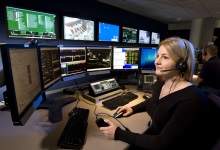
The mining industry is in need of a shake-up. The once high market prices across the mineral markets are becoming an ever more distant memory, driving companies both big and small towards a more efficient and less costly mode of operation. In addition to tightening its belt, the industry must continue to push forward to seek out new territories and secure its future workforce.
The answer to such challenges, in the eyes of many, is to be found through automation; stripping out the human factor where possible from the production process can cut costly downtime and increase worker safety. It can also enable the industry to pitch itself to the modern, tech-savvy generation of workers, whose designs on working life lie in the hustle and bustle of big cities rather than the remote, near-deserted regions where the digging is done. Speaking on the issue, Rio Tinto CEO Sam Walsh said: "Some people have expressed concern about automation but quite frankly it’s getting harder and harder to attract young people to remote areas."
Handing over the leg work to machines opens up a number of opportunities to operators. Safety checks can be carried out at the touch of a button, real-time analytics can inform improvements in workflow and human operators and engineers can flick between sites located thousands of miles apart at will, without ever setting foot on site.
Mine control from thousands of miles away
One of the companies leading the charge is Walsh’s Rio Tinto, where its operations centre in Perth in Western Australia, located next to the city’s airport, houses a team of 200 controllers and schedulers, and even more technicians, who manage operations at 14 different Rio Tinto mines located up to 1,500 kilometres away. From their desks, operators monitor and manage each stage of the production cycle, analysing performance metrics and processes in order to ensure that work on the ground is achieving maximum efficiency.
Across the Western Australia mine sites, autonomous drilling rigs are being trialled at the BHP Billiton Mitsubishi Alliance, driverless trucks are transporting iron ore for Fortescue Metals Group and Rio Tinto is in the final stages of launching driverless trains to deliver its quarry from site to port. In between and throughout each stage, sophisticated machinery equipped with sensors fill in the gaps and feed back detailed information to control centres.
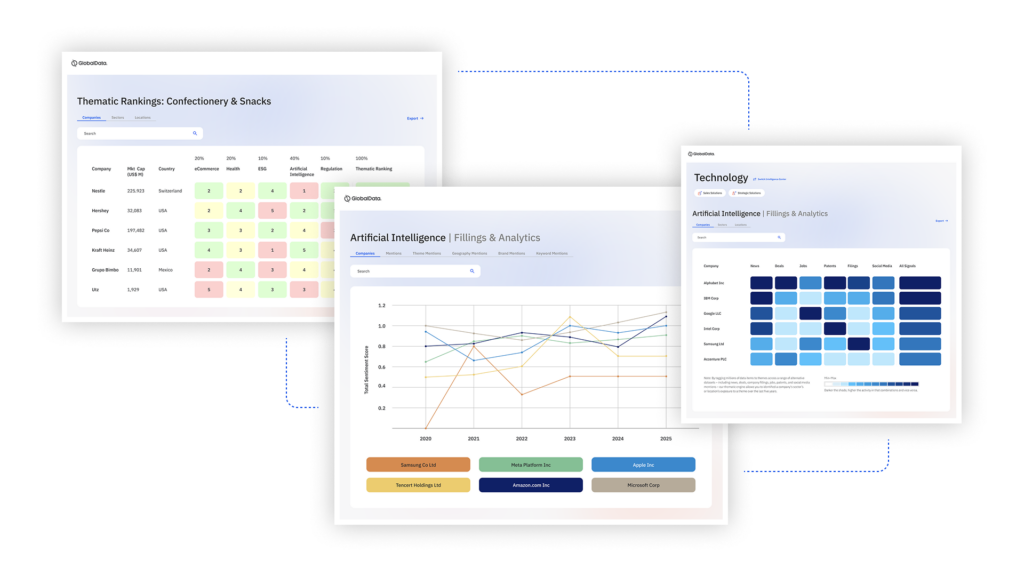
US Tariffs are shifting - will you react or anticipate?
Don’t let policy changes catch you off guard. Stay proactive with real-time data and expert analysis.
By GlobalDataMine Location Intelligence, a mobile, location-based system created by ABB and Mobilaris, can both improve personnel safety and boost productivity.
