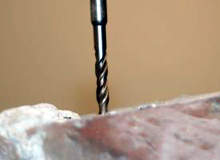
Resources are becoming scarcer and more valuable, and it is more important than ever to exploit resources to their maximum in a cost-effective way. Mining companies are trying to balance the drive for cost effectiveness with increased productivity with new technologies at all stages from exploration to export.
The techniques and tools at the front line are among the top priorities, hence the huge investment that many mining companies are making in drills and drilling control systems.
Rising commodity prices have given many of these companies sufficient cashflow to invest not only in new assets, but also the development of more sophisticated technology throughout the drilling and processing chain. Drilling is a key focus, given that it is a significant contributor to the total costs of exploration and mine production.
A key focus of current research and development is extending a drill’s lifecycle, thereby reducing cost in the long-term and, potentially, increasing productivity.
Work on creating durable, hard-wearing drill bits has been a priority for the Commonwealth Scientific and Industrial Research Organisation (CSIRO), Australia’s national science agency, which has devoted significant time and resources to developing highly wear-resistant cutting elements as part of its SMART*CUT drilling technology development project.
CSIRO believes that these tools could revolutionise mining excavation by offering faster rates of penetration with lower energy expenditure. SMART*CUT – Super Material Abrasive Resistant Tools – uses thermally stable diamond composites (TSDC) in cutting and drilling tools. TSDC is over 1,000 times more resistant to abrasive wear than tungsten carbide, and problems with thermal instabilities limiting traditional diamond composites have been overcome.
CSIRO is now prototyping drill bits using TSDC, after laboratory drilling trials showed that the rock drill bits have twice the penetration rate and expend half the energy of traditional rock coring bits. There is certainly potential for mining companies to make significant savings as the technology develops.
Accuracy and capacity
The efficiency of a drilling system will depend to a large extent on the speed and accuracy it can achieve. Technology developers such as Sweden’s Atlas Copco have been working on systems that can combine the accuracy of down-the-hole (DTH) drilling with the capacity gains of hydraulic top-hammer drilling.
Previous efforts to combine to combine the advantages of these two drilling methods have met with limited success, but Atlas Copco believes that its COPROD systems have succeeded by integrating two types of drill string for percussive drilling.
Percussive drilling systems hark back to a time when manually striking and turning a steel rod would create a round hole. Most top-hammer drilling uses extension rods connected with threaded coupling sleeves, plus an exchangeable drill bit. This works well for smaller holes but fails as the diameter grows, given the limitations on energy transfer to the drill bit, as well as the problems with flushing and accurate alignment.
COPROD uses inner drill rods to transmit power to the drill bit, while outer tubes transfer rotation, meaning there is greater stiffness in the string and flushing efficiency improves. The rods have no threads but are stacked, with the result that high top-hammer drilling rates can be achieved in large holes.
The COPROD system may require a higher initial outlay than competing technologies, but Atlas Copco’s test data shows that it may well prove more economical over its lifespan than comparable systems.
Investing in new technologies
The current high levels of investment in new technology suggest that for large mining operations there is a focus on long-term value. Companies are spending now with a view to reaping sustainable and tangible benefits over the lifecycle of their operations.
Rio Tinto, for instance, massively increased its research and development budget in 2007, with a clear commitment to improving the performance of its mining operations through advanced technology. A feature of this research will be the development of new materials, possibly for the design of more durable drill bits.
This would add to the significant advances the company has already made, given that it is already using bespoke autonomous drill technology in its programme to automate its operations in Australia’s Pilbara iron ore region.
The staged introduction of new technologies at Pilbara began in 2006 with the development of autonomous drilling rigs.
More automated elements along the mine-to-port chain are now being commissioned, including the remote operations centre 1,300km away in Perth, driverless trains to carry ore, a driverless truck fleet and remote control ‘intelligent’ drills.
All of these developments are intended to increase efficiency, reduce production costs and improve working conditions to help the company compete as an attractive employer in what is a challenging labour market. The company’s management believes that human labour will no longer need to be hands-on as the equipment will be autonomous.
Rio Tinto’s chief executive Tom Albanese believes that the company is “changing the face of mining. We have at least a three-year start on the rest of the industry, which has focused on discrete technologies rather than modernising the whole mine-to-port operation,” he says.
For drilling technology, as well as the other components of the mine automation process, the dominant technology trend is likely to be robotics. Much of Rio Tinto’s investment is aimed at replacing humans in the production process. The pace of this development will depend largely on what emerges from the centre for mine automation centre funded by Rio Tinto and based at the University of Sydney’s Australian Centre for Field Robotics (ACFR).
“The Centre aims to provide a substantial improvement in safety, predictability, precision and efficiency of mining through the development of automation and remote operation across mining systems,” says Rio Tinto’s head of technology and innovation, Dr Grant Thorne.
Autonomous drilling technologies are already in development at CSIRO and elsewhere, and will no doubt be commonplace in the mines of the future.