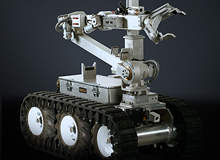
There has been a great deal of discussion about the applications of robotics for emergency response. Robots can be used to conduct dangerous tasks like bomb disposal and handling hazardous chemicals without fear of endangering human lives. This makes them ideally suited to rescue operations after mine explosions or collapses, as they can access areas that would be lethal to human rescuers.
Although the use of robots is picking up across the world, the trend has largely passed the mining industry by. The impact of the lack of mine rescue robots was felt keenly in the aftermath of the Pike River mine explosion in November last year, when rescuers made use of a military-grade robot from the New Zealand Defence Force to try and reach the trapped miners.
The robot short-circuited after hitting water and authorities were forced to seek another unit from Australia or the US, wasting valuable time. So why, with mine disasters still a disturbingly regular occurrence, doesn’t the industry have easy access to robotic rescue units that are specifically tailored to the challenges of delving deep into mines in search of survivors? Why aren’t 2010’s high-profile mine disasters, those that took place in Chile, China, the US, Turkey and New Zealand, translating into renewed interest in the robotic rescue option?
Mining Technology talked to Michael Knopp, president of robotics company Remotec, about how robots could contribute during the mining industry’s darkest hours. Remotec developed and manufactured the ANDROS Wolverine, one of the only mine rescue robots on the market, with one unit purchased by the US Mine Safety and Health Administration (MSHA).
Chris Lo: Why do you think robotic rescue units are so uncommon in the mining industry?
Michael Knopp: In our experience, there are a couple of things. Firstly, mining operations tend to not have budgets for robotic vehicles. We have only one vehicle in the industry right now, with MSHA [Mine Safety and Health Administration] here in the US. That’s the only vehicle we’re aware of, so they don’t have the budgets for it.
Interest tends to peak after an incident occurs, but then it drops back off again. The other thing we sense is that mine regulations aren’t as strict as they need to be, so the need for vehicles isn’t enforced in the way it could be. So regulations and a lack of enforcement play a part, too.
CL: How is the ANDROS Wolverine system that was purchased by MSHA equipped to fulfil its role?
MK: To our knowledge it’s the only real proven piece of equipment out there. The vehicle is sealed to protect against causing an explosion in a mine. It will handle some water, unless it has to drive through a pond. The other benefit is that it has one mile of spooled fire-optic cable on it, so it gives it quite a bit of distance.
The downside to any robotic piece of equipment in a mine is ideally it would be nice to use radio controls or drop breadcrumb repeaters along the way to do your communications, but the problem is you have to make those sealed so that they don’t cause an explosion. So that’s the biggest risk.
This vehicle is fairly large – it’s around 850lbs; it was designed specifically for MSHA and it’s our base platform that we can readily recreate. It’s very durable; it will go a lot of places other vehicles will not. It has a heavy duty arm in order to move things in its way, and that’s a pretty significant advantage. The camera systems are pretty robust so you get good feedback to your control stations.
CL: What lessons can be learned from recent mine explosions like Upper Big Branch and Pike River when optimising robotic systems in the future?
MK: With the Chilean disaster and other mine disasters in China in particular, we’ve had inquiries from Australia and lots of other places. Folks are really interested in putting this equipment into mining operations. But they can’t afford it or they don’t want to spend the money. So we get inquiries all the time and we have technology upgrades that we can put into these systems that will enhance what’s out there now.
But one of the biggest lessons learned is that when disasters happen around the world, it takes a lot of time for rescuers to fly equipment in from remote locations. Whether every mine has a robot or not, I’m not sure that’s completely necessary, but it’s clear that within countries or regions, there needs to be a team that has this kind of equipment readily available, so they can have it on site, on demand, and not take a week for it to get it there.
I don’t know if this is a lesson learned but it’s another observation. Our piece of equipment right now is about 850lbs, and one of the lessons that the robotic community can probably take is to ask if that’s really the right piece of equipment. For example, we have a new piece of technology coming out within this year that is going to be HAZMAT and mine safety ready. It will be purged and pressurised, it will be intrinsically sealed, and it will be much smaller and more mobile than the existing equipment. So maybe one of the lessons learned is to stop relying on big pieces of equipment; find something more mobile, easier to move and more readily available.
CL: What did you learn from the deployment of the ANDROS Wolverine robot during the Sago mine disaster in 2006?
MK: From what I understood of that disaster, the robot worked well and got quite a ways into the mine before it ran into…I don’t remember if it was deep water or a blockage. That’s just one of the hazards you deal with. Now, in terms of dealing with those kinds of obstructions, one of the options is to use a larger robot and have a marsupial smaller robot, like the one we’re working on, that you can deploy off of that to get around or through that kind of obstruction and go further. You could then use the larger vehicle as a potential communications repeater to gain additional distance. Its equipment has sensor capability as well.
CL: How could the application of more advanced sensor technology benefit robots that have to find miners in low-visibility conditions?
MK: In terms of robotics? That’s a tough one. All the sensors you would ever need are out there already. We have many of those mounted on our existing robot. But it doesn’t matter what kind of sensor it is if you can’t get it to where you need it. The main challenges is getting it where you need to be without causing an explosion in the process.
CL: Robots can reach areas that humans can’t in dangerous mines, but what is the potential for rescue robots to actually bring survivors out as well?
MK: I won’t say there isn’t that possibility, but I know we haven’t thought through that, and I’m not sure if any others have, but that’s certainly a technology that would be interesting.
You could envision taking the robot in, finding a survivor and if the path was clear enough, you could deploy some kind of gurney and use the robot to tow him out. Or load him on to a cart or some kind of a skid device. But this is all dependent on the environment and the obstacles you’re dealing with.
CL: Is it the case that the robotics world is waiting for the market to wake up before developing more advanced ideas?
MK: When the world gets tired of mine disasters occurring, and when the industry gets tired with mines not complying with safety regulations, and when budgets become available… there’s just a whole stream of things that has to happen. How many more disasters do we have to have before these mining operations put things in place to give themselves a chance?