The age of autonomy has well and truly arrived in Australia, and the technology is expected to shortly take a firm grip in other major markets. In preparation for its wider adoption, the International Standards Organisation (ISO) has started to develop a global safety standard, ‘ISO standard ISO/NP 17757, earth-moving machinery — autonomous machine system safety’, which will set the bar on the development and use of automated technology in mining.
As part of the development of the standard, Daniel Roley, chair of ISO technical committee ISO/TC 127, travelled to Australia to meet with the companies and manufacturers that are leading the way in autonomous mining. During the three-day tour, he met with representatives from mining firms, including Rio Tinto, BHP Billiton and Fortescue Metals Group, to discuss the benefits and challenges they have encountered from trialling the technology and putting it into full use. He also met with equipment manufacturers, such as Cat, to get their input. Roley explains that the information gained from talking to the firms, as well as codes of practice and guidelines provided by the Western Australian Department of Mines and Petroleum, will be of vital importance in the development of the standard.
Australia leads the way in standard development
"Our goal is to develop standards with safety performance levels that allow machines to be used to achieve zero injury during the life cycle of machines," says Roley. "We will benefit from the experience and concern for safety in Western Australia to help our ISO experts develop a global safety standard for autonomous machine systems that can be effective for Western Australia and for the rest of the world."
Tony Ottaviano, vice president of planning at BHP Billiton, who met with Roley, said: "Autonomy is the journey that a number of the large mining companies are taking; it is the future, so having fit-for-purpose and appropriate standards by a world-recognised body like ISO is critical."
To provide this critical standard, the working group will need to identify a broad range of risks associated with automated mining. While they are continuing the identification process, Roley is already certain of one of the major issues. "One of the challenges for autonomous machine systems is to develop electronic systems to duplicate the capability of operators for sensing what is happening around machines, for controlling the machine and for planning the movement of the machine, so that the machines can be used safely without on board operators", he says. "The ISO standard will identify the risks associated with removing the operator from machines and provide safety performance criteria to address the risks."
Other issues that will need to be addressed in autonomous mining include measuring the build-up of toxic or flammable gas and materials during the extraction process and monitoring the temperature and capacity of the machines carrying out the work. The removal of human workers from the operating environment will also remove constraints on the hours that work can be carried out. One of automation’s most attractive aspects is that an operation could conceivably operate 24 hours a day, seven days a week; however, such a schedule would place extra strain on the equipment. Understanding just how much work can be carried out by the machines and developing sensors to detect potential problems will be crucial.
Risks remain even without humans in the loop
Above ground, the most critical risk will be ensuring that the hazard detection systems attached to the autonomous vehicles live up to the billing as being safer than having someone at the wheel. Current systems, which are being assessed as part of the standard, combine a global positioning system, radar sensor and a camera view that is transmitted to an operator. Setting a minimum standard of safety for the autonomous transport of the materials will be key to avoiding collisions with other machinery, wildlife or even people.
The full scope of the issues is still not known. Roley and the working group are continuing to collaborate with industry to identify them, but once established, the global standard should serve to encourage the production of safe and reliable technology and discourage that which is below par. "Typically an industry standard is considered ‘state-of-the-art’," explains ASI Robots chief engineer Jonathan Moore. "Not adopting and even not being aware of state-of-the-art has potentially very serious product liability consequences."
Moore adds: "Adoption may take time but organizations that have the maturity and skills to treat standards compliance seriously are generally those providing higher levels of reliability, robustness and customer satisfaction since they are committed to continuously improving their processes, products and most importantly their people."
A further benefit of its creation will be that it will reduce the confusion and inconsistency created by having competing standards at a national or company level. "A global standard would be good to harmonize the safety criteria," says Metso Corporation’s vice president of technology services Jari Riihilahti. Riihilahti explains that the challenge for the ISO team will be striking the right balance between complexity and accessibility: "One global standard that is not too complex would be good for the industry."
Once launched, ISO/NP 17757 will bring structure and convention to the manufacture and use of autonomous mining technology. Thanks to the support and contributions from the mining firms, manufacturers and public bodies in Western Australia, the wider industry should be able to make the transition to automation a little more steadily.