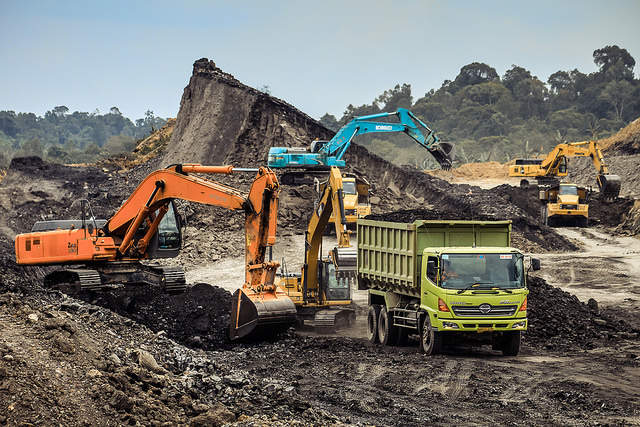
The concept of digital mining is nothing new. In fact, a 2017 EY poll of more than 700 industry representatives revealed that the majority had already started the digital journey. Their activities, however, mostly consisted of small-scale, initial ‘no regrets’ projects, but nothing near revolutionary.
Yet digital goes beyond simply adopting technology – it should be addressing key business issues and resolving the sector’s number one operational challenge: improving productivity across the value chain, according EY.
Despite the opportunity presented by the technology that’s already harnessed by other industrial sectors, EY insists the transformative benefits of digitising the mining sector is far from being fully realised.
Here, Heidi Vella gets some insight into the industrial benefits from EY global mining and metals advisory leader, Paul Mitchell.
Heidi Vella: In EY’s report, it states there is a disconnect between the potential from a digital shift and the successful implementation of new technologies; why is this still happening in the mining sector?
Paul Mitchel: Our Digital Disconnect report highlights some reasons. Mining companies have been innovators and early adopters in the past, but have a poor track record of implementing technology. Some key challenges relating to digital have concerned us.
These include a notable lack of clear direction for the implementation pathway; there is consensus between stakeholders on the digital vision but little discussion on how to practically and effectively move from current state to digital adoption.
A perception of high costs, namely that decision-makers think projects linked with IT systems often over-promise and under-deliver, often with significant budget overrun. This perception delays the decision to start a digital initiative. There is a degree of scepticism from leadership about the robustness of the business case for digital and a lack of clarity on what the new business model will look like.
Furthermore, ownership of digital transformation initiatives is often unclear, and siloed organisational structures create a mismatch between teams that operate differently.
Also, data systems often lack maturity to support a future vision – there needs to be an increase in the quality of data available for decision-making. In some areas, there are huge amounts of new data, while other parts of the value chain present with gaps in data quality and issues in gaining access to required information.
HV: Do you see a change in miners’ attitudes towards digitisation and is anyone in particular leading the charge?
PM: Digital mining has been with us for over half a century and the mining sector has already embraced the introduction of new technologies, such as plant control systems, GPS technologies, mobile broadband and automated haulage. Miners have been the leaders in this field but have reached an inflection point. They are now struggling to identify what the future digital state should look like, hampered primarily by challenges in executing strategically planned implementation.
I don’t think there is a clear leader in digital at this stage, but rather different companies are leading in different areas. Some are leading in the automation space to improve productivity, while we’re seeing ground-breaking developments in the innovation space from others.
HV: How does digitising help miners stay ahead of the competition?
PM: It’s not really about adopting technologies but rather thinking of it as a fully integrated business culture shift. Within operations, digital should initially be used to drive productivity.
Indeed, a number of applications provide an excellent way to manage the challenges of variability and to gain commercial advantage.
These include optimising plans and productivity rates by combining detailed ore body data with equipment operational and maintenance data; enhancing asset reliability with predictive maintenance systems that can improve haulage rates, reduce labour costs and minimise equipment downtime; understanding true end-to-end capability and systems bottlenecks, and supporting loss elimination; as well as using predictive analytics to increase agility and responsiveness to changes in market factors.
The second wave of opportunities is around improving the supply chain in the broadest way possible, and extracting commercial advantage in the sales process.
HV: Specifically, how can digital technology improve productivity across the value chain?
PM: To answer this it is necessary to look at assets through the lens of a business system. While mines were scaled up during the boom to maximise production, mine managers were not provided with the tools to manage this increased complexity. The scale of these larger mines and the related intricacy created an increased pressure on the functional departments to manage these burgeoning workforces.
A silo mentality has crept into the management of mining companies. We refer to the gap between the creation of silos and the desire to eliminate them as ‘the integration gap’. Adoption of an end-to-end process model / business system approach to the organisation is key. This provides greater communication and transparency across the line, which leads to improved and more timely decision-making, and ultimately to improved productivity.
Having a manufacturing mindset can lead to significant productivity and value creation and, in turn, helps close the integration gap. However, mining is not a factory; there is far more variability than a factory environment. Factors such as weather, ore body knowledge, work conditions and quality of workforce all impact variability. There is no silver bullet to remove variability. But it is possible to reduce it to a more manageable level and improve long-term productivity through digital transformation, which we believe will be crucial in driving improved performance and better managing variability across the value chain.
HV: When starting their digital journey, what should miners consider and where should they exercise caution?
PM: The same rigor that underpins other major change or expenditure initiatives needs to be adopted to strengthen digital transformation. Before embarking on the digital journey, a sober assessment of the way forward is required. There needs to be a clear alignment between the digital vision and the overall business strategy. This will move the business away from the adoption of technology for specific purposes and ensure an end-to-end approach.
Other factors to consider include: how long will it take and what is a reasonable estimate of cost? Do we have a clear business case to support the change? What capability do we need and how does this compare with current resourcing? Which packages of work are required to move from our current state? What is the level of cultural support and have we addressed critical elements of the change? Do we understand how the new digital operating model will look? Have we tested this with those who understand the operations in depth?
HV: Cybersecurity is also a significant problem for miners – EY lists it as the third-biggest risk factor. How can miners manage the implementation of more digital technologies but also protect themselves from cybercrime?
PM: In our Global Information Security Survey this year, 55% of mining participants noted experiencing a significant cybersecurity incident in the last year. Malware that targets operational technology is becoming more prominent and is a matter of particular concern for mining and metals companies. In addition, the attack surface is getting larger, with the increasing investment in digital and reliance on control systems for efficient operations.
Mining and metals companies need to have a clear plan – their digital roadmap needs to be cognizant of cyber risk, or face a major incident. There needs to be a recognition that cybersecurity firstly requires the organisation to establish a baseline of ‘basic’ cyber maturity, supported by a risk-based approach to prioritise strategic, long-term cyber investment for the subset of top cyber threat scenarios.
HV: Finally, if companies fail to digitise, what are the risks to business?
PM: They will be less competitive and move up the cost curve.