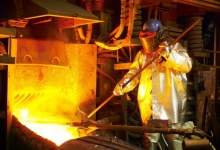
By 2023, the mining industry in Canada will require over 145,000 new workers, according to a 2013 report from the Mining Industry Human Resources Council (MiHR). This is over half the current workforce.
The skills shortage in the industry represents a significant challenge to filling all mining roles, but will undoubtedly affect some more than others. For example, while administrators, cooks and financial analysts can be transferred from many other industries to mining with little adjustment, industry-specific roles, such as underground drilling and mining, pose more of a challenge.
The report projects that the estimated talent pool for underground miners will not be enough to meet the industry’s needs by 2023. Trades and undesignated occupations, including underground mining, will need over 47,000 workers by 2023, according to MiHR executive director Ryan Montpellier.
Underground roles are also some of the most demanding, potentially dangerous and challenging in the industry. Underground miners can expect to work at depths of up to 2.5km – mines are now pushing to even further depths – for twelve hours a day for a minimum of four days in a row. This at temperatures that, according to Centre for Excellence in Mining Innovation CEO, president and chair of holistic mining practice Douglas Morrison, a mining veteran with more than 30 years’ experience, hover around the 35 to 40 degree mark with very high humidity. Many roles also require workers to fly in for two weeks of daily work and to then fly out for two weeks’ rest.
Although underground conditions have undoubtedly improved in the last 50 years and Canada’s underground safety record is excellent, is there a need to further modify working arrangements and invest further in technology in order to improve underground mining conditions and culture to attract a new generation of miners?
Challenges in attracting underground miners
Shell Canada and Caterpillar are testing a new engine and fuel mix using liquefied natural gas (LNG).
"It is very difficult to attract people to work in these conditions," says Morrison, who is working on a five-year industry-funded project called the Ultra Deep Mining Network (UDMN). The project aims to develop technologies and solutions to enable miners, not robots, to go deeper underground.
The ‘difficult’ conditions Morrison is referring to are primarily the heat and humidity, which progressively escalate deeper underground. While the industry in Canada is now investing in technologies to improve working conditions for ultra-deep drilling – classified as deeper than 2.5km – Morrison suggests that the previous generation "should have objected before" and the "current generation is going to object; they are just not going to show up."
Prospectors and Developers Association of Canada executive director Ross Gallinger says the conditions in underground mines are no more or less challenging than working in construction. The Canadian construction industry is also facing skills shortages in some areas but these are being counteracted to some extent by job losses in other areas.
"The challenges of attracting youth are awareness of career potential in the sector; jobs are where the mines are, and people may not wish to move or work in a ‘fly in, fly out’ arrangement," he says.
"For some people that lifestyle works but for many people it does not," says Montpellier. "I think we’re able to, as an industry, find people that want to try it; they do it for a few years but then eventually they look for work so they can go back to their own bed and their own families on a regular basis. So retention is certainly a challenge."
This does mean, however, that opportunities for indigenous peoples are "boundless", says Gallinger, as many mine sites are located near aboriginal populations. However, currently, according to the MiHR report, although the mining industry is a major employer of aboriginal peoples, they are mainly found in entry-level and support roles. The same is true for women, who make up 16% of the workforce, but are mainly employed in administrative and office roles, with very few employed in trades and production roles.
However, Morrison says: "Unless we can provide clothing and personal protection and conditions that are much nicer we are not going to attract women to work in our industry."
Technology shift – is automation the answer?
Morrison says the research UDMN is doing is focused on making working environments more comfortable for miners with cooling suits, better ventilation, fibre-optic communication tools, and is very much focused on having miners, rather than automated systems, underground
However, Montpellier thinks focusing more on the development and deployment of automated technology, removing miners from the mines altogether, and offering a different working lifestyle will attract more young people to the industry. He refers to technology such as programmable logic controllers (PLCs) and tele-mining, which is remote operation of equipment from a control room located on the surface, possibly even in a convenient urban or semi-urban environment, removing the miner from the worksite altogether.
"By removing the need for workers to live in remote environments, away from modern conveniences and their families, this shift has the potential to make mining a more attractive career choice for a diverse group of people," Montpellier says.
"Furthermore, the ‘digitalisation’ of existing machinery adds a high-tech component to mining that research participants believe will make the industry more attractive to young people, provided the current state of technology in mining is communicated."
Meeting the shortfall – a multi-attack approach
What does the labour market in the global mining industry look like in 2014? Four industry insiders give us the low-down.
Meeting the shortfall of underground mining in the coming decade is undoubtedly going to be a challenge. To do so, as has been pointed out, the industry needs to take a multi-pronged approach. Investing in improving the underground working environment, as the UNDM is currently doing, and deploying more automation are just some things that can attract youth.
Others include reducing working hours from the current gruelling twelve- hour shift to a more moderate eight to ten hours; Morrison believes this could even improve productivity. Another is changing the image of the industry; Montpellier believes "youth often hold negative and dated perceptions of careers [in the mining industry]," not forgetting better career awareness at a younger age and working with aboriginal and indigenous communities.
Different approaches will no doubt work for different companies and their mines, but modifying corporate culture to suit workers’ lives could be key to finding and retaining a new generation of mining staff.