size limit of flotation and drastically reduces the mining industry’s energy and water consumption.
Jameson started development of the Novacell – named after Novacastrians, the demonym for residents of Newcastle – eight years ago.
However, finance issues mean he hasn’t been able to get any funding to further its development to the large prototype stage. The technology focuses on recovering coarse particles instead of fine particles.
"It turns out that coarse particles are also very difficult to recover because the particles have to stick to bubbles so they can be separated from the rock," Jameson explains. "In a conventional flotation machine, the liquid is in a tank which is stirred by a mechanical agitator.
"It turns out that if the particles are too big they are easily detached from the bubbles by the agitation. The agitation is very violent, and of course the bigger the particles are, the more you have to stir to keep them off the bottom."
Jameson’s coarse particle flotation system is "very gentle so the bubbles and the particles stick together very well", he says.
There are many benefits to floating these larger particles. For one you don’t have to grind the ore so fine. Traditionally ore fed into a mill comes out in particles about 100 microns in size.
"The energy used depends on the final size, and it turns out that if you could grind them to 400 microns, instead of the 100 microns used today, you would use only half the energy, which is an enormous cost saving in a mine," he says.
It has been estimated by the Commonwealth Scientific and Industrial Research Organisation (CSIRO) that the energy used in grinding rock to retrieve valuable material is equal to 14% of Australia’s electricity production.
Jameson points out that miners would also not need to use so much grinding material and would therefore need to replace equipment less often. And if coarser particles can be floated, the circuit in the mill can be simplified.
"The other thing is that because this machine works with a very high solids content the tailings can be up to 85% solids," he adds.
The Novacell will be used for straightforward base metal ores – copper, lead and zinc.
While seeking finance Jameson says he is finding out in detail what happens within the Novacell and preparing so that when a bigger model is finally designed it can be done with "great detail and certainty".
"I am not terribly bothered about the fact that I haven’t been able to get funding because the more I know, the more results I get at a small scale, the less risk there is to an investor coming in at a later date and therefore more returns to the inventor," he says.
"I think I am on the cusp."
Experience and passion
After his many years as an inventor and scientist, Jameson has his share of ideas about how to solve the inventor’s biggest burden – finance.
"The best thing that can be done is for government to make available funds to bridge that gap between the laboratory and the operating plant," he says.
"The fact of the matter is that companies in this country are very risk-averse and they are not very interested in R&D."
Asked for his advice to young, budding scientists looking to follow in his footsteps and make a mark on the mining industry, Jameson says: "If you are looking at mining as a traditional activity, the two key areas are energy and water.
"If you look further into the future it’s likely that people will want to carry out mining and milling as much as possible underground, so they don’t have to move the ore and they don’t have to find places to put the waste material – so if you are a critical scientist or an engineer those areas are attractive."
However, he warns that, as a young person, "You would have to look at whether there are better ways of spending your time because you’ll have to be pretty determined to get your foot in the door with new technology."
At the tender age of 79, despite the current challenges, Jameson himself is still determined to push forward; what drives him to keep inventing when he could simply retire?
"Ah, it is the simple wonder," he says. "All the time I see things happen that are just wonderful. That is what drives me."