
In the north of Western Australia’s remote Pilbara region, at all hours of the day, giant blast hole drills owned by BHP Billiton bore into the earth at depths of up to 14m in search of precious iron ore.
Yet, these particular rigs supplied by Atlas Copco Drilling Solutions are, literally and figuratively, ground-breaking. Rather than being controlled on-site, they are transitioning to remote operation from a control room 1,300km away in Perth. Welcome to the brave new world of autonomous drilling.
BHP has been trialling the technology on Pit Viper 271 rigs at the Yandi mine for the past two years. During that time, the machines have operated autonomously for more than 15,000 hours and drilled more than one million metres. BHP has reported a 20% improvement in the optimisation of its drills.
Impressive, but according to Tyler Berens, product line manager − automation at Atlas Copco, we are only beginning to see what autonomous drilling can do in terms of boosting operational efficiency.
“A few months ago, we asked ourselves ‘how far away can we run a drill from the control room and still maintain network communication standards in terms of bandwidth quality and latency?’,” he says. “We were able to run a drill at our test centre in Texas from Stockholm in Sweden, 8,100km away. Staff ran it teleremotely, but, crucially, we were also able to initiate autonomously and supervise, too.”
Loud and clear: Network comms and the BHP collaboration
The issue of network communications, even in open-cut mines, is key to successful automated drilling. Contact between the rig and the autonomous or teleremote system must be seamless. Atlas Copco’s solution is agnostic, meaning it will work with each customer’s bespoke network.
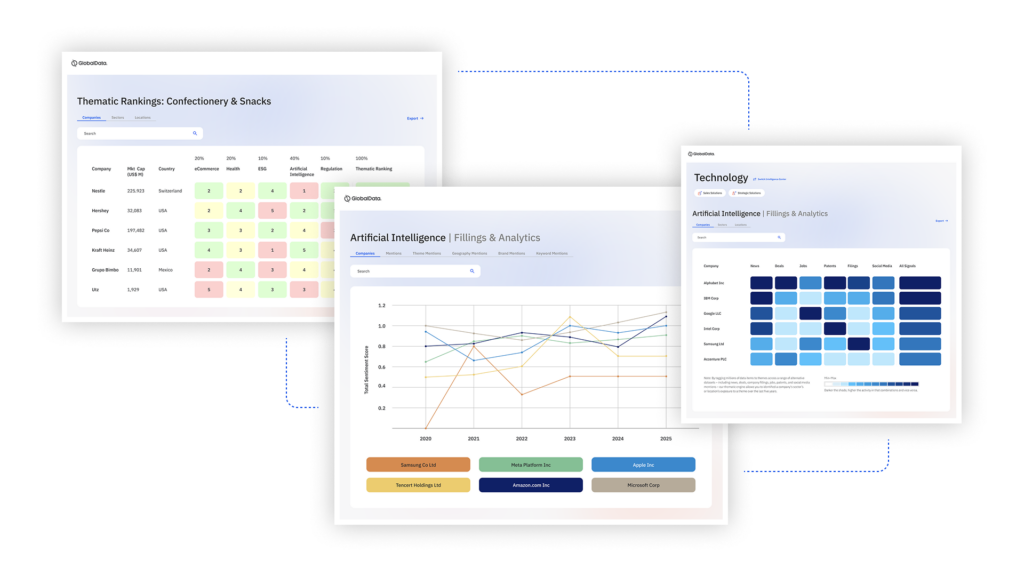
US Tariffs are shifting - will you react or anticipate?
Don’t let policy changes catch you off guard. Stay proactive with real-time data and expert analysis.
By GlobalData“Wireless communications and networks that link the control centre and the drill site play a pivotal role in automated mining operations,” confirms Berens. “For BHP, we are running around 1,300km between control room and drill and we’ve learned how to make those systems more resilient.”
As a result of the successful Pilbara trial, the Anglo-Australian operator has ordered autonomous upgrade packages for a further 18 of its rigs. The 20-strong fleet will initially be controlled at BHP’s five iron ore mines in Pilbara, with the long-term aim of remote operation from a base in Perth.
“It was the perfect merge,” says Berens, “Atlas Copco was running short and focused field trials of operated-assisted automated drills assessing everything from obstacle detection to auto-navigation. We tested in Arctic-type conditions in Northern Europe to mines in humid regions in the Southern Hemisphere. It was simply time to put it into sustained operations.
“BHP, meanwhile, was looking at how the technology was maturing and the key efficiencies for its mining operations and decided that there was a lot of value to be gained from automated drilling.
“We proved the drill could work in the field and then ran fully autonomous blast hole operations with three Pit Viper 271 rigs. Then it was about a roll-out strategy; we decided to adapt a fleet of drills at a time with the automated systems, so as not to disrupt the mine’s day-to-day operations.
“This was made simpler by Atlas Copco’s decision a few years ago to build a retrofitting capability into the Pit Viper’s rig control system (RCS) so that any drills can be automated relatively easily.”
Better by design: the benefits of automated drilling
The multiple benefits for BHP include optimised drilling − which in turn improves digging, loading and hauling − and increased machine uptime, without compromising the quality of the mined ore.
The Pit Viper 271 is capable of working for 11.5 hours of a 12-hour shift, with just one person required to oversee three drills, compared with around eight and a half hours with human operators.
“Mining is a manufacturing business and it’s a game of efficiencies,” explains Berens. “The blast hole drill is one of the first operational steps in that value chain. Therefore, automating that process and getting rid of the element of human free will and replacing it with predictability adds a lot of value.
“The first improvement is obvious: speed. We saw roughly a 16% increase per cycle in the overall speed of the drill, which is a significant number, much bigger, in fact, than we’d initially predicted.
“The second benefit of automation concerns consistency. Every stage of the process is informed by the previous one, so if you can’t predict every element of the process then the whole system suffers.
“In terms of standard deviation metrics, the automated drilling resulted in a huge improvement in every part of the process – drilling, levelling, tramming and delevelling − allowing our mines to start thinking about having a ‘just in time’ methodology, which again has huge benefits up and down the value chain.
The Pit Viper 271 also provides feedback on torque, downward pressure and rotation speed.
“The third key issue is quality. Being fast and consistent is no good if you are then delivering a poor product. The automated drill is guaranteed to be where it is supposed to be, at the exact depth that the engineer designed it to drill to − and in most cases will up hold better until the blast technician can fill it.
“Once we had these three elements in place, we started looking at capacity. We have seen up to a 30% increase in drill capacity, almost one third, which is huge in terms of total cost of ownership (TCO) for drills.”
Future innovations: linking the data and control chain
Mining, particularly in Australia, has suffered from rock-bottom commodity prices and dwindling reserves. Any technology that offers increased efficiencies and margins is therefore at a premium.
With this in mind, plus Atlas Copco’s achievement of running an automated drill in Texas from a whole other continent, how does Berens see mining technology evolving in the short to mid-term?
“Now that automated drills and other automated equipment are in many mines, we at Atlas Copco spend a lot of time thinking about these set processes from a manufacturing mindset,” he says.
“There is also definitely a lot of discussion at the global level among the Global Mining Standards Group (GMSG) and we are discussing with partners about how to really link the data and control chain together to create more value.
“I believe that’s where you are going to see a lot of innovation and development in the short to mid-term. We’re going to see key processes − drilling, blasting, shovels and transporting to the mill – really linked together from a strategic and operational standpoint in terms of tools and control.”